All I could do today is this photo.

These are the chopsticks I promissed to make
for one of the girls. Of these, two sets are
meant for lunch boxes.
They are short at 175 mm and thin enough,
meant to be cute and elegant in a feminine hand
at lunch hours.
Today for now I want to talk about coatings of these
artefatcs. As mentioned earlier I use polyurethane coating.
First three times they are subjected to penetration
coating. Polyurethane molecules are just so tiny and
penetrate into the artefacts very easily.
Each time drying process (24 hours) is complete,
they are closely examined for polyps. If I find any,
I remove them with sharp edges.
That still leaves micro-polyps, or dusts on the
surfaces. They are then wet sanded in water.
Altogether, I apply my coating 10 times.
Now, after three penetration coating with type A
polyurethane, urethane gets saturated on the surface.
That is when type C polyurethane is applied 6 times,
making the protective coating thicker and thicker.
Naturally, wet sanding continues each time.
By the time all this comes to an end you have extremely
glossy surfaces, with extremely strong protective
performance.
That is precisely when they are made mat with type E
polyurethane. So, I use three types of polyurethane
materials for the coating of my workpieces.
Naturally, all this is ridiculously excessive, but,
there you are. This is my way of doing my coatings.
The end products are extremely tough.
Polyurethanes are usd for coating of car bodies.
You must know how tough they are.
I just now go back to the following photo.
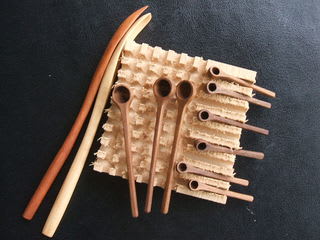
Those on the right are the smallest spoons
I construct. Their length is something like
5cm, and the cavity diameter is 5 mm.
Even these are coated 10times. Aed 3 times,
Ced 6 times, and finally Eed once, actually,
E coating is applied 3 or 4 times, more on that later.
What are these smallest spoons for?, you may ask.
They are meant for scooping habanero powders.
Well, so much for today.




These are the chopsticks I promissed to make
for one of the girls. Of these, two sets are
meant for lunch boxes.
They are short at 175 mm and thin enough,
meant to be cute and elegant in a feminine hand
at lunch hours.
Today for now I want to talk about coatings of these
artefatcs. As mentioned earlier I use polyurethane coating.
First three times they are subjected to penetration
coating. Polyurethane molecules are just so tiny and
penetrate into the artefacts very easily.
Each time drying process (24 hours) is complete,
they are closely examined for polyps. If I find any,
I remove them with sharp edges.
That still leaves micro-polyps, or dusts on the
surfaces. They are then wet sanded in water.
Altogether, I apply my coating 10 times.
Now, after three penetration coating with type A
polyurethane, urethane gets saturated on the surface.
That is when type C polyurethane is applied 6 times,
making the protective coating thicker and thicker.
Naturally, wet sanding continues each time.
By the time all this comes to an end you have extremely
glossy surfaces, with extremely strong protective
performance.
That is precisely when they are made mat with type E
polyurethane. So, I use three types of polyurethane
materials for the coating of my workpieces.
Naturally, all this is ridiculously excessive, but,
there you are. This is my way of doing my coatings.
The end products are extremely tough.
Polyurethanes are usd for coating of car bodies.
You must know how tough they are.
I just now go back to the following photo.
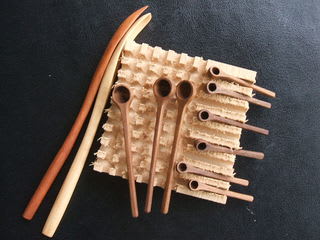
Those on the right are the smallest spoons
I construct. Their length is something like
5cm, and the cavity diameter is 5 mm.
Even these are coated 10times. Aed 3 times,
Ced 6 times, and finally Eed once, actually,
E coating is applied 3 or 4 times, more on that later.
What are these smallest spoons for?, you may ask.
They are meant for scooping habanero powders.
Well, so much for today.


