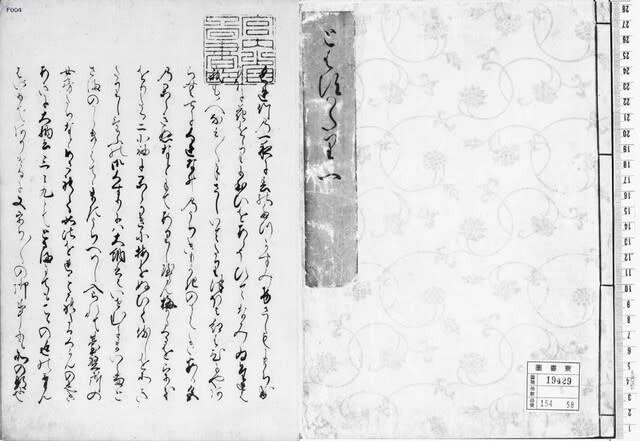
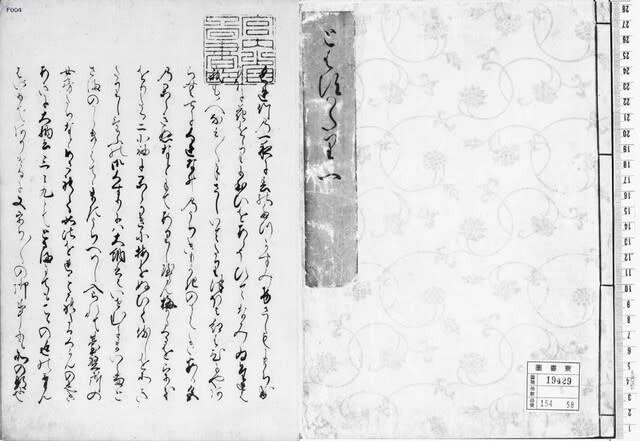
一部繰り返しになりますが、高品質な誘導電動機の回転子(以下ローター)をダイキャスト鋳造で製作しようとするなら、以下の記事を参考にしてください。
誘導電動機(籠型)ローターバーのアルミ化はすでに1940年以前から行われており、富士技報-昭和14年5月号(現在は富士電機技報)にアルミニウム製回転子製造の報告が有る。また昭和16年12月号(米国との開戦の時です)には手汲みによる鋳造の報告が有る。このときから電動機製造に関しては苦労していたと思われる。その後1947年ころから米国製ダイキャスト機を使ってDC化が進んだようだ(日立評論の2010年12月号) 上記3件の金型方案については詳しい情報がないためどのように鋳造されたか不明で、情報提供をいただけるとありがたいなと考えています。ダイキャスト化されてからは以下のような金型方案で長い間鋳造されてきました。
ローター鋳造の金型方案は、横型鋳造機では、以下のような方法が一般的に採用されてきました。第2次大戦後現在まで70年以上です。
これは、copper.org. が公表している金型方案です。(アルミではなく銅を使おうとしている)金型の中では以下のように置かれています。(注記あり'24.05.26付け)
これは、富士電機システムズ社が2008年に特許申請したものでやはりローターは水平に置かれています。画像クリックすると拡大されます。つまり最近でもこの方案が採用されているのです。現状に不満がないのかとやや驚きます。
これは東芝機械が2001年に出したものです。図では90度回転した状態で置かれていますが、横型鋳造機を使ったもので、これも金型内でローターコアは水平に置かれています。これもDCマシンの有力メーカーが特許申請しているということは、ここでもまだ、この方案が主流なんですね。
他にも各社が(私から見るとあまり望ましくない鋳造法を)、現在も選択しています。
これは縦型のように見えますが、横型です。
以上の通りで、根本原因を究明して不良品を減らそうとか考えないのかな。日本の有力メーカーは根本的な間違いに、未だに気が付かないのかしら?と思う。 有名企業の名誉の為に追記すると、外径の大きなローターや高品質を要求されるローターは縦形鋳造機(東芝機械や宇部興産機械で専用機を作っている)を使って製作されている。しかしコストが上がるため普及品は横型鋳造機が使われている。
この方法でローター生産を行っている企業はいまだに多いようです。富士電機、三菱電機、日立製作所などが特許から見ると今だに上記の方法で鋳造を行っており、その現場は苦労していると思います。また日経メカニカル1986.10.20号では、富士電機がバー切れ(スロット内でアルミが断線している状態)の検出をオンライン(工程内)で行っているという記事が有る。これ以上鋳造工程での品質改善が望めないから、製品を全数検査しようという力技と言えるものであった。他社からもバー切れに関する検査方法の特許が出ている。
以上が横型鋳造機を使って行われている普通の(大勢が採用している)鋳造方案です。戦後ほぼ70年間(更新していないから75年か)各社が基本的に同じ方案を採用し、新しい改善案(本稿の後半で説明します)は筆者の提案まで実用化されては出てこなかった。なお、アルミではなく銅製ローターの鋳造試作をしているメーカーの情報では、このローターを水平に保持する鋳造方案でも巣の問題はあまり気にならないとのこと。アルミのように巣によるアンバランスとか断線の問題は起きていないとのこと。溶湯としての銅の比重が大きいからだろうか、溶湯の粘性が違うのだろうか。しかしその後、アメリカのネット上に報告された誘導電動機の効率向上と称して回転子のバーを銅ダイキャストで解決しようとするグループ(AC Propulsion、+ Ramco + MIT + ICA----(MIT以外は知らないなが))がレポート(uploads/2013/09/CR-IM-hi-speed-improvement-project-ARMI-final-report-11Jul13.pdf)を公表しているがその報告の39ページにあるエンドリング部の巣は酷い(ほんとにヒドイ)画像で、
良くこんな品物を公表したなと思うレベルでした。それでも最高に良いものを選んで公表してると思われるので、写真を公表した最高レベルがあれだとすると量産は無理だろうな。’24.05.11 注記追記
また縦型鋳造機を使っては以下のような方案になります。
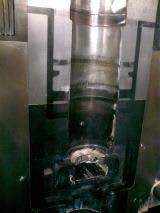
金型が傷んでどのように修理したらベストか、という相談があった。ハイシリコンのアルミを使っているため流速の早い部分がどうしても摩滅してしまう現象はご存じだろうか。修理法はさておいて、金型を詳しく観察したところ、流速の早いゲートだけでなく、流速が一定の部分においても金型の摩滅が発生している。なぜかと思って老眼でよく見るとスムーズ(smooth)な流れを意識していないため(流れがT字形になっていてT字の下から入りT字の右側へ抜けていく流れ。T字の右へ流れる部分で渦が発生して交差部から20~30mmほど摩滅あり。これはT字の左側部を作ってあるため流れが交差部まで来て右に行こうか左に行こうか迷った結果ここで渦が発生しているように見える、ちなみに窒化処理した入れ子で、C135ton )その部分に不要な渦が発生しているため、そこだけ金型が凹みとなっている。ADC12ではこの現象をはっきり確認することはあまりないが、ハイシリコンの場合ははっきり金型に症状が現れる。やはりランナー設計でも同じ、スムーズな流れを意識しないと金型の破損につながるんだなと再認識した次第です。
’24.05.11 T字部流れの説明が良くないため改定追記
作業中にプツンとパソコンの電源が落ちてしまった。あらら,パソコンの寿命か? 困ったなー。電源コードを抜いて、もう一度電源オンにしてもすぐにプツンと切れてしまう。中古品を使って3年目だし諦めるか。しかし昨日のデータのバックアップをしてないし、何とかするしかない。CPU内部で温度を測定していることが頭に浮かんできたので、ダメでもともとだからと、「CPUの熱が逃げない」という仮説を作って、ファンが回っていないか。回っている。ホコリで詰まったか。詰まっていない。ソケットから外したCPUの上面を良く見るとサーマルグリスが乾いて剝がれかかっている。これかなと半信半疑ながら、グリスを塗り替えて試してみるか。だめなら諦めよう、ということで急いでPC販売店に出かけ、ダイヤモンド入りとか銀入りとか各種ある中で熱伝導率の良いやつを選んでレジへ。これでだめなら諦めますからと祈るような気持ちで組み上げた。配線を済ませて電源オン、やったーしっかり立ち上がって電源が落ちることもない。作業後のビールのうまいこと。
基礎伝熱工学的一日でした。費用750円。
PF法での真空バルブ応用について
PF法(Pore-Free、日軽金が開発)は、金型内の空気・特にその中の80%の窒素を酸素に置換して金型内部に酸素だけを存在させて、鋳造品の品質向上を狙う鋳造法であるが、一般的なPF法では、酸素吹き込みの直前に金型を完全に閉じないでわずかに開いた状態で酸素の吹き込みが行われる。この時に酸素への置換が完全に行われればPF法は有効であるが、しばしば空気中の窒素が金型内に残留するため、巣の形で鋳造品に現れると考えられる。引け巣の問題は別です。
ここでDC金型に真空バルブを設置して大気開放で使用すると、金型内の窒素と酸素の置換が効率良く行われる、つまり大量の酸素を一方の入口から吹き込み真空バルブ(管路断面が確保されている)から窒素80%の空気を排出すれば、PF法としての本来の能力を十分に発揮することができると考えられる。この時、金型スリーブから真空バルブまでの管路の流れに、行き止まりや淀みができないように流れ(FLOW)に留意した金型設計がなされれば、PF法を有効 に応用することができると期待される。
もう少し詳しく書くと、真空バルブと言ってはいるが真空ポンプで吸引する必要はなく、大気に排出するだけなので、トラブルの少ない稼働が期待できる。実際に稼働したら軽く真空を掛けて吸引してみるも面白い。
注記: いい結果が得られたようです。'24.09.11