Today's interest in magnesium alloys for automotive applications is based on the combination of high strength properties and low density. In automotive applications weight reduction will improve the performance of a vehicle by reducing the rolling resistance and energy is used in acceleration, thus reducing fuel consumption and, moreover, a reduction in the greenhouse gas CO2 can be achieved.
In the 1920s magnesium began to make an appearance in the automotive industry. The light weight metal began to be used in racing car adding to their competitive edge. About a decade later, magnesium began to be used in commercial vehicles such as the Volkswagen Beetle which contained about 20kg (44.09lbs) of the material. Interest in using magnesium in automotive applications has increased over the past decade in response to the increasing environmental and legislative influences. Fuel efficiency, increased performance and sustainability are top-of-mind issues.
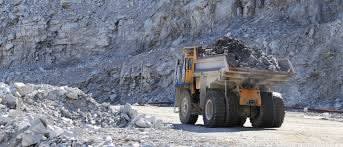
The use of magnesium in vehicles can, and does, lower overall weight and improves each of these conditions. Many large automotive companies have already replaced steel and aluminum with magnesium in various parts of their products. Audi, DaimlerChrysler (Mercedes-Benz), Ford, Jaguar, Fiat and Kia Motors Corporation are just a few of these companies. Magnesium is currently being used in gearboxes, steering columns and driver’s air bag housings as well as in steering wheels, seat frames and fuel tank covers.

The use of magnesium in automotive applications can provide more than just weight savings. For many years, the desire to identify challenges, solutions, and opportunities regarding the use of magnesium in vehicles has been growing. Magnesium usage on the front end of a vehicle provides not just a lower overall mass for the car, but also allows for the shifting of the center of gravity towards the rear improving the car’s handling and turning capabilities. In addition, frequencies that reduce vibration and overall noise can be achieved through the tuning of magnesium parts. Steel components in vehicles can be replaced by a single cast piece of magnesium adding to the strength of the material and allowing for housings to be cast into place. This castability also requires less tooling and fewer gauges, which lowers manufacturing costs.
According to the United States Automotive Materials Partnership (USAMP), it is estimated that by 2020, 350 lbs of magnesium will replace 500 lbs of steel and 130lbs of aluminum per vehicle, an overall weight reduction of 15%. In turn, this weight saving would lead to fuel savings of 9% to12% without any drastic changes in design. Considering the large number of vehicles produced worldwide, these weight savings could lead to a significant drop in the carbon dioxide released into the atmosphere, reducing its harmful impact on global warming. It is for this reason that magnesium is known as the green metal of the 21st century.
Currently, multiple automobile parts can be made from magnesium alloys such as engine block, wheels, steering columns, seats, front consoles, and hoods.
For more information, please visit http://www.samaterials.com/139-magnesium
In the 1920s magnesium began to make an appearance in the automotive industry. The light weight metal began to be used in racing car adding to their competitive edge. About a decade later, magnesium began to be used in commercial vehicles such as the Volkswagen Beetle which contained about 20kg (44.09lbs) of the material. Interest in using magnesium in automotive applications has increased over the past decade in response to the increasing environmental and legislative influences. Fuel efficiency, increased performance and sustainability are top-of-mind issues.
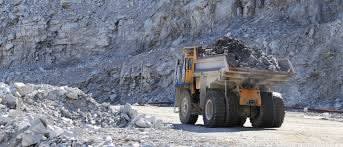
The use of magnesium in vehicles can, and does, lower overall weight and improves each of these conditions. Many large automotive companies have already replaced steel and aluminum with magnesium in various parts of their products. Audi, DaimlerChrysler (Mercedes-Benz), Ford, Jaguar, Fiat and Kia Motors Corporation are just a few of these companies. Magnesium is currently being used in gearboxes, steering columns and driver’s air bag housings as well as in steering wheels, seat frames and fuel tank covers.

The use of magnesium in automotive applications can provide more than just weight savings. For many years, the desire to identify challenges, solutions, and opportunities regarding the use of magnesium in vehicles has been growing. Magnesium usage on the front end of a vehicle provides not just a lower overall mass for the car, but also allows for the shifting of the center of gravity towards the rear improving the car’s handling and turning capabilities. In addition, frequencies that reduce vibration and overall noise can be achieved through the tuning of magnesium parts. Steel components in vehicles can be replaced by a single cast piece of magnesium adding to the strength of the material and allowing for housings to be cast into place. This castability also requires less tooling and fewer gauges, which lowers manufacturing costs.
According to the United States Automotive Materials Partnership (USAMP), it is estimated that by 2020, 350 lbs of magnesium will replace 500 lbs of steel and 130lbs of aluminum per vehicle, an overall weight reduction of 15%. In turn, this weight saving would lead to fuel savings of 9% to12% without any drastic changes in design. Considering the large number of vehicles produced worldwide, these weight savings could lead to a significant drop in the carbon dioxide released into the atmosphere, reducing its harmful impact on global warming. It is for this reason that magnesium is known as the green metal of the 21st century.
Currently, multiple automobile parts can be made from magnesium alloys such as engine block, wheels, steering columns, seats, front consoles, and hoods.
For more information, please visit http://www.samaterials.com/139-magnesium