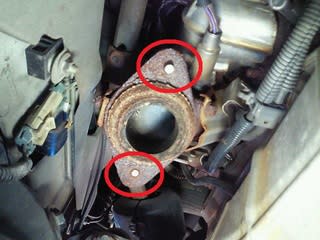
結局、、トータル、丸一日。
φ3から掘り始めた、ドリルの刃ぁ。
2mmきざみでφ9まで、各2本ずつ折損。
作業スペース不足により
超硬刃による切削に切り替えましたら
今度は、頭から細かい切り子を浴びて
チクチクとの戦いを強いられる羽目に・・・
甚大な被害すぎて笑うしかありません、おはようございます。
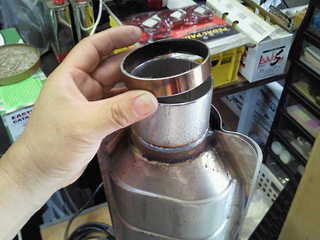
そんな苦難を乗り越えて
やっとこさ、折れたボルトの処理が終わりましたので
本来のマフラー加工へと移ることができました。
写真は、微妙に長さが足りなくて
あわててパイプを継ぎ足そうとしてるとこ。
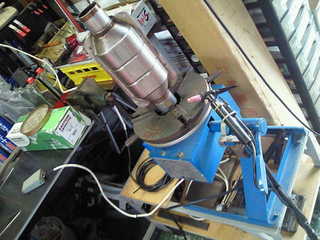
円筒なのでポジショナーを使ってみる。
・・・が
慣れてないので、めっちゃ汚い溶接になってもぉた。。。
※トーチを動かす、従来の方法でやり直しました。

一度、車輛に仮組みして
位置決め、一気にやってまう。
溶接ポイントは2箇所なので
一発で決めても大丈夫だろうと、安易な発想。
ちなみに、V型エンジンなので
仮溶接した後の、触媒付パイプは結構な大きさ・・・。
本溶接をするのに、だだっ広い基地が狭く感じますョ。

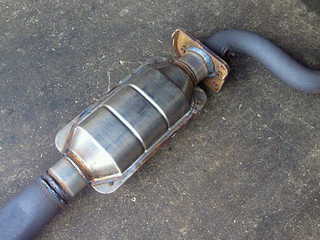
パイプを反転させるのにも、一苦労。
ひとりでドッタンバッタン、暴れながら
どうにか完成です。

嗚呼。
人手が欲しいと思う瞬間。。。
パイプを持ちながら、左右バンクのフランジにボルトを通し
出口を見据えながら、本締め作業をこなす。
「器用にやるもんだ」
と、自分で褒めておきましょう。
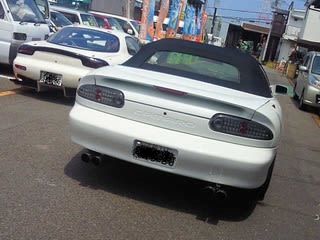
ヤったった、出来たった。。さようなら。
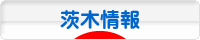
※コメント投稿者のブログIDはブログ作成者のみに通知されます