
「このネタ。。もう、見飽きたよ」
とは、言わないでください。
今回で終わらせますんで、、おはようございます。

”ワッカ接合” 成功率、、1/3 という、
とてつもない難関を突破した、次に待っておりますのは
これまた難題、 ”アルミ溶接” でございます。
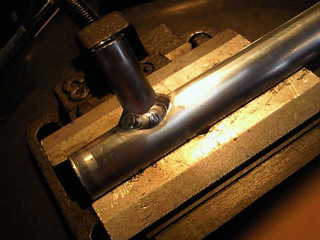
いくぶん、気が楽なのは 鋳物 ではないという点。
資材選定も #6000台 をオーダーしてありますし
最近では、レンズの使用もやめておりますので
あとは単純に、 『ウデの問題』 だけかと。。。

細いパイプは、やりにくいです。。。
溶けるスピードにトーチの角度が追いつかん・・・。
ひとつ、勉強になりました。。 と、いうより、 ”そーだった” と思い出した。
・・・を、いっぱい。

休憩と冷却を兼ねましたら
抜け防止のビード加工を施します。
コツは要るけど、そんなタイソウな作業でもない。

・・・を、いっぱい。
さすがに、こんだけヤルと、腕パンパン。
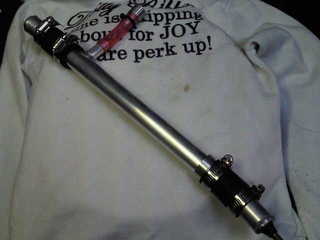
『品質管理』
と書けば、やや御立派に聞こえますが
創ったモノの良否確認は、しておかねばなりません。

検査用の治具を製作しました。
ココから、空気を注入して

他方をメクラ栓して
水中に浸しておけば
溶接部位からの ”漏れ” が
確認できるというスンポウです。

・・・を、いっぱい。
自分で立案しておきながら、言うのもナンナンですが、、、

なんとか、早く終わる方法はないものかしらと
エアゲージのレバーを目一杯、、
握りましたら、一気に MAX 15kg/cm 。
ワタクシは、びっちゃびちゃで風邪ひくゎ
鉄板ムキ出し作業台は、錆びっサビになるゎ の
ご想像通りの展開で。。。
『横着するな』 の一例でした、さようなら。
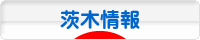
※コメント投稿者のブログIDはブログ作成者のみに通知されます