The sintering method of the silicon carbide tube mainly includes reaction sintering, pressureless sintering, hot pressing sintering, and hot isostatic pressing.
Reaction sintering is based on the reaction: 3Si(s) + 2N2(g) = Si3N4 (s) The initial temperature of the nitridation reaction is at 1100, and then gradually increases to 1420 ° C. The whole process takes several days, since the reaction is an exothermic reaction. Therefore, the heating rate should be carefully controlled. The resulting product, typically maintained at a temperature below 1400, is a mixture of alpha-, beta-Si3N4 having a porosity of 15% at 15 °C.
The advantage of reaction sintering is that no additional additives are added. Its characteristics are: 1) the strength of the material does not decrease significantly at high temperatures; 2) the size and shape of the product can be changed to produce a complex shape; 3) When welding two parts, simply connect them together for nitrogen Chemical. In reaction sintering, the key factor affecting product quality is to control the reaction temperature. The three-step heating method finally raises the furnace temperature above the melting point of silicon, often referred to as ultra-temperature nitriding.
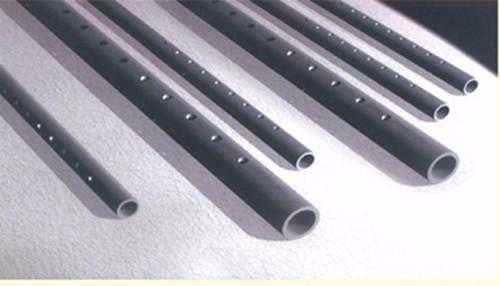
At present, in addition to reaction sintering, methods for preparing high-density silicon carbide tubes include pressureless sintering, hot pressing sintering, and hot isostatic pressing. The SiC component of complex shape and large size can be prepared by a pressureless sintering process, and thus is considered to be the most promising sintering method of SiC ceramic.
Only a simple shape of the SiC component can be prepared by the hot press sintering process, and the number of products prepared by one hot sintering process is small, which is disadvantageous for commercial production. Although the hot isostatic pressing process can obtain a SiC product of a complicated shape, the green body must be encapsulated, so that industrial production is also difficult to achieve.
The performance of SiC tubes varies depending on the sintering method. In general, the overall performance of pressureless sintered SiC tubes is superior to that of reactive sintered SiC, but inferior to hot pressed sintering and hot isostatically sintered SiC tubes.
For more information, please visit https://www.preciseceramic.com/.
Reaction sintering is based on the reaction: 3Si(s) + 2N2(g) = Si3N4 (s) The initial temperature of the nitridation reaction is at 1100, and then gradually increases to 1420 ° C. The whole process takes several days, since the reaction is an exothermic reaction. Therefore, the heating rate should be carefully controlled. The resulting product, typically maintained at a temperature below 1400, is a mixture of alpha-, beta-Si3N4 having a porosity of 15% at 15 °C.
The advantage of reaction sintering is that no additional additives are added. Its characteristics are: 1) the strength of the material does not decrease significantly at high temperatures; 2) the size and shape of the product can be changed to produce a complex shape; 3) When welding two parts, simply connect them together for nitrogen Chemical. In reaction sintering, the key factor affecting product quality is to control the reaction temperature. The three-step heating method finally raises the furnace temperature above the melting point of silicon, often referred to as ultra-temperature nitriding.
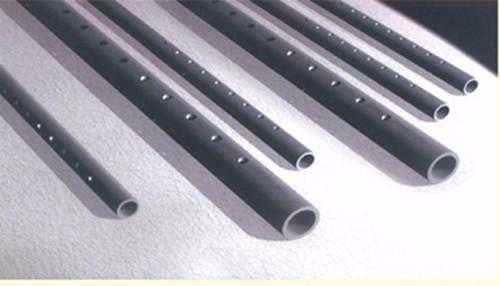
At present, in addition to reaction sintering, methods for preparing high-density silicon carbide tubes include pressureless sintering, hot pressing sintering, and hot isostatic pressing. The SiC component of complex shape and large size can be prepared by a pressureless sintering process, and thus is considered to be the most promising sintering method of SiC ceramic.
Only a simple shape of the SiC component can be prepared by the hot press sintering process, and the number of products prepared by one hot sintering process is small, which is disadvantageous for commercial production. Although the hot isostatic pressing process can obtain a SiC product of a complicated shape, the green body must be encapsulated, so that industrial production is also difficult to achieve.
The performance of SiC tubes varies depending on the sintering method. In general, the overall performance of pressureless sintered SiC tubes is superior to that of reactive sintered SiC, but inferior to hot pressed sintering and hot isostatically sintered SiC tubes.
For more information, please visit https://www.preciseceramic.com/.