



Paulson Training - Extruder Operation & Control: Single Screw
http://www.cjindustries.com/Injection-molding-resources/injection-molding-glossary.html
Plastic Injection Mold
A
AGING - The change of a material with time under defined environmental conditions, leading to improvement or deterioration of properties.
ALLOY - Composite material made up by blending polymers or copolymers with other polymers or elastomers under selected conditions. e.g. , styrene-acrylonitrile copolymer resins blended with butadiene-acrvlonitrile rubbers.
ANNEAL - (1) To heat a molded plastic article to a predetermined temperature and slowly cool it. to relieve stresses. (2) To heat steel to a predetermined temperature above the critical range and slowly cool it, to relieve stresses and reduce harness. (Annealing of molded or machined parts may be done dry as in an oven or wet as in a heated tank of mineral oil.)
ANTISTATIC AGENT - Agents which, when added to the molding material or applied on the surface of the molded object, make it less conducting (thus hindering the fixation of dust).
AUTOMATIC MOLD - A mold for injection, compression or transfer molding that repeatedly goes through the entire molding cycle, including ejection, without human assistance.
AUTOMATIC MOLD - A mold for injection, compression or transfer molding that repeatedly goes through the entire molding cycle, including ejection, without human assistance.
« return to top
B
BACK TAPER - Reverse draft used in mold to prevent molded articles from drawing freely. See UNDERCUT.
BACKING PLATE - In mold construction, a plate used as a support for the cavity blocks, guide pins, bushings, etc.
BLEED - (1) To give up color when in contact with water or a solvent. (2) Undesired movement ot certain materials in a plastic (e.g. plasticizers in vinyl) to the surface of the finished article or into an adjacent material. Also called "Migration." (3) An escape passage at the parting line of a mold, like a vent but deeper, which allows material to escape or bleed out.
BLISTER - A raised area on the surface of a molding caused by the pressure of gases inside it on its incompletely hardened surface.
BLOOM - A visible exudation or efflorescence on the surface of a plastic. Bloom can be caused by lubricant, plasticizer, etc.
BLOW MOLDING - A method of fabrication of thermoplastic materials in which a parison (hollow tube) is forced into the shape of the mold cavity by internal air pressure. BLUE1NG OFF ― The checking of the accuracy of mold cutoff surfaces by putting a thin coating of Prussian Blue on one-half and checking the blue transfer to the other half.
BOSS - Projection on a plastic part designed to add strength, to facilitate alignment during assembly, to provide for fastenings, etc.
BREATHING - The opening and closing of a mold to allow gases to escape early in the molding cycle. Also called degassing.
BRINELL HARDNESS - Similar to ROCKWELL HARDNESS
BUBBLE - A spherical. internal void of air or other gas trapped within a plastic. See VOID.
BUBBLER - A device inserted into a mold cavity or core, which allows water to flow deep inside the hole into which it is inserted and to discharge through the open end of hole. Uniform cooling of the molds and of isolated mold sections can be achieved in this manner.
BURNED - Showing evidence of thermal decomposition through some discoloration, distortion. or localized destruction of the surface of the plastic.
« return to top
C
CARBON BLACK - A black pigment produced by the incomplete burning of natural gas or oil. It is widely used as a filler, particularly in the rubber industry. Because it possesses useful ultraviolet protective properties. It is also much used in molding compounds intended for outside weathering applications.
CASE HARDEN - To harden surface of a piece of steel to a relatively shallow depth.
CAST - To form a "plastic" object by pouring a fluid monomer-polymer solution into an open mold where it finishes polymerizing.
CAVITY - Depression in mold, which usually forms the outer surface of the molded part; depending on number of such depressions, molds are designated as a single cavity or multi-cavity.
CENTER GATED MOLD - An injection or transfer mold wherein the cavity is filled with molding material through a sprue or gate directly into the center of the part.
CHALKING - Dry. chalk-like appearance or deposit on the surface of a plastic. See HAZE and BLOOM.
CHROMIUM PLATING - An electrolytic process that deposits a hard film of chromium metal onto working surfaces of other metals where resistance to corrosion, abrasion. and/or erosion is needed.
CLAMPING PLATE - A plate fitted to a mold and used to fasten mold to a molding machine.
CLAMPING FORCE - In injection molding and in transfer molding, the pressure which is applied to the mold to keep it closed, in opposition to the fluid pressure of the compressed molding material, within the mold cavity (cavities) and the runner system.
COLD FLOW - See CREEP.
COLD SLUG - The first material to enter an injection mold. So called because in passing through the sprue orifice it is cooled below the effective molding temperature.
COLD SLUG WELL - Space provided directly opposite the sprue opening in an injection mold to trap the cold slug.
COMBINATION MOLD - See FAMILY MOLD.
COMPRESSION MOLD - A mold which is open when the material is introduced and which shapes the material by heat and by the pressure of closing.
COMPRESSION MOLDING - A technique of thermoset molding in which the molding compound (generally preheated) is placed in the heated open mold cavity, mold is closed, under pressure (usually in an hydraulic press) causing the material to flow and completely fill the cavity, pressure being held until the material has cured.
COMPRESSION RATIO - In an extruder screw, the ratio of volume available in the first flight at the hopper to the last flight at the end of the screw.
COMPRESSIVE STRENGTH - Crushing load at the failure of a specimen divided by the original sectional area of the specimen.
CONCENTRICITY - Relationship of all inside dimensions to all outside dimensions. usually as with diameter expressed in thousandths of an inch T1R (Total Indicator Reading)
COOLING CHANNELS - Channels or passageways located within the body of a mold through which a cooling medium can be circulated to control temperature on the mold surface. May also be used for heating a mold by circulating steam. hot oil or other heated fluid through channels as in molding of the thermosetting and some thermoplastic materials.
COOLING FIXTURE - Block of metal or wood holding the shape of a molded piece which is used to maintain the proper shape or dimensional accuracy of a molding after it is removed from the mold until it is cool enough to retain its shape without further appreciable distortion. Also called: ‘Shrink Fixture.
COPOLYMER - See POLYMER.
CORE - (1) Male element in a die which produces a hole or recess in part. (2) Part of a complex mold that molds undercut parts. Cores are usually withdrawn to one side before the main sections of the mold opens. (Usually called Side Cores). (3) A channel in a mold for circulation of a heat-transfer medium. Also called "Force."
CORE PIN - Pin used to mold a hole.
CORING - (molded part design) ― The removal of excess material from the cross section of a molded part to attain a more uniform wall thickness.
CRAZING - Fine cracks which may extend in a network on or under the surface or through a layer of plastic material.
CREEP - The dimensional change with time of a material under load, following the initial instantaneous elastic deformation. Creep at room temperature is sometimes called "Cold Flow".
CRYSTALLINITY - A state of molecular structure in some resins which denotes uniformity and compactness of the molecular chains forming the polymer. Normally can be attributed to the formation of solid crystals having a definite geometric form.
CURE - To change the physical properties of a material by chemical reaction, which may be condensation. polymerization. or vulcanization: usually accomplished by the action of heat and catalysts. along or in combination. with or without pressure.
CURING TEMPERATURE - Temperature at which a cast, molded or extruded product, a resin-impregnated reinforcing material, or adhesive. etc., is subjected to curing.
CYCLE - The complete, repeating sequence of operations in a process or part of a process. In molding. the cycle time is the period, or elapsed time between a certain point in one cycle and the same point in the next.
« return to top
D
DAYLIGHT OPENING - Clearance between two platens of a press in the open position.
DIAPHRAGM GATE - Gate used in molding annular or tubular articles. Gate forms a solid web across the opening of the part.
DEFLASHING - Covers the range of finishing techniques used to remove the flash (excess, unwanted material) on a plastic molding such as filing, sanding. milling, tumbling, etc.
DEGASSING - See BREATHING.
DEGRADATION - A deleterious change in the chemical structure of a plastic. See DETERIORATION.
DELAMINTATION - The splitting of a plastic material along the plane of its layers. Physical separation or loss of bond between laminate plies. See LAMINATE.
DENSITY - Weight per unit volume of a substance. expressed in grams per cubic centimeter, pounds per cubic foot, etc.
DESSICANT - Substance which can be used for drying purposes because of its affinity for water.
DESTATICIZATION - Treating plastics materials to minimize their accumulation of static electricity, and subsequently. the amount of dust picked up by the plastics because of such charges. See ANTISTATIC AGENTS.
DETERIORATION - A permanent change in the physical properties of a plastic evidenced by impairment of these properties.
DIELECTRIC - Insulating material. In radio frequency preheating, dielectric may refer specifically to the material which is being heated.
DIMENSIONAL STABILITY - Ability of a plastic part to retain the precise shape in which it was molded, fabricated. or cast.
DISCOLORATION - Any change from the original color, often caused by overheating, light exposure irradiation or chemical attack.
DISHED - Showing a symmetrical distortion of a flat or curved section of a plastic object, so that, as normally viewed, it appears concave, or more concave than intended. See―WARP.
DISPERSION - Finely divided particles of a material in suspension in another substance.
DOMED - Showing a symmetrical distortion of a flat or curved section of a plastic object, so that, as normally viewed, it appears convex, or more convex than intended. See―WARP.
DOWEL - Pin used to maintain alignment between two or more parts of a mold.
DRAFT - The degree of taper of a side wall or the angle of clearance designed to facilitate removal of parts from a mold.
DRY COLORING - Method commonly used by fabricators for coloring plastic by tumble blending uncolored particles of the plastic material with s1ected dyes and pigments.
DUROMETER HARDNESS - The hardness of a material as measured by the Shore Durometer.
DWELL - A pause in the application of pressure to a mold made just before the mold is completely closed, to allow the escape of gas from the molding material.
« return to top
E
EJECTOR PIN - Or ejector sleeve. A rod, pin or sleeve which pushes a molding off of a core or out of a cavity of a mold. It is attached to an ejector bar or plate which can be actuated by the ejector rod(s) of the press or by auxiliary hydraulic or air cylinders.
EJECTOR PIN RETAINER PLATE - Retainer into which ejector pins are assembled.
EJECTOR RETURN PINS - Projections that push the ejector assembly back as the mold closes: also called Safety Pin, and Position Pushbacks.
EJECTOR ROD & BAR - Bar that actuates the ejector assembly when mold is opened.
ELASTICITY - That property of a material by virtue of which it tends to recover its original size and shape after deformation.
ELASTOMER - A material which at room temperature stretches under low stress to at least twice its length and snaps hack to the original length upon release of stress. See
RUBBER.
ELECTRIC DISCHARGE MACHINING (EDM) - A metal working process applicable to mold construction in which controlled sparking is used to erode away the work piece.
ELECTRONIC TREATING - A method of oxidizing a film of polyethylene to render it printable by passing the film between electrodes and subjecting it to a high voltage corona discharge.
ELECTROPLATING - Deposition of metals on certain plastics and molds for finish.
ELONGATION - The fractional increase in length of a material stressed in tension.
EMBOSSING - Techniques used to create depressions of a specific pattern in plastics film and sheeting. Such embossing in the form of surface patterns on molded part by the treatment of the mold surface by photoengraving or other process.
ENCAPSULATING - Enclosing an article (usually an electronic component or the like) in a closed envelope of plastic, by immersing the object in a casting resin and allowing the resin to polymerize or, if hot, to cool. See POTTING.
ENVIRONMENTAL STRESS CRACKING (ESC) - The susceptibility of a thermoplastic article to crack, or craze formation under the influence of certain chemicals or aging, or weather, and stress.
EXTRUSION - The compacting of a plastic material and the forcing of it through an orifice in more or less continuous fashion.
« return to top
F
FABRICATE - To work a material into a finished form by machining, forming, or other operation.
FAMILY MOLD - A multi-cavity mold wherein each of the cavities forms one of the component parts of the assembled finished object. The term often applied to molds wherein parts from different customers are grouped together in one mold for economy of production. Sometimes called "Combination Mold."
FAN GATE - A shallow gate somewhat wider than the runner from which it extends.
FIBER - This term usually refers to thin fibers of glass which are used to reinforce both thermoplastic and thermosetting materials. One-inch long fibers are occasionally used, but the more commonly used fiber lengths are 1/2" and 1/4", or less.
FILLER - An additive to resins for the purpose of improving physical properties (impact resistance, hardness, dimensional stability, etc.), or to reduce cost of resin.
FILLET - A rounded filling of the internal angle between two surfaces.
FINISH - To complete the secondary work on a molded part so that it is ready for use. Operations such as filing, deflashing, buffing, drilling, tapping. degating are commonly called finishing operations. See SURFACE FINISH
FIXTURE - Means of holding a part during a machining or other operation.
FLASH - Extra plastic attached to a molding along the parting line; under most conditions it would be objectionable and must be removed before the parts are acceptable.
FLASH GATE - Usually a long gate extending from a runner which runs parallel to an edge of a molded part along the flash or parting line of the mold.
FLEXURAL STRENGTH - Ability of a material to flex without permanent distortion or breaking.
FLOW - A qualitative description of the fluidity of a plastic material during the process of molding.
FLOW LINE - A mark on a molded piece made by the meeting of two flow fronts during molding. Also called "Weld Line."
FLOW MARKS - Wavy surface appearance on a molded object caused by improper flow of the material into the mold. See SPLAY MARKS.
FOIL DECORATING - Molding paper, textile, or plastic foils printed with compatible inks directly into a plastic part so that the foil is visible below the surface of the part as integral decoration.
FRICTION WELDING - See SPIN WELDING.
« return to top
G
GATE - In injection and transfer molding, the orifice through which the melt enters the cavity.
GLOSS - The shine or luster of the surface of a material. See SURFACE FINISH.
GUIDE PINS - Devices that maintain proper alignment of core and cavity as mold closes. Also called "Leader Pins."
« return to top
H
HARDNESS - The resistance of a material to compression and indentation. Among the most important methods of testing this property are Brinell hardness, Rockwell hardness and Shore hardness.
HAZE - The degree of cloudiness in a plastics material.
HEAT-DISTORTION POINT - The temperature at which a standard test bar deflects 0.010 in. under a stated load of either 66 or 264 psi.
HOT-RUNNER MOLD - A thermoplastic injection mold in which the runners are insulated from the chilled cavities and remain hot so that the center of the runner never cools in normal cycle operation. Runners are not, as is the case usually, ejected with the molded pieces.
HOT/HEATED MANIFOLD MOLD - A thermoplastic injection mold in which the portion of the mold which contains the runner system has its own heating elements which keep the molding material in a plastic state ready for injection into the cavities, from which the manifold is insulated.
HOT-STAMPING - Engraving operation for marking plastics in which roll leaf is stamped with heated metal dies onto the face of the plastics.
HYGROSCOPIC - Tending to absorb moisture.
« return to top
I
IMPACT STRENGTH - (1) The ability of a material to withstand shock loading. (2) The work done in fracturing, under shock loading, a specified test specimen in a specified manner. (3) Molded plastics are usually given a value on an izod scale. An Izod impact test is designed to determine the resistance of a plastics material to a shock loading, it involves the notching of a specimen, which is then placed in the jaws of the machine and struck with a weighted pendulum.
INJECTION MOLDING - A molding procedure whereby a heat-softened plastic material is forced from a cylinder into a cavity which gives the article the desired shape. Used with both thermoplastic and thermosetting materials.
INJECTION BLOW MOLDING - A blow molding process in which the parison to be blown is formed by injection molding.
INSERT - An integral part of a plastics molding consisting of metal or other material which may he molded into position or may be pressed into the molding after the molding is completed. Also a removable or interchangeable component of the mold.
« return to top
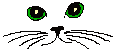




※コメント投稿者のブログIDはブログ作成者のみに通知されます