現在従事している工場での業務に集中していましたのでブログおよびそれらに付随する設計開発が停止状態でした。
今後は製造工場でのERPシステム、それらの利用範囲、補完システムの必要性、使われないERPの仕組みと要因などをご紹介したいと思います。
今後は製造工場でのERPシステム、それらの利用範囲、補完システムの必要性、使われないERPの仕組みと要因などをご紹介したいと思います。
特に「様々な課題をどう克服していくか」など
・在庫精度が向上しない要因
・部品の出庫指示、ピッキングでのチェックの仕組み
・旧部品から新部品への切替の連携と現場に必要な仕組み
・計画変更の連絡と各部門での意思決定と指示に乖離がないか
・工程間進捗とチェックの仕組み・・・etc
取り急ぎ今回はHPに掲載している記事をご紹介といたします。
これらは昨年から私個人が設計、開発してきた製造向けシステムです。
これらは昨年から私個人が設計、開発してきた製造向けシステムです。
1.システム概要図
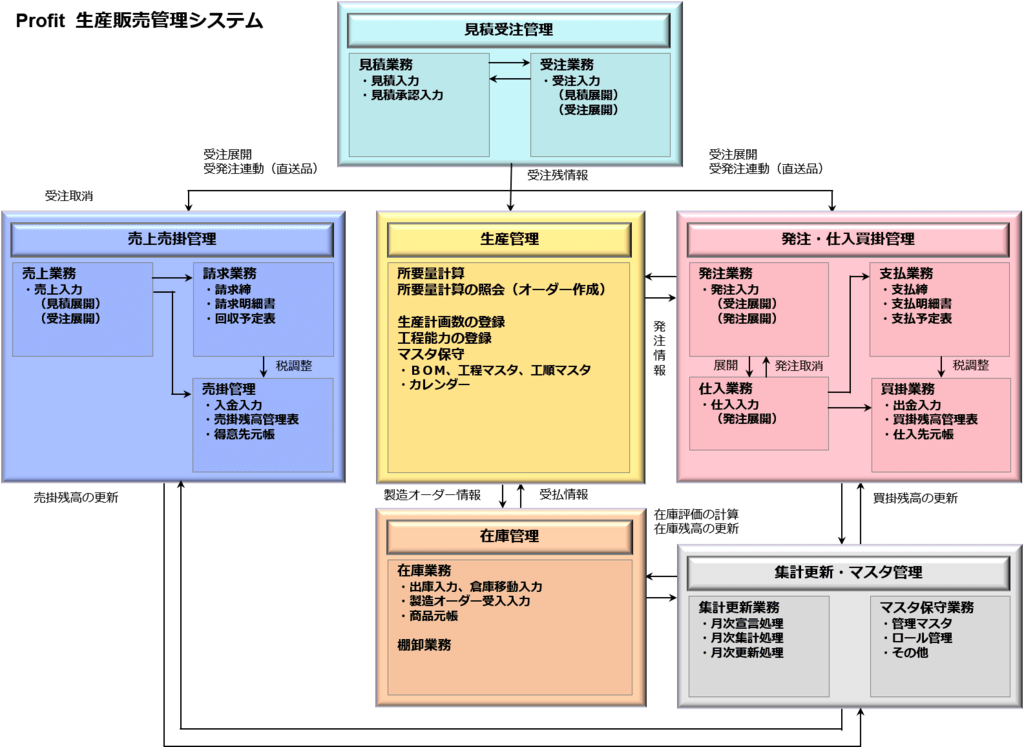
2.MRP実行結果の照会画面
1)第1画面 MRP 検索および発注伝票/製造伝票の作成指示
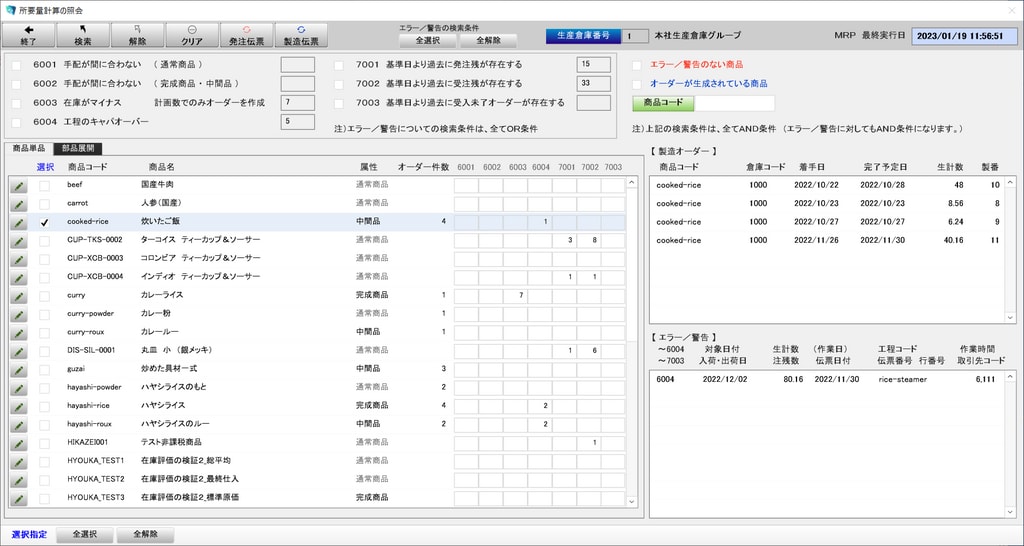
MRP(資材所要量計画)の実行結果を表示する照会画面です。
部品展開にて生成された品目およびそれ以外(商品単品)の品目が混在して表示されています。
・最初に、エラーまたは警告を確認し是正します。
特に工程のキャパオーバーに対しては以下の措置を検討し実施します。
①当該日の工程能力を増やす ※台数(人数)または稼働率
②当該日の作業時間を増やす ※残業
最終的な措置としては、
③生産計画数を変更する(無理な計画)
④顧客の希望納期を変更する ※受注生産の品目の場合
・次に、実際の発注伝票および製造伝票を作成します。
これらは、オーダー日付(発注日、製造着手日)を指定することにより、必要な期間(確定期間)までのオーダーを対象として作成することができます。
(以下の画面は、部品展開された品目のみを表示しています。
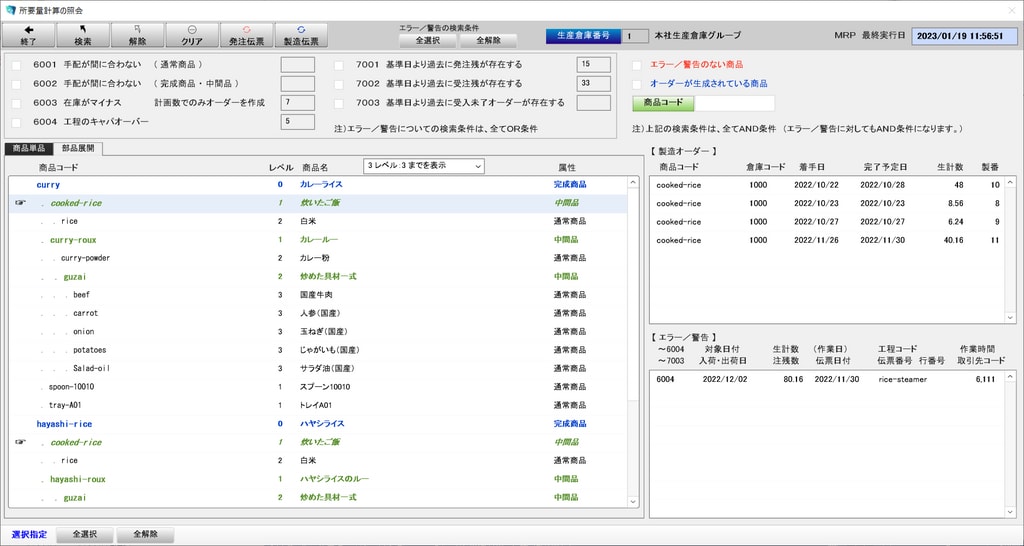
1)第1画面 MRP 検索および発注伝票/製造伝票の作成指示
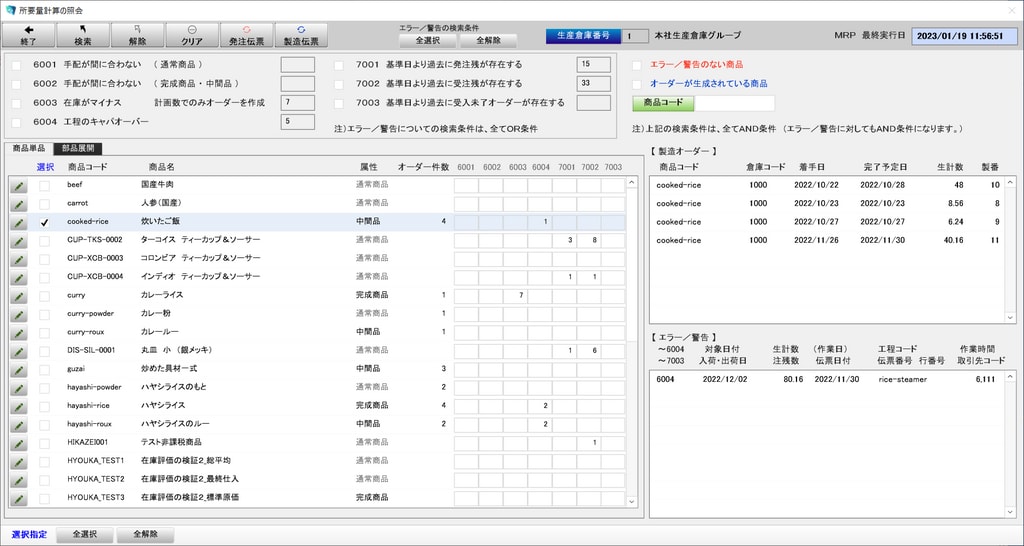
MRP(資材所要量計画)の実行結果を表示する照会画面です。
部品展開にて生成された品目およびそれ以外(商品単品)の品目が混在して表示されています。
・最初に、エラーまたは警告を確認し是正します。
特に工程のキャパオーバーに対しては以下の措置を検討し実施します。
①当該日の工程能力を増やす ※台数(人数)または稼働率
②当該日の作業時間を増やす ※残業
最終的な措置としては、
③生産計画数を変更する(無理な計画)
④顧客の希望納期を変更する ※受注生産の品目の場合
・次に、実際の発注伝票および製造伝票を作成します。
これらは、オーダー日付(発注日、製造着手日)を指定することにより、必要な期間(確定期間)までのオーダーを対象として作成することができます。
(以下の画面は、部品展開された品目のみを表示しています。
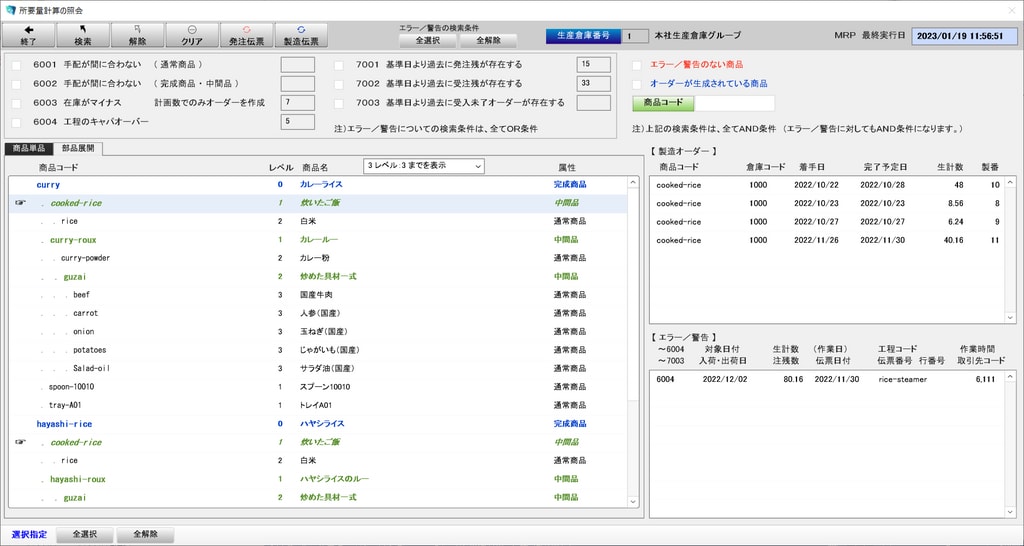
2)第2画面 MRP Entity

第1画面から確認したい品目を指定することで表示されます。

第1画面から確認したい品目を指定することで表示されます。
<説明>
1.生成される情報
1)発注・製造オーダー
・購買品は発注オーダーが生成されます。
・製作品は製造オーダーが生成されます。
・共通(完成製品以外)では、引計オーダー(親品目の生計に対する子品目の引落計画)も生成されます。
2)作業オーダー
・製作品のみ作業オーダーが生成されます。
2.MRP(資材所要量計画)には、製作品に対するCRP(能力所要量計画)が含まれます。
これにより、工程の負荷をチェックし、作業の着手を前倒しにしたりします。
発注・製造オーダーは、数量で手配計画を生成しますが、作業オーダーは作業時間で手配計画を生成します。
・製作品毎の工順マスタに登録される各工程は直列ルールとしています。
(直列ルール : 次工程は、前工程が完了しないと着手できない。)
3.CRP(能力所要量計画)
作業オーダーの生成は、バックワード方式で行っています。
・工順の後工程から処理を開始します。
・作業オーダーの割り付けは、終了時刻を基点として開始時刻を生成しています。
・対象の日付(バケット)において、当該工程の空き時間が不足する場合、前日以前の日付(バケット)に移動して再度チェックします。
・一般的な負荷山積みはせず、終了時刻・開始時刻にて、当該工程の当該バケットに対して占有させる方式を採用しています。
※一般的な負荷山積み
(工程の負荷をまず無条件に山積みし、その後に工程の負荷山崩しを最早開始日と最遅開始日の差異(余裕日数)にて移動させる方式)
一つの製作品の工順は複数の工程かつ直列ルールで成り立っていますので当該工程のみを移動させることは前後の工程に影響が出てしまいます。
・占有された作業オーダーからの空き時間帯を取得し、今回の作業オーダーが充当可能かのチェックを行っています。
・今回の作業オーダーの作業時間の全てが充当しきれない場合は、充当可能な時間のみ充当させ、前日以前のバケットに対して同様に空き時間を取得し残りの作業時間を充当します。
以上です。
1)発注・製造オーダー
・購買品は発注オーダーが生成されます。
・製作品は製造オーダーが生成されます。
・共通(完成製品以外)では、引計オーダー(親品目の生計に対する子品目の引落計画)も生成されます。
2)作業オーダー
・製作品のみ作業オーダーが生成されます。
2.MRP(資材所要量計画)には、製作品に対するCRP(能力所要量計画)が含まれます。
これにより、工程の負荷をチェックし、作業の着手を前倒しにしたりします。
発注・製造オーダーは、数量で手配計画を生成しますが、作業オーダーは作業時間で手配計画を生成します。
・製作品毎の工順マスタに登録される各工程は直列ルールとしています。
(直列ルール : 次工程は、前工程が完了しないと着手できない。)
3.CRP(能力所要量計画)
作業オーダーの生成は、バックワード方式で行っています。
・工順の後工程から処理を開始します。
・作業オーダーの割り付けは、終了時刻を基点として開始時刻を生成しています。
・対象の日付(バケット)において、当該工程の空き時間が不足する場合、前日以前の日付(バケット)に移動して再度チェックします。
・一般的な負荷山積みはせず、終了時刻・開始時刻にて、当該工程の当該バケットに対して占有させる方式を採用しています。
※一般的な負荷山積み
(工程の負荷をまず無条件に山積みし、その後に工程の負荷山崩しを最早開始日と最遅開始日の差異(余裕日数)にて移動させる方式)
一つの製作品の工順は複数の工程かつ直列ルールで成り立っていますので当該工程のみを移動させることは前後の工程に影響が出てしまいます。
・占有された作業オーダーからの空き時間帯を取得し、今回の作業オーダーが充当可能かのチェックを行っています。
・今回の作業オーダーの作業時間の全てが充当しきれない場合は、充当可能な時間のみ充当させ、前日以前のバケットに対して同様に空き時間を取得し残りの作業時間を充当します。
以上です。