当企画のガレージキットにおける各パーツの接続には現在ABS棒の埋め込みによるジョイント軸を用いております。
わざわざレジンのパーツにABS素材を埋め込む理由は、その素材の持つ耐久性や対摩耗性の高さ、特にジョイントを可動部に用いる際の「捩れ」に対する強度の高さにあるわけですが、別素材を埋め込むデメリットとしてパーツ本体と完全に融着しているわけでは無いので軸が抜ける可能性もあります。
そこで軸の埋め込まれる面になるべくパーツ本体のレジンが食いついて脱落しない様な加工を施す必要があるわけですが、これまでも試行錯誤がありました。
最初の頃に行ったのは軸に対して直角に針金を通して固定する事でギャップを形成させ、脱落を防止しようという試みです↓
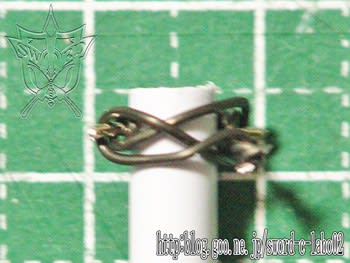
レジンの注型時、針金の隙間にレジンが流れ込んで硬化する事でがっちりとホールドされる…という寸法でしたが、この針金を軸一本一本に取り付ける作業はおそろしく面倒臭く、これは早々に挫折してしまいました
次に試したのが軸に穴を開けてそこにレジンを流し込もうという案↓

発想としては悪くなかったと思うのですが、時折大きめの気泡が発生する事が判ってこれまた頓挫。
そして現在用いているのがニッパーとカッターで切り欠きを作る方法↓
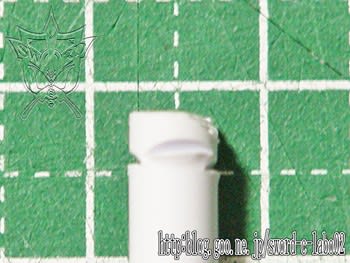
一見雑な方法に見えますが、これが意外に効果的で、軸が抜け落ちる確率も飛躍的に低くなりました。(「低くなった」と書くのはもちろん可能性が0%ではないという事で、例えばアジャストが不十分でジョイント孔が極端にきつい場合は無理をすると軸が外れてしまう可能性はありますし、軸をペンチなどで無理やり捩じればさすがに外れてしまいます)
さて、これまでは殆ど5㎜ジョイントで構成していたため軸の固定はこれで十分だったのですが、モノグラス制作においては軸の固定に再検討が必要となりました。
これは以前グラニの馬形態時の膝関節等の時から懸念されていた事なのですが、切り欠きの方法ですと3㎜ABS棒の場合、若干強度に不安が出てしまうためです。
そのため今回のビギナーズモデル版モノグラスからは3㎜ジョイントに限って先端を熱して潰す…という方法を採る事にしました↓

切り欠き法に比べると少しだけ手間はかかりますが、まぁ許容範囲…という事で有効なのではないかと考えます。
もちろんこれからじっくりと検証も行う予定ですが、経験的にはたぶん問題はない…かなぁ?…と考える次第です。
ガレージキット制作は模索の積み重ね…見えない部分で日々進歩、しております。
わざわざレジンのパーツにABS素材を埋め込む理由は、その素材の持つ耐久性や対摩耗性の高さ、特にジョイントを可動部に用いる際の「捩れ」に対する強度の高さにあるわけですが、別素材を埋め込むデメリットとしてパーツ本体と完全に融着しているわけでは無いので軸が抜ける可能性もあります。
そこで軸の埋め込まれる面になるべくパーツ本体のレジンが食いついて脱落しない様な加工を施す必要があるわけですが、これまでも試行錯誤がありました。
最初の頃に行ったのは軸に対して直角に針金を通して固定する事でギャップを形成させ、脱落を防止しようという試みです↓
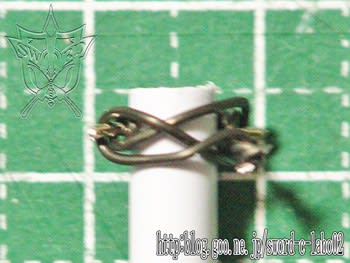
レジンの注型時、針金の隙間にレジンが流れ込んで硬化する事でがっちりとホールドされる…という寸法でしたが、この針金を軸一本一本に取り付ける作業はおそろしく面倒臭く、これは早々に挫折してしまいました

次に試したのが軸に穴を開けてそこにレジンを流し込もうという案↓

発想としては悪くなかったと思うのですが、時折大きめの気泡が発生する事が判ってこれまた頓挫。
そして現在用いているのがニッパーとカッターで切り欠きを作る方法↓
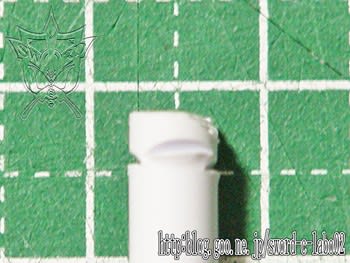
一見雑な方法に見えますが、これが意外に効果的で、軸が抜け落ちる確率も飛躍的に低くなりました。(「低くなった」と書くのはもちろん可能性が0%ではないという事で、例えばアジャストが不十分でジョイント孔が極端にきつい場合は無理をすると軸が外れてしまう可能性はありますし、軸をペンチなどで無理やり捩じればさすがに外れてしまいます)
さて、これまでは殆ど5㎜ジョイントで構成していたため軸の固定はこれで十分だったのですが、モノグラス制作においては軸の固定に再検討が必要となりました。
これは以前グラニの馬形態時の膝関節等の時から懸念されていた事なのですが、切り欠きの方法ですと3㎜ABS棒の場合、若干強度に不安が出てしまうためです。
そのため今回のビギナーズモデル版モノグラスからは3㎜ジョイントに限って先端を熱して潰す…という方法を採る事にしました↓

切り欠き法に比べると少しだけ手間はかかりますが、まぁ許容範囲…という事で有効なのではないかと考えます。
もちろんこれからじっくりと検証も行う予定ですが、経験的にはたぶん問題はない…かなぁ?…と考える次第です。
ガレージキット制作は模索の積み重ね…見えない部分で日々進歩、しております。