最近はトレーラーのABS修理が立て続けに入庫…
ディーラーさんや同業他社さんからABSの修理依頼が急増してます。
去年まではABSチェックランプが点灯していても車検の継続検査には特に問題無かったんですが、今年から検査基準が変わりエンジンやABS、SRSなどのチェックランプが点灯している場合、修理しないと車検に受からなくなりました。
球が抜かれたりシステムが殺されていないかの点灯後の消灯確認もあるのでインチキは基本的には出来ません。
まあウチは検査基準が変わる前からお客様には安全上の理由から修理しないと車検は通せませんよ…という方針だったので特に苦労する事も無かったんですが、他の業者さん達はABSチェックランプが点灯していても見て見ぬ振りをする事が多かったようで…
ここにきてトレーラーのABSトラブルに苦労しているようです…(^_^;)
車両は東邦車両のコンテナトレーラー。
ABSシステムはBOSCH(クノール)のミニカッパーというタイプ。
このミニカッパーのトラブルは
以前書いた記事にもある通り接触不良が大半を占めていたんです…
ところが最近になって今までの接触不良にも繋がる新たな原因が判明したんです…
今回の車両も自己診断をかけると2-8左PCV系統異常のコードが出てたので…
また端子部の接触不良だろうな…なんて思いながらPCVハーネスのオスメス端子共にカシメて磨いて故障コード消去して再接続。
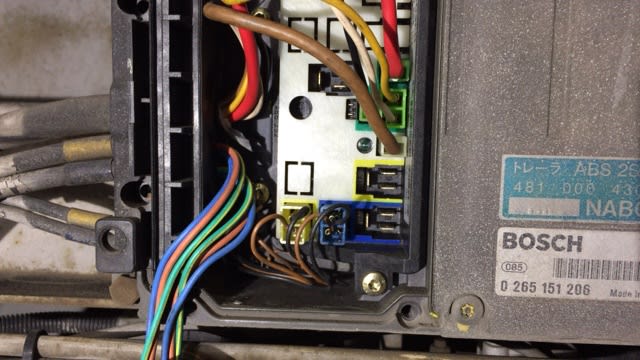
これで消えるでしょう…と思い試運転すると少し走ると再度点灯…
おっと…マジか。
その後何度磨いて接続し直してもちょっとでも振動を与えると再度点灯…
どうやらコンピュータ側に原因がありそうです。
これは参った…
実は過去にもこのコンピュータ不良を何度か経験してたんですが、深く原因を探究せず中古コンピュータへの載せ換えで対応してました。
新品のコンピュータは約40万もするので換えちゃってイイよ〜‼︎なんてお客様はほぼ居ませんから…
なのでウチではコンピュータ不良の場合廃車になったトレーラーから取り外しておいた中古コンピュータのストックで対応してました…
が、6個ほどあったストック品もとうとう残り1個と枯渇状態…
おまけにこのミニカッパーは古いタイプなのでたとえ新品でもいつまで供給されるかも不透明。
このままいくとマズイな…という事で、なんとか修理出来ないか原因を詳しく調べてみる事に。
現車からコンピュータASSYを取り外し…
コンピュータ単体にして分解。
いじり止めトルクスを取り外し…
カラーペイントもしてあるし、基本的にいじり止めトルクスが使われているという事は分解禁止を意味します。
分解した時点でメーカー保証の対象外となりますが、そんなものはとうの昔に切れてるので気にしません…笑
シリコンとボルトで固定された基板を上手く取り外し…
問題のPCV端子から繋がる基板回路を目視で確認するも特に目立った損傷は無し。
別回路で1箇所ダイオードが黒く焼けてる所がありましたが…
サーキットテスターで点検するとダイオードとしての機能は生きてたのでとりあえず問題無いでしょう。
PCV回路の導通を重点的に点検…
基板側には回路の遮断は無かったんですが、端子側と基板側を繋ぐスルーホールのはんだ部で導通をテストすると見事にオーバーレンジ。
端子の足に直接プローブを当てると導通。
という事はこれはもしかして…⁉︎
端子を繋ぐスルーホールのはんだ部をルーペでよく見てみると…
画像だと見にくいと思いますが…
端子の足とはんだが盛ってある部分にクラックが…
なるほど…
これで原因が判明。
端子を繋ぐスルーホール部の基板側のはんだにクラックが入った事による接触不良と判明しました。
正直、私はまだまだ老眼ではありませんが肉眼で見るのに苦労する程小さいクラックでした…笑
早速、はんだを盛り直してテストしてみる事に…
ルーペを介しながらのコテ作業。
周りのマイクロチップに過度な熱を与えないよう気を遣いながらなんとか盛りつけ…
今回クラックが入っていたのは左PCV回路の接続部だけでしたが、予防も含めて左右の接続部合計12カ所を盛り直し…
再度サーキットテスターで導通点検。
無事に導通しました…
基板クリーナーで表面の誇りや汚れをキレイにしてから再度組み付け。
車両に取り付けて…
全ての配線を接続して故障コードの消去。
自己診断動画
無事に2-1(システム正常)のコードを表示…
試運転の結果、チェックランプも点灯しなくなり修理完了です。
実はこれ以降、同じ症状のトレーラーが3台立て続けに入って来ており…
同じミニカッパーを搭載している車両で全てコンテナトレーラーだったんです…
で、何故こんなに同じコンテナトレーラーに頻発するのか考えたんですが…
コンテナ積み込み時の衝撃ではんだにクラックが入ったのか?とも考えたんですが今までクラックが入ったケース全車がPCVの端子部だけなんですよね…
衝撃によるクラックならPCVだけじゃなく他の箇所にも入るでしょうから…
なのでもともとPCV端子部のはんだ量が少なく強度が足らなかった可能性もあり、その上でコンテナ積み込み時の衝撃によってクラックが入ったんじゃないかと…
コンテナの積み込みってかなりの衝撃がありますからねぇ…
防振しておかないと衝撃でマーカーレンズとかも割れちゃうくらい…
それに別タイプのコンピュータにはあまり見ない症状ですから…
どちらにせよこの症状に対しては修理方法が確立出来たので今後の高額修理は避けられそうでひとまず安心。
ちなみに今まで交換したコンピュータは捨てずにとってあり、同じ原因の可能性もあるので時間がある時に1度調べてみる事にします…