スピーカー製作には欠かせない穴あけ。
















ホームセンターに行けば、直線カットは無料でやっているところもあり、サブロク合板900×1800mmを車に詰める大きさにカットしてもらって、自宅に帰って自分で丸鋸やジグソー、手引き鋸などを使って加工。
スピーカー製作には欠かせない円の穴あけは、色々な工具を使う方法がある。
学校の授業などで使った糸鋸、ジグソーが一番手軽だが変形した形になりやすい。
他には、トリマーをサークルガイドを使った穴あけがあるが、騒音問題で場所を選ぶ。
なので、一番手軽でしかも綺麗に穴あけ可能なのは自在錐を使った穴あけ方法を、私独自のやり方を説明します。
今回使用する工具は
充電式電気ドリル
Amazonで3500円くらいの安物

標準のスターエム製自在錐
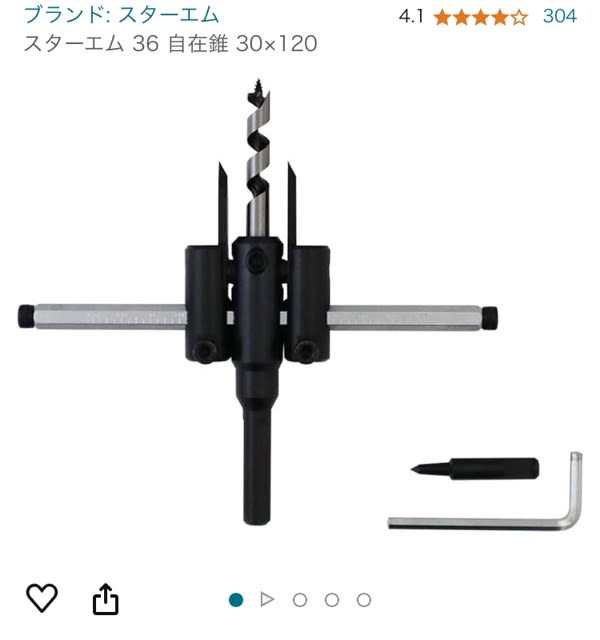
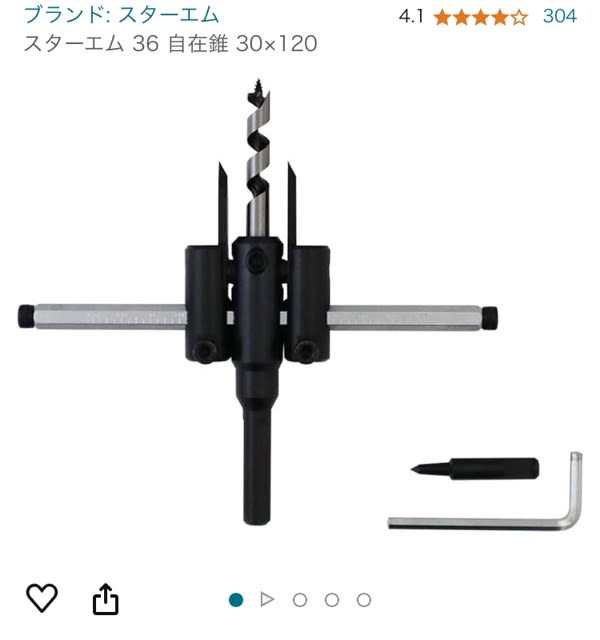
直径300mmまで開けられるロングバー

今回開けるのは、スピーカーユニットのザグリを加工するためのテンプレートのための穴あけ。
Φ232mmに対して0.5mm大きくしたΦ233mmの穴あけ。

コンパスを使って円を描く。
半径116.5mm。

自在錐を300のロングバーに取り替え。
(取り替え方法は商品の説明書を参照)
円の中心にセンタードリルを突き刺し、手で回しながら、外周を回る刃が当たるまで回し込む。
定規を使って、正確な寸法116.5mmの場所に外刃を合わせる。

合わせたら緩まない程度で、締める。

軽く締めたあと、上から押して刃型を付ける

180度回して対角線上にも、同様に刃型を付ける!

刃型を付けた長さを計ると、開けたい233mmに対して3mm大きい。

別の場所で同じことを繰り返す。
この時は内刃はフリーの状態

233mmに合わせることが出来ました。
233mmになるまで、何度も繰り返して調整。
233mmに合わせたら、固く締める。

円の内側に刃がある方、内刃を233mmで刃型を付けた場所に差し掛かる場所に合わせて固く締める。
この場合、同じ場所でなくても問題ない。

たまに作るスピーカー作りのために、作業台は必要ないので、コンクリートブロックなどの上に乗せ、動かないように足を載せて固定。

作業台を使うと、横から見る感じになり、軸がブレても修正しずらい。
さらに、回転する刃が手元に近いため、とても危険です。
半分くらい傷をつけたら、裏返し。

今回は12mm厚のコンパネを使用したため、裏返して穴あけが出来ました。
上から力を加えると、キックバックを起こしやすいため、ドリルの重さだけで板をスライドさせる気持ちで作業した方が、安全で綺麗に穴あけができます。

AC100v電源の電動ドリルの場合は、キックバックが起きた時は、回転は止まらず手から離れてとても危険です。
AC100v電源ドリルはスイッチを切らない限り回り続けるため危険ですので日曜大工には不向きかと思います。
しかし、充電式電気ドリルの場合、回転能力はAC電源ドリルに比べたら回転性能は落ちますが、安全にゆっくり開けられます。また、キックバックを起こした場合には、安全装置で回転は止まります。
マキタやリョービ製は高価などため、この安い3流メーカーだと更に回転性能が落ちるため、より安全に作業ができます。

一連の流れでの作業時間は、凡そ5分程度で、無事Φ233mmの穴あけが出来ました。
トリマーを使うとキレイに穴あけができると言う方も居ると思いますが、騒音問題で場所を選びます。
さらに、0.5mmまでの正確な調整が難しい。
穴あけを始めないと寸法が計りにくい。
ち具が高価。
時間がかかるなどの短所の方が多い。
是非、自在錐を使って、穴あけをやってみてください。
ドリルは横から見るよりも、真上から見た方が安全です。