今回は生産管理システムで重要な要件である製造場所と保管場所についてご紹介いたします。
ERPなど生産管理システムには、製造場所と保管場所が存在します。
1.品目の遷移
完成品 FG (Finished Goods)
↑
中間品 WIP (Work In Progress) ※仕掛品
↑
原材料 RM (Raw Material)
注)資材(原材料) → 完成品もあります。
2.製造場所と保管場所
製造場所は完成商品または中間品を製造する場所であり、それらの下位構成品が消費される場所でもあります。
保管場所は製造した品目を一時的に保管しておく場所および仕入先(供給先)から入荷したものを一時的に保管してく場所です。
3.在庫の出庫と消費
生産計画が立案され、現場に指示がだされると、まず原材料に対する出庫指示が行われます。
①原材料の保管場所から出庫され、現物は上位品目(完成商品、中間品)の製造場所に移動されます。
②上位品目にて原材料が消費され、上位品目が完成し保管されます。(この時点では上位品目の製造場所と保管場所は同一になります。)
③次に、完成した中間品の更に上位品目の製造場所へ現物を移動します。
完成商品が生産されるまで、出庫、生産・消費、移動が繰り返されます。
システムを運用するにあたり、BOMの階層を深くし過ぎると、下線部分の処理も比例して増加してしまいます。それらに伴って製造場所、保管場所の設定も増加します。
但し、中間品(A) → 中間品(B)・完成商品の生産において、消費される中間品(A)の保管場所と、生産される中間品(B)・完成商品の製造場所が同じ場合は、中間品(A)の移動は発生しません。
製造場所(保管場所)
中間品(B)・完成商品 製造1部
↑ (移動しない)
中間品(A) 製造1部
↑ (移動)
原材料 材料倉庫
☞ システムの仕組みとして、品目により以下の機能が必要となります。
・出庫させるもの、出庫させないもの
・出庫する保管場所
注)原材料 → 中間品(A)の時、原材料の保管場所と中間品(A)の製造場所が同じであっても、原材料を計量するため出庫する場合があります。 ※装置系(プロセス系)
注)Profit生産販売管理システムでは、実際に移動データを作成し、上位品目の製造場所へ原材料の在庫を更新させることはしていません。
(出庫データは作成します。)
※仕掛品としての棚卸は別の方法で実現します。
4.仕組み
4.1.商品マスタ
1)基本画面
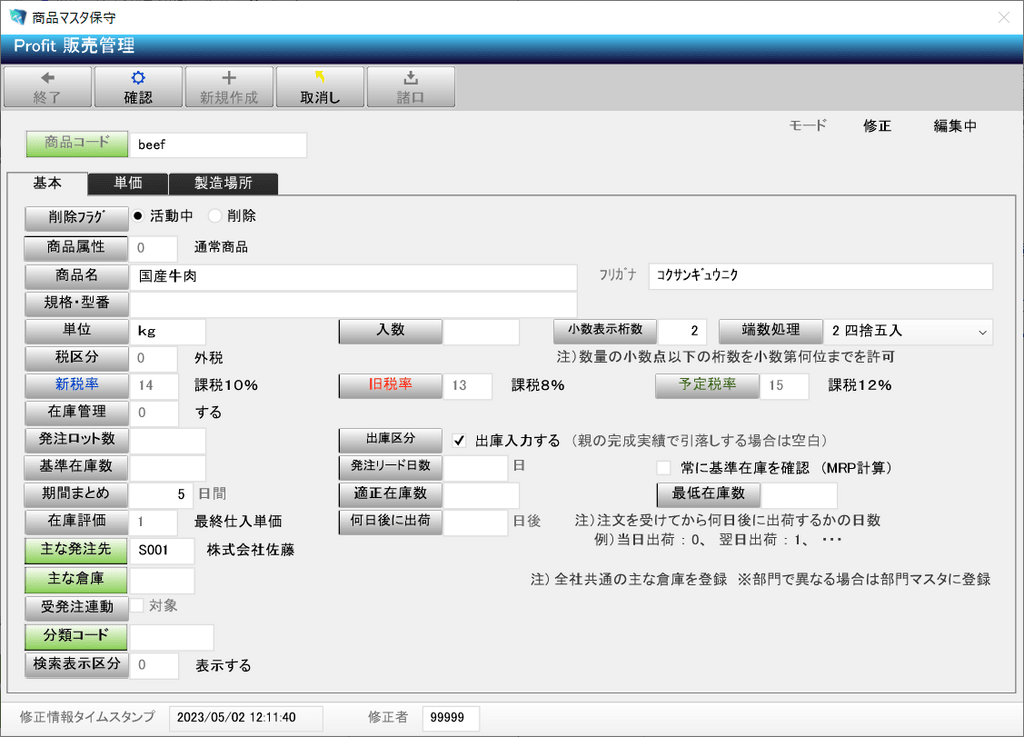
出庫区分:☑ 出庫入力する
チェックした場合、出庫入力の対象となります。
チェックしない場合、親(上位品目)の完成入力と同時に引落しされます。
最低在庫数:(後述記載)
2)製造場所(保管場所)
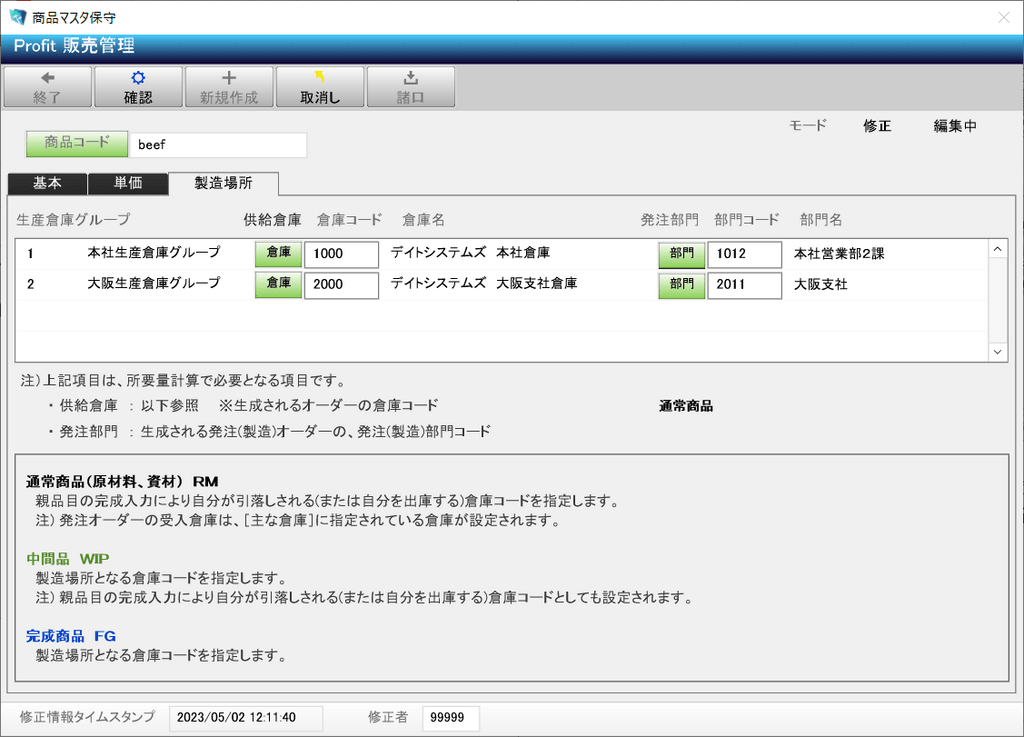
通常商品(原材料、資材) RM
親品目の完成入力により自分が引落しされる(または自分を出庫する)倉庫コードを指定します。
注) 発注オーダーの受入倉庫は、[主な倉庫]に指定されている倉庫が設定されます。
☞ 原材料の倉庫が複数登録されている場合
ア. 消費(引落される)倉庫
イ. 仕入先から入荷され、保管する倉庫
「最低在庫数」を設定することで、所要量計算とは別に、ア.倉庫の在庫がチェックされ、不足している場合は、イ.倉庫から移動伝票を一括作成します。
中間品 WIP
製造場所となる倉庫コードを指定します。
注) 親品目の完成入力により自分が引落しされる(または自分を出庫する)倉庫コードとしても設定されます。
完成商品 FG
製造場所となる倉庫コードを指定します。
4.2.補足 (生産倉庫マスタ)
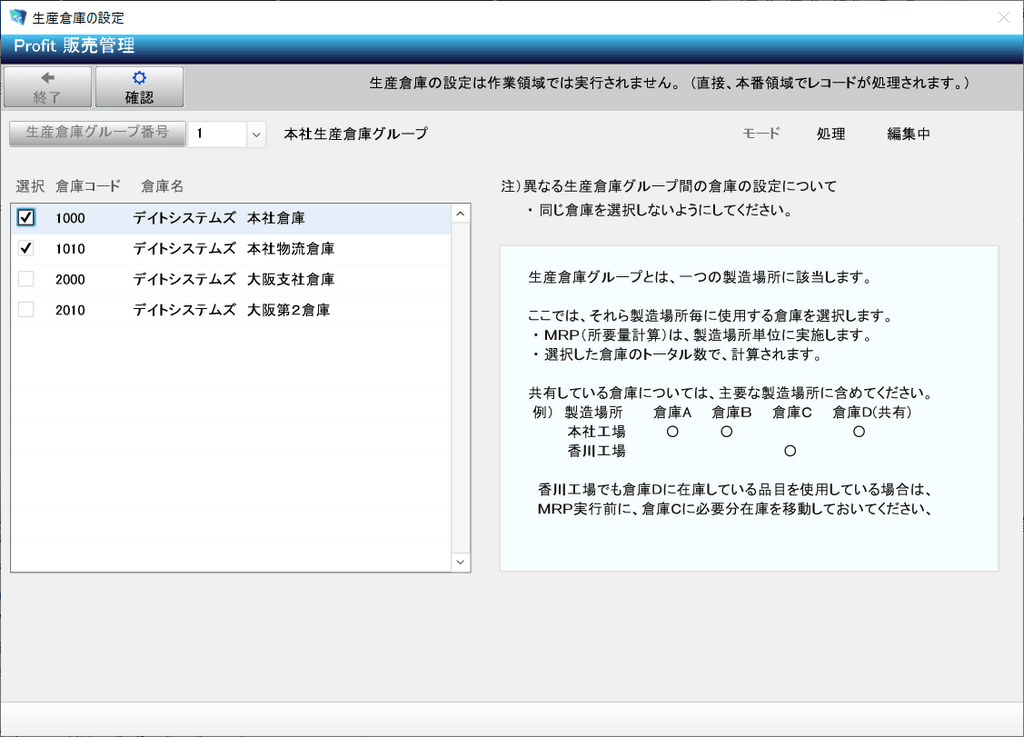
以上です。
P.S
かみゅーのホームページ
https://www.date-systems.com/