巷、この自転車業界では言葉の意味が独自発展してしまうことがあり、他業界から来ると へ?ってことが少なくないですね。例えば、フレームに使われてるのはCFRPで、カーボンを熱硬化性のエポキシ樹脂で固められたもので、カーボン繊維そのものの物理特性とは全く異なります。(しかし、まことしやかにカーボン繊維の特性がライディングに貢献しているような説明をしているブランドもあるらしい)それに、カーボン素材の種類によって得られる大きなメリットは、同じ剛性や弾性のフレームで重量を軽くすることができることだそうです。
モノコックって言葉の少々歪曲されて、金型で作ったCFRPフレームっていう意味に限定して使われるようになりました。スチールでもアルミでも、正確に言えばモノコックフレームは存在します。そもそも、自転車は言葉の定義からすれば、骨(柱?芯?)がないし、自転車フレームそのものがモノコックですよね(笑)
前置きはさておき、CFRPフレームの製造方法については、現在は大きく分けると3種類・・・・③の製造方法が意外と知られていないので、少し詳しく説明しますね。
①金型で製造する
②ラグでCFRPチューブをつなぐ方法
③CFRPチューブをラッピングでつなぐ方法
①金型で製造する、一般的にカーボンモノコックフレームと言われているフレーム。1980年代後半にKestrelが世界で初めて量産化しました。当時はオイルヒーティングで金型を温めたために、冷めるまで待たなきゃいけなくて、とても効率が悪く、1日2~3台しか作れなかった。しかも金型もオイルヒーティングの為に複雑でそのため高価でした。当時はサイズ毎に金型を用意したのもコストを押し上げた要因でした。現在は後ろ△部分を共通にして、前△に接着構造にして、コストを抑えているケースが多いです。しかも高温スチームヒーティングで冷却も早いので、大幅に効率化され コストが大幅に下げられました。数多くの大手ブランドがこれを採用しています。金型で製造する方法はさらに細かく区分することができるけど、ここでは割愛。
②ラグでCFRPチューブをつなぐ方法
①の方法が一般化するまで、この方式が主流でした。LOOKのカーボンラグフレームはクロモリチックな乗り味で、個人的にも好きでしたね(笑)
現在でも、コルナゴなどに採用。
③CFRPチューブをラッピングでつなぐ方法
2015年くらいからか?忘れたけれど、比較的新しい方法。CFRPチューブデザインを独自に設計して、お好みのジオメトリーでラッピングで成型する方法。これだとミリ単位のオーダーもできちゃうので、お客様の要望通りの注文が可能。CasatiやTommasini、サルトアントニオ等のイタリアのメーカーで採用されています。
CASATIのラッピング製造の様子
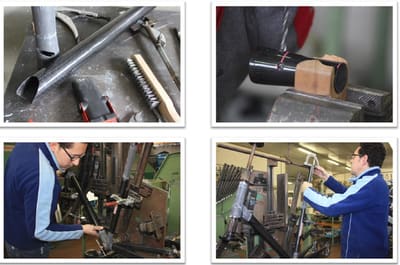
お客様の指定のジオメトリー合わせ、ジグを設定してカッティングしCFRPチューブをセット
レース用?ポタ用?ブルベ用?ヒルクライム用?希望通りのスケルトンで可能です!

丁寧に面取りをして、エポキシで固定します

プリプレグでラップします CASATIの場合は、東レの製品をつかっていますね
なので、フレーム重量はサイズにもよりますが900g前後です。

加熱処理すると・・・・ 外見上は金型製造のフレームとの違いが
まったくわからなくなります

カスタムオーダーってクロモリしかできないと勘違いしてはいけません。アルミ・チタンはもとより、このようにカーボンもできちゃうのです!
自分のこのサイズを測って、目的をはっきり伝えましょう。
最近では、こんなリスエストがありました。「アップライト気味で、25~30km/hくらいで、週末150km前後のサイクリングフレームをつくってください。」個人的にはシンパシーを感じましたね(笑)

モノコックって言葉の少々歪曲されて、金型で作ったCFRPフレームっていう意味に限定して使われるようになりました。スチールでもアルミでも、正確に言えばモノコックフレームは存在します。そもそも、自転車は言葉の定義からすれば、骨(柱?芯?)がないし、自転車フレームそのものがモノコックですよね(笑)
前置きはさておき、CFRPフレームの製造方法については、現在は大きく分けると3種類・・・・③の製造方法が意外と知られていないので、少し詳しく説明しますね。
①金型で製造する
②ラグでCFRPチューブをつなぐ方法
③CFRPチューブをラッピングでつなぐ方法
①金型で製造する、一般的にカーボンモノコックフレームと言われているフレーム。1980年代後半にKestrelが世界で初めて量産化しました。当時はオイルヒーティングで金型を温めたために、冷めるまで待たなきゃいけなくて、とても効率が悪く、1日2~3台しか作れなかった。しかも金型もオイルヒーティングの為に複雑でそのため高価でした。当時はサイズ毎に金型を用意したのもコストを押し上げた要因でした。現在は後ろ△部分を共通にして、前△に接着構造にして、コストを抑えているケースが多いです。しかも高温スチームヒーティングで冷却も早いので、大幅に効率化され コストが大幅に下げられました。数多くの大手ブランドがこれを採用しています。金型で製造する方法はさらに細かく区分することができるけど、ここでは割愛。
②ラグでCFRPチューブをつなぐ方法
①の方法が一般化するまで、この方式が主流でした。LOOKのカーボンラグフレームはクロモリチックな乗り味で、個人的にも好きでしたね(笑)
現在でも、コルナゴなどに採用。
③CFRPチューブをラッピングでつなぐ方法
2015年くらいからか?忘れたけれど、比較的新しい方法。CFRPチューブデザインを独自に設計して、お好みのジオメトリーでラッピングで成型する方法。これだとミリ単位のオーダーもできちゃうので、お客様の要望通りの注文が可能。CasatiやTommasini、サルトアントニオ等のイタリアのメーカーで採用されています。
CASATIのラッピング製造の様子
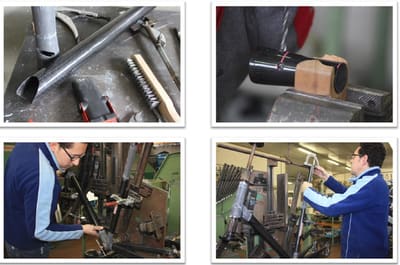
お客様の指定のジオメトリー合わせ、ジグを設定してカッティングしCFRPチューブをセット
レース用?ポタ用?ブルベ用?ヒルクライム用?希望通りのスケルトンで可能です!

丁寧に面取りをして、エポキシで固定します

プリプレグでラップします CASATIの場合は、東レの製品をつかっていますね
なので、フレーム重量はサイズにもよりますが900g前後です。

加熱処理すると・・・・ 外見上は金型製造のフレームとの違いが
まったくわからなくなります

カスタムオーダーってクロモリしかできないと勘違いしてはいけません。アルミ・チタンはもとより、このようにカーボンもできちゃうのです!
自分のこのサイズを測って、目的をはっきり伝えましょう。
最近では、こんなリスエストがありました。「アップライト気味で、25~30km/hくらいで、週末150km前後のサイクリングフレームをつくってください。」個人的にはシンパシーを感じましたね(笑)

※コメント投稿者のブログIDはブログ作成者のみに通知されます