先週のブログで 『日本の製造業 品質管理 / 物を見る力の養成が急務』との私見を書いたが、さっそくこのブログを見ている人からメールを頂いた。
最後に書いた『『なぜなぜ』問答が真剣に出来る人間力を引き戻さない限り、日本の製造業は強くなれないかと考える。』という事について、
『そだね~』と言ってくれる仲間がいたが、『リタイアした者ではどうしようもないな!!』との感想が多かった。
小生も定年後何かできないかと、安全管理や品質管理でのお手伝いを売り込んでみたが、定年前での準備ができていなかった事もあり、そんなに簡単にはいかない事を感じていたので、まさしく遠吠えの感である。
このブログを見た次の世代の方々が、何かを掴んでもらえればと発信を続けたい・・とコメントメールを返信した。
頂いたコメントや事例はおいおい咀嚼し紹介していきたいが、一つ、若い方からのメールの言葉が胸に響いた。
これは、定年の何年か前に、ある鉄工場を経営する友人に頼まれ、『大阪弁で考える品質。安全とは』というテーマで工場の方へ話をさせてもらった事があるが、この時に参加の若いメンバーからである。
メールは『コン先生、現役を離れてもまだマス目用紙持っておられるのですね』・・との携帯メール挨拶であった。
この前のブログに『ポンチ絵』を描いた紙の事のようである。
この勉強会では、鉄工場の技術を、小生より少し年上のベテランが、若い方へどう技術を伝承させたらいいかが判らないとの事で
引き継ぐ方法を聞きたいとの事であった。
このため、鉄工場は門外ではあるが、いろいろな仕事での出来事を、大阪弁で『おもしろおかしく』説明する事で雑談をさせて頂いた。
例えば、旋盤で素材を削りだす時、ベテランの方が『もうちょっと、ここをこないせなあかんで』と説明しても、若い方は『なんやようわからんわ』と折り返される事がある。
このシーンでは、
もうちょっと ⇒ あと何ミリとか定量的に
ここを ⇒ 具体的な場所
こないに ⇒ 方法の具体化
と指導をするベテランの方へは具体策の説明の必要性をやんわりとポイントを説明した。
さらに、指導を受ける方へも、この逆で、具体的にどうする必要があるのかを聞き出すように努力することの重要性を説明し、理解してもらった。
この時に若い方へメモるためのマス目入りの名刺大のカードを提供したが、これが後に役立ったようである。
『そや』『それちゃうで』『あかんがな』『ちゃっちゃとやらんか』『あほか』『何べんゆうても判らんやっちゃ』から『ようやった』『そやそや』・・こんな積極的な会話の中で成長を期待したが、メールでは、勉強会の後、ベテランの方の教え方も段々うまくなったとのこと。
溶接でも、昔は『ここあぶってみ』とだけ指示が出されていたのが、『このチョークの範囲を、バーナーを半分ほど開けて、ゆっくりと縦横へ動かしてあぶり、赤こうなる所がムラないようにせなあかんで』と、コツや勘所の指導がしてもらえるようになったとの事。
さらには仕事が終わったあと、切端をあぶって、急に水をかけ、あぶり方でこんなにひずみが違うんや・・とも手本を見せてもらえた。これらは、若い方得意のスマホで画像として記録され、学ぶネタができたとも聞いており、少しはお役にたてたのではと思っている。
この若手の方が今回の新幹線の台車の事故のコメントを書いてくれていたが、『あんな、厚い、大きな溶接は難しいで。』『船を作るくらいの技術が無いとあかんわ』との技術面から、『でけんならでけんとちゃんと言わんとあかん』『おっさん(班長)はどないやねん』との究極の言葉が最後にあり、やはりベテランが、まずは図面通りの作業が出来る事の確認を行い、指示する事がポイントのような気がする。
この作業確認が出来ないままで、単にバリを削り出せだけでは、作業する方へ勘所、原理原則が伝えられず、『なぜなぜ』や
『ここが課題・問題』という意見も出てこなくなるのではなかろうか。
品質維持のためには、作業をする方々の感性を引き上げる事が最も重要であり、先のブログでの『なぜなぜ』問答が真剣に出来る人間力をどう生み出していくかが喫緊の課題としたが、川重での説明では量産化段階で問題発生が起こり、設計へのフィードバックが出来ていなかった事が課題とのコメントであったが、現場からの問題を、問題として捉えられない設計部門や品質管理部門の技術力低下が最も危ないかもしれない。
このために、設計部門や品質担当部門はもっと現場へでて会話をしないと、何も見えてこない可能性がある。
大阪弁ではファジーな所を、阿吽の呼吸で双方が解決できるが、今回の台車事故ではこんな会話も出てきていないのかもしれない。
会話力が『なぜなぜ』問答を真剣に議論するための一つの解決策であり、この切り口は『ポンチ絵』など、コンピューター酷使の世界ではない、アナログ、手書きの世界を構築する事も重要なのかもしれない。
話はあっちこっちに飛んでしまうが、今回頂いたメールの中でも、小生が会社生活時代、最終製品を量産化する段階で、安全監査では、WORD、EXCELできれいに書いた団子図や設備フロー図ではなく、出来れば手書でもかまわないから、具体的な機器の大きさで、一目できるようにした方が良いのでは提案していた事を懐かしむ内容を頂き、まさしく今それが必要との事が書かれており、感性の低下が心配との事であった。
メールの中で、反応でタンクから釜へ原料を移送する場合、建屋の上階に原料タンクがあり、自動閉止弁で流入量をコントロールする様な設備となっていた場合、この弁が故障し制御が利かなくなった場合、最悪釜からあふれてしまう事になる。
これが、最近の安全監査用資料で、タンクの大きさや設置位置が配管図フローだけで示されている事が多く、上記のような危険をはらんでいるにも係わらず、危険個所が一目で判らず、誰も指摘されないままで、安全監査会議が通過し、生産に入り初めて問題が発覚したこともあったとの事。会議で簡単な『ポンチ絵』図面があり、現場主義で認識確認ができなかった事を反省したとのコメントであった。
この現場を熟知し、簡単なスケッチ図を的確にかけるかが、安全対応、品質管理では必須であり、合理化のネタにもなってくる。
昨今このような現場力の低下が気になり、どう向上させていくかの解決策を見つけ出さないと、最悪の事態を引き起こす可能性も否めないとの内容であったが、たしかに最近の若い方々は、『黒板メモ』も出来なくなっているような気もする。
文書作成があまりにもコンピューターに頼り過ぎた事の弊害なのかもしれない。
『ヒヤリメモ』や『1ポイント改善メモ』でもっと手書きしないと、ダメなのかもしれない。
次回以下、もう少しまとめていきたい。
<鉄工場での勉強会でのまとめを幹部用にPP化>
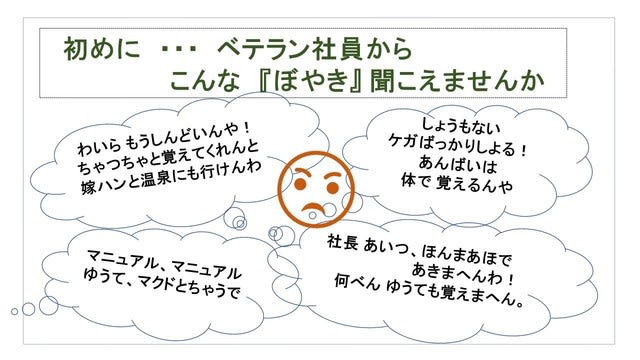







・・続く
最後に書いた『『なぜなぜ』問答が真剣に出来る人間力を引き戻さない限り、日本の製造業は強くなれないかと考える。』という事について、
『そだね~』と言ってくれる仲間がいたが、『リタイアした者ではどうしようもないな!!』との感想が多かった。
小生も定年後何かできないかと、安全管理や品質管理でのお手伝いを売り込んでみたが、定年前での準備ができていなかった事もあり、そんなに簡単にはいかない事を感じていたので、まさしく遠吠えの感である。
このブログを見た次の世代の方々が、何かを掴んでもらえればと発信を続けたい・・とコメントメールを返信した。
頂いたコメントや事例はおいおい咀嚼し紹介していきたいが、一つ、若い方からのメールの言葉が胸に響いた。
これは、定年の何年か前に、ある鉄工場を経営する友人に頼まれ、『大阪弁で考える品質。安全とは』というテーマで工場の方へ話をさせてもらった事があるが、この時に参加の若いメンバーからである。
メールは『コン先生、現役を離れてもまだマス目用紙持っておられるのですね』・・との携帯メール挨拶であった。
この前のブログに『ポンチ絵』を描いた紙の事のようである。
この勉強会では、鉄工場の技術を、小生より少し年上のベテランが、若い方へどう技術を伝承させたらいいかが判らないとの事で
引き継ぐ方法を聞きたいとの事であった。
このため、鉄工場は門外ではあるが、いろいろな仕事での出来事を、大阪弁で『おもしろおかしく』説明する事で雑談をさせて頂いた。
例えば、旋盤で素材を削りだす時、ベテランの方が『もうちょっと、ここをこないせなあかんで』と説明しても、若い方は『なんやようわからんわ』と折り返される事がある。
このシーンでは、
もうちょっと ⇒ あと何ミリとか定量的に
ここを ⇒ 具体的な場所
こないに ⇒ 方法の具体化
と指導をするベテランの方へは具体策の説明の必要性をやんわりとポイントを説明した。
さらに、指導を受ける方へも、この逆で、具体的にどうする必要があるのかを聞き出すように努力することの重要性を説明し、理解してもらった。
この時に若い方へメモるためのマス目入りの名刺大のカードを提供したが、これが後に役立ったようである。
『そや』『それちゃうで』『あかんがな』『ちゃっちゃとやらんか』『あほか』『何べんゆうても判らんやっちゃ』から『ようやった』『そやそや』・・こんな積極的な会話の中で成長を期待したが、メールでは、勉強会の後、ベテランの方の教え方も段々うまくなったとのこと。
溶接でも、昔は『ここあぶってみ』とだけ指示が出されていたのが、『このチョークの範囲を、バーナーを半分ほど開けて、ゆっくりと縦横へ動かしてあぶり、赤こうなる所がムラないようにせなあかんで』と、コツや勘所の指導がしてもらえるようになったとの事。
さらには仕事が終わったあと、切端をあぶって、急に水をかけ、あぶり方でこんなにひずみが違うんや・・とも手本を見せてもらえた。これらは、若い方得意のスマホで画像として記録され、学ぶネタができたとも聞いており、少しはお役にたてたのではと思っている。
この若手の方が今回の新幹線の台車の事故のコメントを書いてくれていたが、『あんな、厚い、大きな溶接は難しいで。』『船を作るくらいの技術が無いとあかんわ』との技術面から、『でけんならでけんとちゃんと言わんとあかん』『おっさん(班長)はどないやねん』との究極の言葉が最後にあり、やはりベテランが、まずは図面通りの作業が出来る事の確認を行い、指示する事がポイントのような気がする。
この作業確認が出来ないままで、単にバリを削り出せだけでは、作業する方へ勘所、原理原則が伝えられず、『なぜなぜ』や
『ここが課題・問題』という意見も出てこなくなるのではなかろうか。
品質維持のためには、作業をする方々の感性を引き上げる事が最も重要であり、先のブログでの『なぜなぜ』問答が真剣に出来る人間力をどう生み出していくかが喫緊の課題としたが、川重での説明では量産化段階で問題発生が起こり、設計へのフィードバックが出来ていなかった事が課題とのコメントであったが、現場からの問題を、問題として捉えられない設計部門や品質管理部門の技術力低下が最も危ないかもしれない。
このために、設計部門や品質担当部門はもっと現場へでて会話をしないと、何も見えてこない可能性がある。
大阪弁ではファジーな所を、阿吽の呼吸で双方が解決できるが、今回の台車事故ではこんな会話も出てきていないのかもしれない。
会話力が『なぜなぜ』問答を真剣に議論するための一つの解決策であり、この切り口は『ポンチ絵』など、コンピューター酷使の世界ではない、アナログ、手書きの世界を構築する事も重要なのかもしれない。
話はあっちこっちに飛んでしまうが、今回頂いたメールの中でも、小生が会社生活時代、最終製品を量産化する段階で、安全監査では、WORD、EXCELできれいに書いた団子図や設備フロー図ではなく、出来れば手書でもかまわないから、具体的な機器の大きさで、一目できるようにした方が良いのでは提案していた事を懐かしむ内容を頂き、まさしく今それが必要との事が書かれており、感性の低下が心配との事であった。
メールの中で、反応でタンクから釜へ原料を移送する場合、建屋の上階に原料タンクがあり、自動閉止弁で流入量をコントロールする様な設備となっていた場合、この弁が故障し制御が利かなくなった場合、最悪釜からあふれてしまう事になる。
これが、最近の安全監査用資料で、タンクの大きさや設置位置が配管図フローだけで示されている事が多く、上記のような危険をはらんでいるにも係わらず、危険個所が一目で判らず、誰も指摘されないままで、安全監査会議が通過し、生産に入り初めて問題が発覚したこともあったとの事。会議で簡単な『ポンチ絵』図面があり、現場主義で認識確認ができなかった事を反省したとのコメントであった。
この現場を熟知し、簡単なスケッチ図を的確にかけるかが、安全対応、品質管理では必須であり、合理化のネタにもなってくる。
昨今このような現場力の低下が気になり、どう向上させていくかの解決策を見つけ出さないと、最悪の事態を引き起こす可能性も否めないとの内容であったが、たしかに最近の若い方々は、『黒板メモ』も出来なくなっているような気もする。
文書作成があまりにもコンピューターに頼り過ぎた事の弊害なのかもしれない。
『ヒヤリメモ』や『1ポイント改善メモ』でもっと手書きしないと、ダメなのかもしれない。
次回以下、もう少しまとめていきたい。
<鉄工場での勉強会でのまとめを幹部用にPP化>
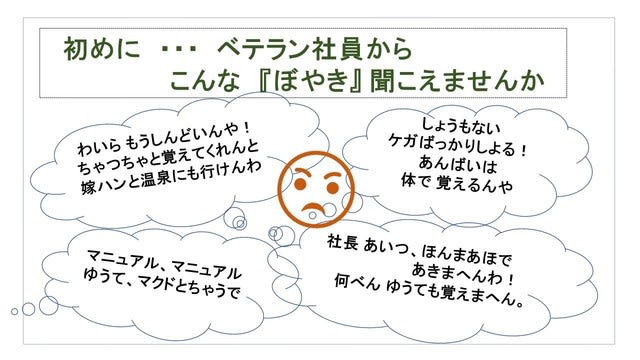







・・続く