あけましておめでとうございます。
本年も宜しくお願い致します。
気が付けば1月も終わり2月も半ばに入ろうとしています。
確定申告に必要な帳簿や領収書などを税理士さんに持参し、
令和2年分の申告手続きをお願いしましたが、
コロナ禍で退去者が多く、部屋の修繕と外壁工事などで大赤字の一年になりました。
地域差はあるものの少子化、世帯数減少など賃貸経営は難しくなっています。
退職金を原資に賃貸経営をお考えの方、絶対お止めになった方が良いと思います。
儲からないなら止めた方が良いよな!
俺はやらないよ!
・・・俺はやるよ!
・・・俺もやるよ!
じゃあ、俺がやるよ!
・・・「どうぞ、どうぞ!」
「チキショ~」
♬「儲からなくってゴメンね、賃貸経営」♬ ってならないために。
注釈:ダチョウ倶楽部さんの鉄板ネタをパクりました。ごめんなさい!
落ちが付いたところで、
昨年投稿したタイヤ編(7)の補足です。
相変わらず文書を纏めるのが下手で申し訳ございません!
タイヤ編(7)の内容で、高速ユニフォーミティを測定するドラムの場合、
ドラムの釣合い良さを6.3G以下にする必要がありますと説明しましたが、
「釣合い良さ6.3Gとは何ぞや」と思った方、いらっしゃるかと思います。
まず「釣合い良さ」とは何かを考えてみます。
JISハンドブック 機械要素 : B 0905-1992を参考に説明すると、
二つの軸受で支持された状態で、目標とする任意の回転速度まで撓まないロータ(回転体+回転軸)を剛性ロータとします。
その剛性ロータの釣合い程度を示す量を「釣合い良さ」と言います。
別の言い方では、剛性ロータの質量分布がどれだけ均等であるかを表す量と言い、
計算式で表すと比不釣合いの大きさe(mm)と、ある指定された角速度ω(rad/s)との積と定義されます。
釣合い良さ(mm/s) = eω・・・①
角速度ω(rad/s)と回転速度n(min^-1)の関係は、ω = 2πn / 60 ですから、
回転数を使い計算する場合は下記の式になります。
釣合い良さ(mm/s) = en / 9.55・・・②
注釈:角速度ωは1秒間当たり何度変化したかを表し、角度の単位はラジアン(rad)を使用します。
180度 = π(rad)ですから360度 = 2π(rad)、回転数は1分間(min)に何回転したかを表します。
よって回転数(min^-1)を用いて角速度ω(rad/s)を計算する場合、2π / 60を回転数nに掛け合わせます。
比不釣合いとは剛性ロータに於いて、静不釣合い : mrをロータの質量:Mで割った量で、
ロータの質量中心の軸中心線からの偏りに等しい。
<参考図>
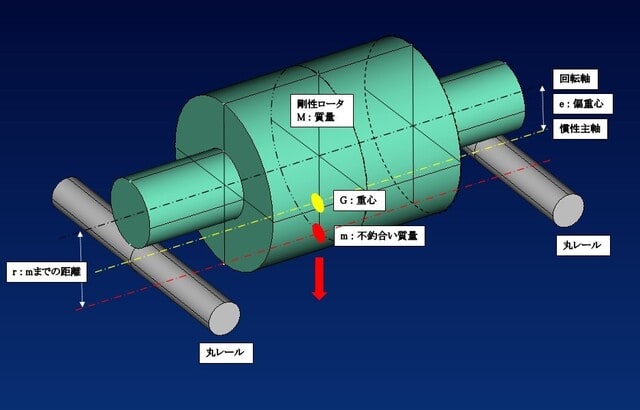
計算式で表すと、比不釣合い e(mm) = mr / M ・・・偏重心
静不釣合い = mr(gmm又はkgmm) ・・・静アンバランス
不釣合い質量 : m(g又はkg)
剛性ロータ質量 : M(g又はkg)
回転中心から不釣合い質量までの距離 : r(mm)
又、JISハンドブック 機械要素 : JIS B 0905では、「釣合い良さ等級」から「釣合い等級の上限値」を定め、
各種回転機械の釣合い良さの推奨値を提示しています。
誤記などございましたらお知らせください。
次回はこの続きから
本年も宜しくお願い致します。
気が付けば1月も終わり2月も半ばに入ろうとしています。
確定申告に必要な帳簿や領収書などを税理士さんに持参し、
令和2年分の申告手続きをお願いしましたが、
コロナ禍で退去者が多く、部屋の修繕と外壁工事などで大赤字の一年になりました。
地域差はあるものの少子化、世帯数減少など賃貸経営は難しくなっています。
退職金を原資に賃貸経営をお考えの方、絶対お止めになった方が良いと思います。
儲からないなら止めた方が良いよな!
俺はやらないよ!
・・・俺はやるよ!
・・・俺もやるよ!
じゃあ、俺がやるよ!
・・・「どうぞ、どうぞ!」
「チキショ~」
♬「儲からなくってゴメンね、賃貸経営」♬ ってならないために。
注釈:ダチョウ倶楽部さんの鉄板ネタをパクりました。ごめんなさい!
落ちが付いたところで、
昨年投稿したタイヤ編(7)の補足です。
相変わらず文書を纏めるのが下手で申し訳ございません!
タイヤ編(7)の内容で、高速ユニフォーミティを測定するドラムの場合、
ドラムの釣合い良さを6.3G以下にする必要がありますと説明しましたが、
「釣合い良さ6.3Gとは何ぞや」と思った方、いらっしゃるかと思います。
まず「釣合い良さ」とは何かを考えてみます。
JISハンドブック 機械要素 : B 0905-1992を参考に説明すると、
二つの軸受で支持された状態で、目標とする任意の回転速度まで撓まないロータ(回転体+回転軸)を剛性ロータとします。
その剛性ロータの釣合い程度を示す量を「釣合い良さ」と言います。
別の言い方では、剛性ロータの質量分布がどれだけ均等であるかを表す量と言い、
計算式で表すと比不釣合いの大きさe(mm)と、ある指定された角速度ω(rad/s)との積と定義されます。
釣合い良さ(mm/s) = eω・・・①
角速度ω(rad/s)と回転速度n(min^-1)の関係は、ω = 2πn / 60 ですから、
回転数を使い計算する場合は下記の式になります。
釣合い良さ(mm/s) = en / 9.55・・・②
注釈:角速度ωは1秒間当たり何度変化したかを表し、角度の単位はラジアン(rad)を使用します。
180度 = π(rad)ですから360度 = 2π(rad)、回転数は1分間(min)に何回転したかを表します。
よって回転数(min^-1)を用いて角速度ω(rad/s)を計算する場合、2π / 60を回転数nに掛け合わせます。
比不釣合いとは剛性ロータに於いて、静不釣合い : mrをロータの質量:Mで割った量で、
ロータの質量中心の軸中心線からの偏りに等しい。
<参考図>
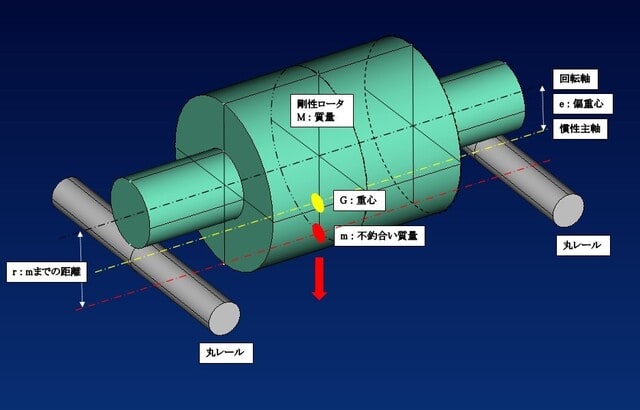
計算式で表すと、比不釣合い e(mm) = mr / M ・・・偏重心
静不釣合い = mr(gmm又はkgmm) ・・・静アンバランス
不釣合い質量 : m(g又はkg)
剛性ロータ質量 : M(g又はkg)
回転中心から不釣合い質量までの距離 : r(mm)
又、JISハンドブック 機械要素 : JIS B 0905では、「釣合い良さ等級」から「釣合い等級の上限値」を定め、
各種回転機械の釣合い良さの推奨値を提示しています。
誤記などございましたらお知らせください。
次回はこの続きから