相変わらず、「インスタント・ステーション」の制作に苦戦中。
型を取り直しました。
前回は樹脂粘土にスジを付けて羽目板風にした天板でしたが、
今回は本物の短冊状にした木材を原型として型取りをしました。
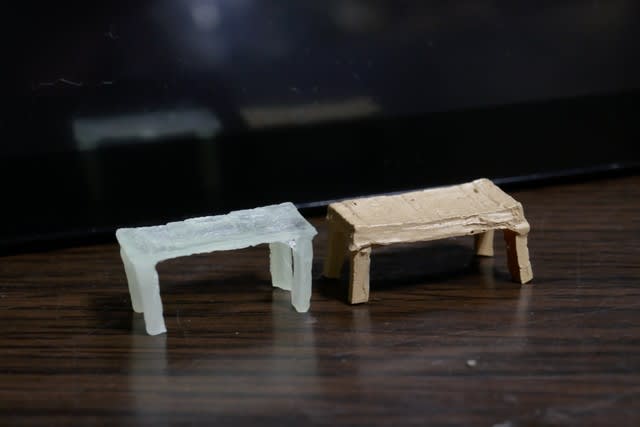
▲左が新規に起こした型から。右が以前のもの。
寸法の大筋は決まりましたが、いざ作成してみると想像以上に
板の厚みが目に付くようになりました。
というか、前回触れた「鉄道ピクトリアル」誌の写真を見るまで、
実物のホームがそこまで薄っぺらなものだとは想像していなかった
もので…。
上の写真の左側の作例は天板の厚みも薄くしてみましたが、
この厚さと強度の両立を図るための材質選びに苦慮しています。
当初は多くのガレージキットで用いられているレジンの使用を
考えましたが、この程度の小さなパーツに見合う量で2種類の液を
全く同量に加減するのは不可能に近く、結局多めに取って混和して
大量に余してしまう結果となりあまりに不経済と判明。
薄くても強度が確保できて良かったのですが。
型を複数用意して一度に多数作る試みもしましたが、やはり余す分
の方が多くなってしまいました。
また、手芸用品として売られているUVレジンも試しましたが、かなり
厚みを持たせないと容易にたわんでしまうので、やはり実用的では
ありませんでした。
手軽にできて細かいモールドも再現できて良かったのですが。
次に、同じUV硬化樹脂でも、車などの補修用の樹脂を試しました。
硬化前の状態でも粘度が高くモールドの再現には慎重を要しますが、
かなり薄くしても充分な硬さがあり、なんといってもかなり安価
なのが助かりました。
しかし非常にもろく、この薄さでは容易に折れてしまうので、
今のところ裏面の目立たない中央部分にUVレジンを垂らして補強を
する方法を試していますが、元々のもろさは如何ともし難いです。
最終的に行き着いたのは、熱で軟化し、冷めると硬化する樹脂です。
こちらもかなりの硬さを持ち、上記各素材より現実的な選択肢です。
天板の厚さは試作段階ではやや厚いですが、成型の手法を見直して
薄くすることはできそうなので、この線で行ってみようと思います。
下の作例はこの樹脂を用いたものです。
硬化後の加工性に劣り、カットやヤスリ掛けがしにくいのが欠点です。
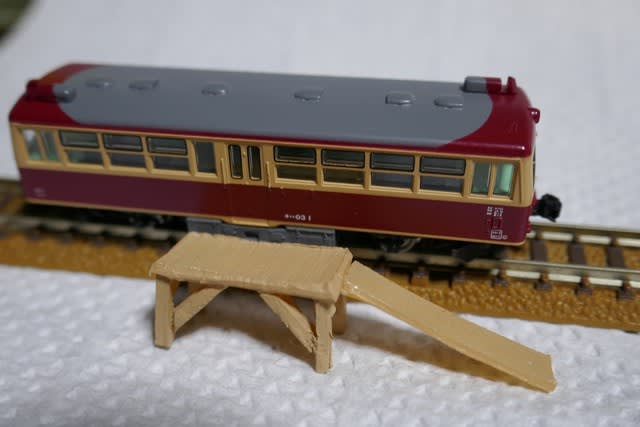
支柱は2ミリ角棒を使った前回のものより細くしたのですが、まだ
太く見えますね。
1ミリ角棒では強度の不安があるのですが、どうでしょうかね。
型を取り直しました。
前回は樹脂粘土にスジを付けて羽目板風にした天板でしたが、
今回は本物の短冊状にした木材を原型として型取りをしました。
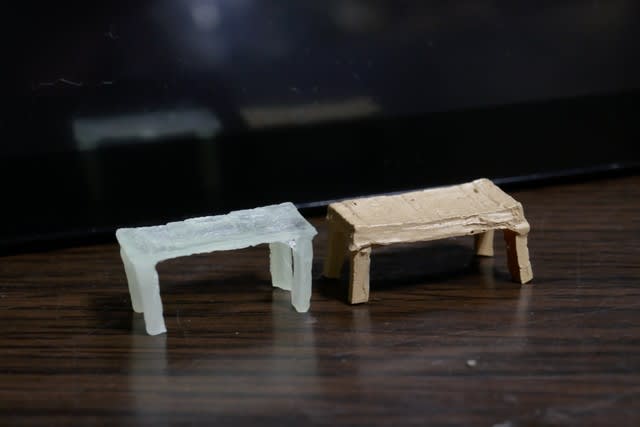
▲左が新規に起こした型から。右が以前のもの。
寸法の大筋は決まりましたが、いざ作成してみると想像以上に
板の厚みが目に付くようになりました。
というか、前回触れた「鉄道ピクトリアル」誌の写真を見るまで、
実物のホームがそこまで薄っぺらなものだとは想像していなかった
もので…。
上の写真の左側の作例は天板の厚みも薄くしてみましたが、
この厚さと強度の両立を図るための材質選びに苦慮しています。
当初は多くのガレージキットで用いられているレジンの使用を
考えましたが、この程度の小さなパーツに見合う量で2種類の液を
全く同量に加減するのは不可能に近く、結局多めに取って混和して
大量に余してしまう結果となりあまりに不経済と判明。
薄くても強度が確保できて良かったのですが。
型を複数用意して一度に多数作る試みもしましたが、やはり余す分
の方が多くなってしまいました。
また、手芸用品として売られているUVレジンも試しましたが、かなり
厚みを持たせないと容易にたわんでしまうので、やはり実用的では
ありませんでした。
手軽にできて細かいモールドも再現できて良かったのですが。
次に、同じUV硬化樹脂でも、車などの補修用の樹脂を試しました。
硬化前の状態でも粘度が高くモールドの再現には慎重を要しますが、
かなり薄くしても充分な硬さがあり、なんといってもかなり安価
なのが助かりました。
しかし非常にもろく、この薄さでは容易に折れてしまうので、
今のところ裏面の目立たない中央部分にUVレジンを垂らして補強を
する方法を試していますが、元々のもろさは如何ともし難いです。
最終的に行き着いたのは、熱で軟化し、冷めると硬化する樹脂です。
こちらもかなりの硬さを持ち、上記各素材より現実的な選択肢です。
天板の厚さは試作段階ではやや厚いですが、成型の手法を見直して
薄くすることはできそうなので、この線で行ってみようと思います。
下の作例はこの樹脂を用いたものです。
硬化後の加工性に劣り、カットやヤスリ掛けがしにくいのが欠点です。
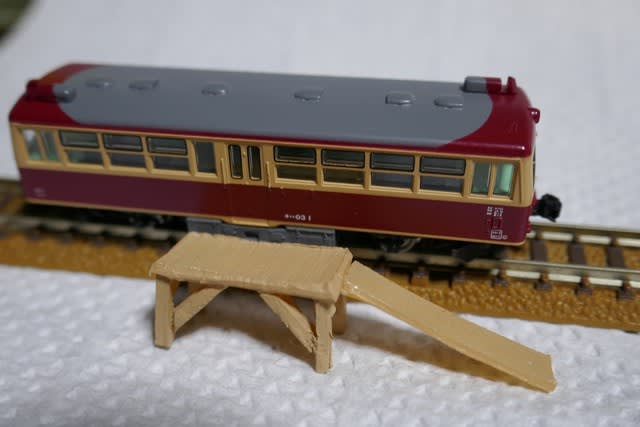
支柱は2ミリ角棒を使った前回のものより細くしたのですが、まだ
太く見えますね。
1ミリ角棒では強度の不安があるのですが、どうでしょうかね。