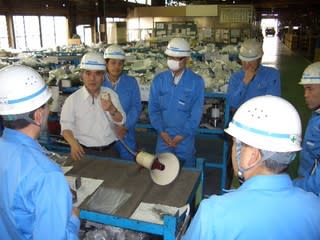
「改善コンサルタント」と聞いて何を連想しますか?
昨年、石原先生の早朝勉強会で講師に来て下さった改善コンサル
タントの柿内先生は私が持っていた「改善コンサルタント」の
イメージとは正反対のタイプでした。
高圧的でなく、ソフトで、褒め上手。

その時から、一度ぜひ我が社に来て欲しいとお願いしていた
のですが、博士論文や全国各地の工場からの改善依頼への
対応で、大忙しで、なかなか実現しませんでしたが、やっと
来て頂くことができました。
我が社の80周年記念のスコラ・柴田さんの講演に端を発し、
定時後オフサイト・ミーティング→リノベーション→社楽と
発展してきた、風土改革運動からスタートした、リードタイム
短縮活動が、この4月に「組立工程管理セクション」として
とうとう正式な部署として発足しました。
このまったくの独学で進めてきた活動の妥当性を、プロの目で
検証してもらうことが、今回柿内先生にお願いしたかったこと
なんです。
その活動の内容とは、
『部品を探す・集める時間をゼロに近づけ、”組む時に部品が
ある”状態を作り、組立工数を短縮する』
というもので、その手段として、パート図を作成して、それに
基づいて組立を行ってきています。

これに対して柿内先生から、
「完全受注生産なんだから、トヨタ生産方式をそのまま取り
入れるには無理がある。むしろパート図を作って、この
リードタイムで作れというやり方は、部署ごとの部分最適
ではなく、全社最適に向かわざるをえないので、理に適った
活動だね。
また日本の現場でパート図もどきと言えども、たくさんの
現場を見てきた私でも初めてですよ。驚きました。
まだまだピリッとしていないところがたくさんあるが、
独自でここまでやったというのは、たいしたもんですよ。」
と激励とお褒めの言葉、両面頂きました。
これに自信を深めましたので、明日からはより精力的に活動を
行っていきましょう。
柿内先生、本当に貴重なアドバイスありがとうございました。
必ず成果を出しますので、またその様子を見に来て下さい。
ありがとうございました。
ホント残念だったね。
とても刺激的でしたよ。
今後やるべきことが明確になり、とても価値ある
一日でした。
ますます頑張って下さい。
明日の商談もよろしくね。
今度、ご教示下さい。
自分達が当たり前だと気にも留めないことをライブで指摘されるからこそ「本の聞きかじり」では理解できないことが理解できたり自分達の凝り固まった概念が吹っ飛んでしまうんでしょうね!?
それと「スピード」の足りなさは正直、痛感しました。
「おーい!みんな!俺が遅いことよーく判った!」
「もっと!スピードあげようぜ!」
それから先生の話の中で気がつきましたか?今日始めて来た会社、会った俺たちに先生は俺たちと同じように当社を「ISOWAさん」と言うのではなく俺たちと同じように「うちの会社」と呼んでいましたね!?
仲間だということ!一緒にやろう!ということを先生の方から言ってくださっているんだよネ!「さすがプロ」管理者である俺たちはそんな気持ちをスタッフに示しているんだろうか・・・?「反省・反省」
「改善」はスタッフに強要するのではなく管理者が率先垂範しなきゃ!
それと先生と雑談していた時、俺が「うちは全てにおいてPDCAのD・Aは得意なんですけど
P・Cが・・・?」「だから最近はその順番をDCAPでもいいよと言っているんです。」と言ったら「いや、CAPDでいいんですよ!」と、仰っていました。
みんな理解できますか?管理サイクルは何もPから廻し始めなくてもいいんです!
Dが得意だったらDから、Cが得意だったらCからはじめて次のステップ⇒ステップへとサイクルすればいいんです。
先ず、得意なステップから踏み出し!(例えば俺はエイヤーと実行することが得意だったら先ず実行して⇒チェックするとか?俺は調べるの得意だから先ず調べる⇒その結果に再行動とかサ!?)課題解決・日常業務に「管理サイクルを廻して考すことはじめようぜ!」
長くなって「ゴメンナサイ!」「これで終わります!」
数あるアドバイスの中から「5Sの看板を見て」のタイトルで
社内へメール送信しました。以下一部紹介させていただきます。
先生の発言と差異が生じていればご堪忍下さい。
管理・監督者各位
改善コンサルタント柿内幸夫様がISOWAへやってきた。
5Sの看板をみて
どこもかしこも看板だおれで実績に乏しい と指摘。
ご指摘道理である。
改善活動の現状は一部の限られたものの発案(アイデア)ですすんでいる。
だから言われても仕方がない。
改善活動を、
とりあえずやろや の シンボルが「5Sの看板」。
工場内のあちこちの看板、ポスター、作業標準、注意警告板などで型はできた。
今、型に身を入れる段階へきた。
型に身を入れよう。これからが勝負。
改善の基本は5S(ムリ・ムダ・ロスとり)これも間違いない。
・・・・・・・・・
・・・
・・
(註、”5S活動推進の列車に乗り遅れないよう”)
渡辺
柿内先生次回のアドバイお待ちしています。
ありがとうございました。後は実践あるのみ。
やってダメなら元に戻せばいいんですから・・・
と背中を押していただいたので、やっぱり実践あるのみ。
「見える化」をPDCAサイクルで実践します
ブログへのコメントまで頂き、ありがとうございます。こういう前向きな社員が我が社の一番の財産であり、風土改革の賜物だと思っています。
みんなで、リードタイムにこだわり、徹底的に追求していきます。また様子を見に来て下さい。
その時は昨日より必ず進歩した姿をお見せします。
ありがとうございました。
ない」ということで今、
リノベーションで半年ほど議論を重ねて活動の
ターゲットを「(トータル)リードタイム短縮」
にして、第1ステップの仮設
「部品が必要なときに必要な場所にあれば、
組立工数が減る」
をやってみることになったころを思い出しました。
最終的には「リードタイム短縮」なんですが、
これに行き着くまでロジックツリーを何度も作っ
たり、色々な部署のキーパーソンに話を伺ったり、
リノベーションメンバー全員がある程度腹に落ちる
まで本当に半年ぐらい議論したんです。
でも、このおかげで方向性を外すことなくこれまで
やってこれたので、これからは自信をもって、もっとPDCAのスピードを上げて活動していきたいと思います。