今回はノーテレ・・・あまり聞きなれないですがドイツのメーカーのようです。ホイールの裏にメイドインジャーマニとありました。このホイールの3Dポリッシュの依頼があり工程を進めております。このホイールの特徴はディッシュタイプ(ディッシュとは平面形状を意味します)のため鋳肌を削る際に凸凹になりやすい、さらに窓がが小さく工具が入りにくく厄介なことに窓奥は平面があります。
全体の工程は
1)粗削り#240~中削り#320~仕上げ削り#400~#600
2)荒バレル研磨
3)乾式バレル研磨
4)自動バフ研磨
5)光沢バレル研磨
6)湿式バフ研磨
7)検査
この工程の時間配分は削り部分が約7割占めています。機械化されてもいまだマンパワーに頼っているのが現状です。
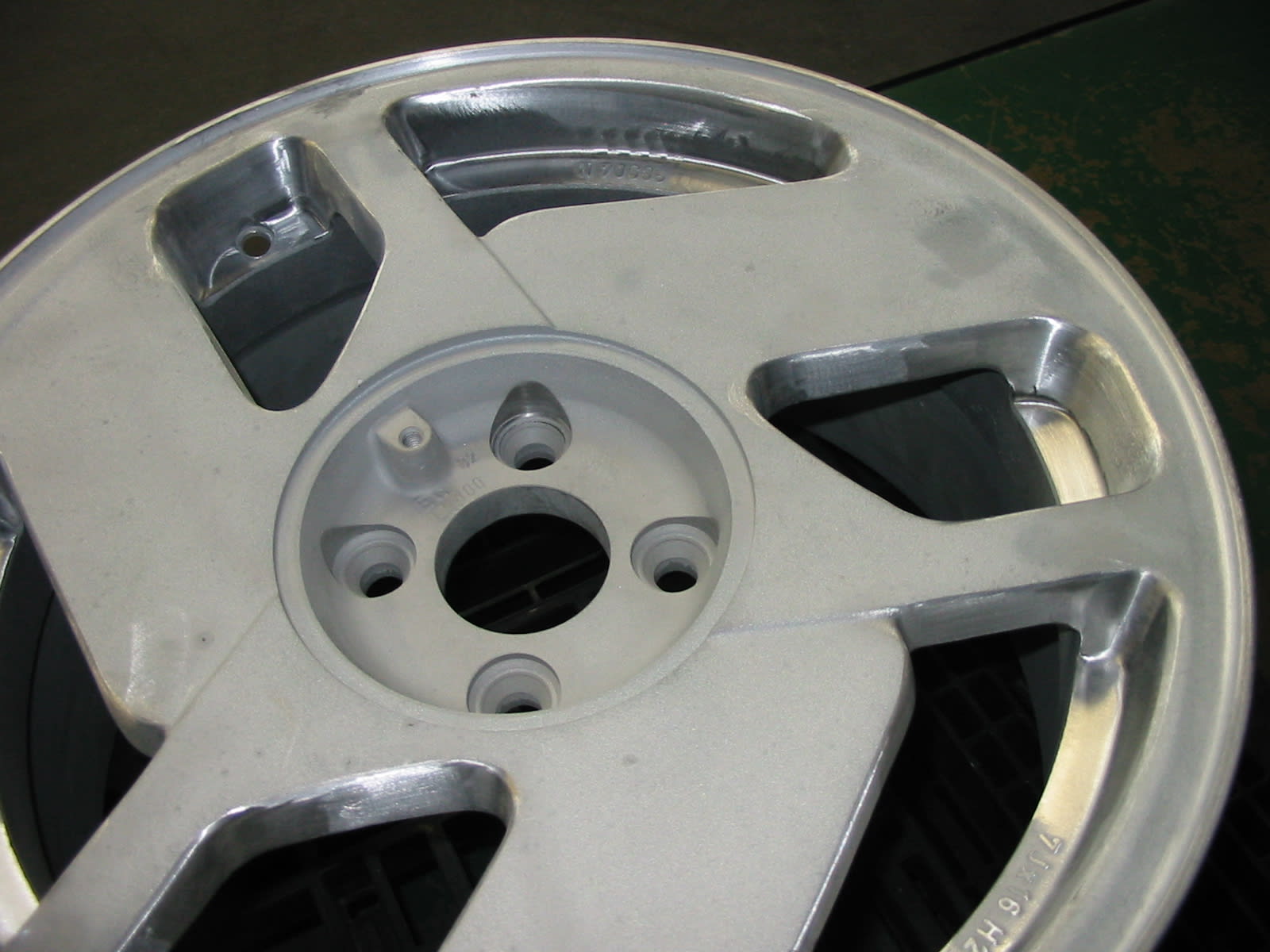
作業途中のノーテレのホイールです。カバーは撮り忘れ
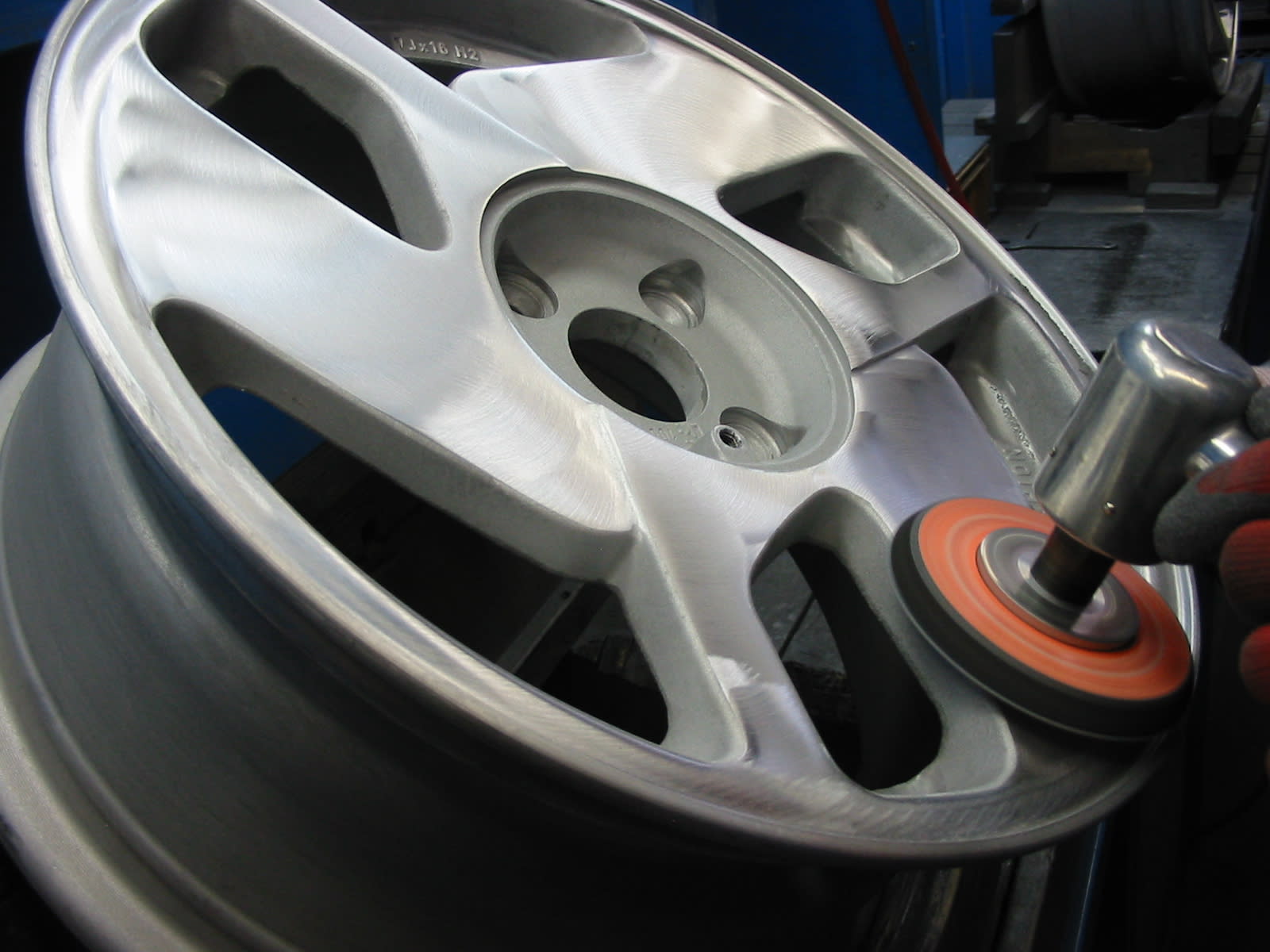
シングルサンダーを使いスパッと平面出し(プロの技です)

窓部はミニコやリューター、ベルトン・・・いろいろなツールを使用します。

荒研磨(#240)終わりました。次は#320~400場所により600の研磨へ。
続く
全体の工程は
1)粗削り#240~中削り#320~仕上げ削り#400~#600
2)荒バレル研磨
3)乾式バレル研磨
4)自動バフ研磨
5)光沢バレル研磨
6)湿式バフ研磨
7)検査
この工程の時間配分は削り部分が約7割占めています。機械化されてもいまだマンパワーに頼っているのが現状です。
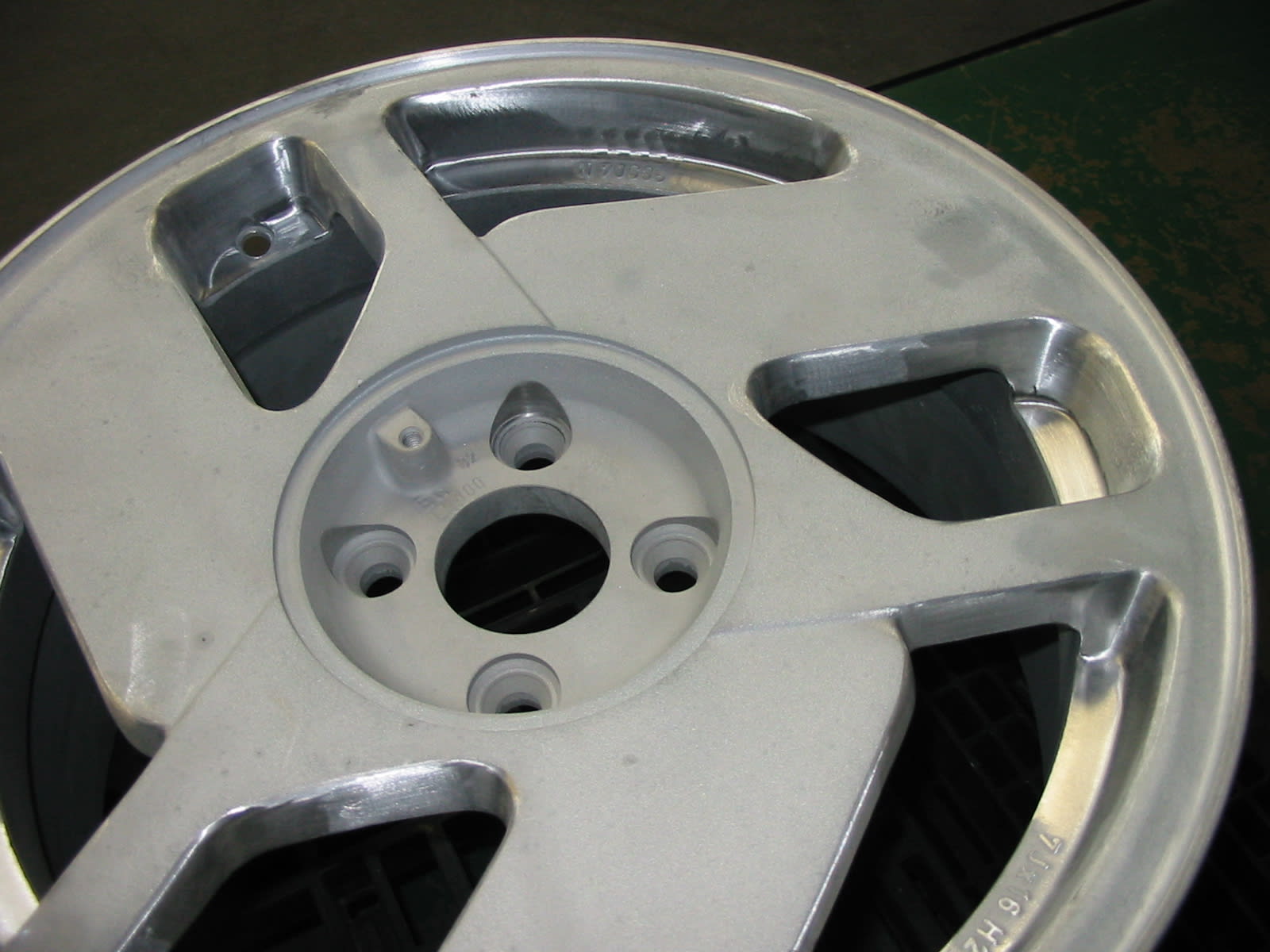
作業途中のノーテレのホイールです。カバーは撮り忘れ
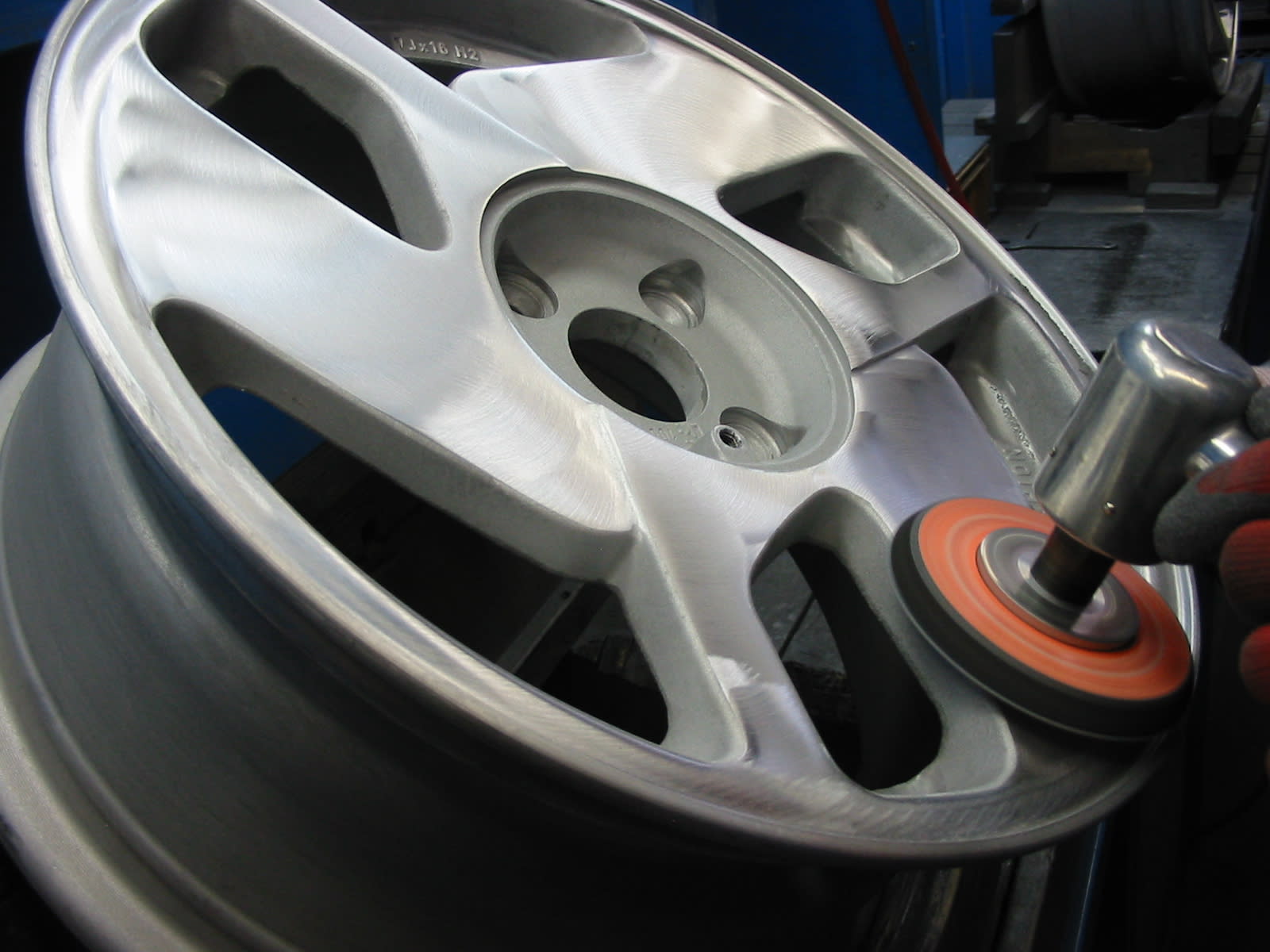
シングルサンダーを使いスパッと平面出し(プロの技です)

窓部はミニコやリューター、ベルトン・・・いろいろなツールを使用します。

荒研磨(#240)終わりました。次は#320~400場所により600の研磨へ。
続く