Conchita, today was not too bad...
Coating continued and the first image below is
just before protective coating was applied.
Quite when to proceed to the next step of coating
does depend on the surface status. You have to have
a good and long look at them before you decide...
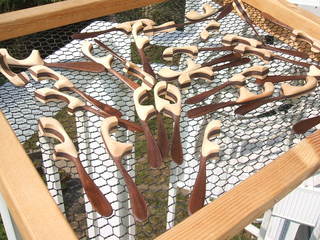
In the meatime toast bed work continued and halfway
through I was beginning to think that I was perhaps
trying to fabricate too many of them...
There are nine here, those I made today, and combined
with earlier pieces I now have close to 30 of them.
Quite realistically, I do not believe for a moment that
people will be buying these at the constant rate of
5 or 6/day for the duration of the department thing...
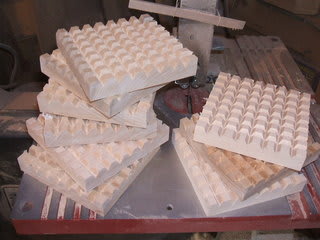
So, what is seen below will be left untouched for the
time being. They will sell, yes, eventually, as earlier
pieces have been sold out!
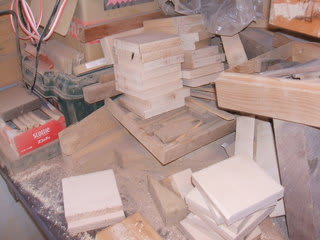
Today, I was bored of making the toast beds, and I decided
to go out by car to buy a soft iron bar, and I came across
a smaller sanding bit, as shown here.
If you are into this kind of work as I am you need
a variety of sanding bits, and I immediately bought this!
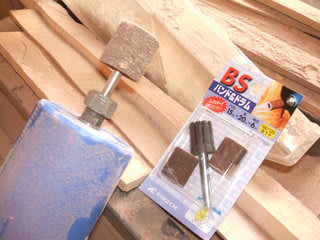
The 5 mm soft iron bar was sliced into something like 5 mm
length. What is seen below is just a confirmation test,
with the neosium magnets and the sliced out soft iron counterparts.
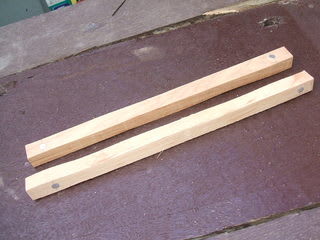
I made 5 mm holes and they were just about right, and
what I did subsequently was to glue them in the holes
so that I can verify my theory of tow halves of my
chopstics covers sticking together with enough force.
Without bonding these pieces will shoot out from the
holes and I will see for sure that I am right,
only tommorrow, or later this evening.
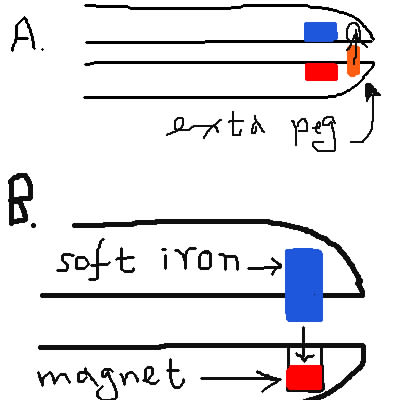
The schematic above is in relaton to precise
alingnment of the covers. Magnets and their
soft iron counterparts are only meant for
closing the gap between the covers. Actually,
with the presence of the magnets they are
intrinsically self-alligning (mis-spelling!).
However, an idea was put forward that we need
something more to ensure an exact contact. A very
naieve solution would have been to have
protruding pegs and counterpart holes to accept them,
as in A here.
My instinctive solution is to make the soft iron
itself to protrude as in B. Of course, tips will have
to be rounded and in the worst case bore diamtre may
have to be altered, but the basic idea is there,
I think.
Anyway, these are the thoughts which emerged today
during the boring process of groove cutting.
Tomorrow, I will be working on the chopstics containers
in earnest!



Coating continued and the first image below is
just before protective coating was applied.
Quite when to proceed to the next step of coating
does depend on the surface status. You have to have
a good and long look at them before you decide...
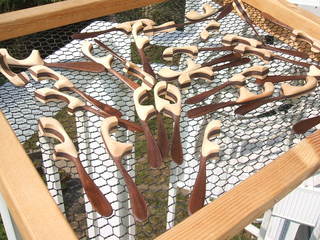
In the meatime toast bed work continued and halfway
through I was beginning to think that I was perhaps
trying to fabricate too many of them...
There are nine here, those I made today, and combined
with earlier pieces I now have close to 30 of them.
Quite realistically, I do not believe for a moment that
people will be buying these at the constant rate of
5 or 6/day for the duration of the department thing...
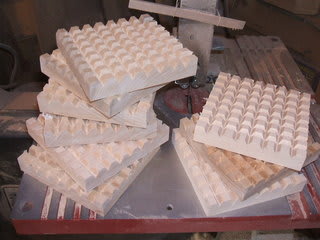
So, what is seen below will be left untouched for the
time being. They will sell, yes, eventually, as earlier
pieces have been sold out!
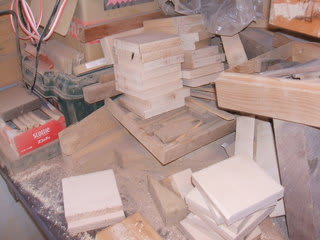
Today, I was bored of making the toast beds, and I decided
to go out by car to buy a soft iron bar, and I came across
a smaller sanding bit, as shown here.
If you are into this kind of work as I am you need
a variety of sanding bits, and I immediately bought this!
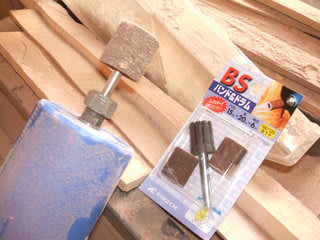
The 5 mm soft iron bar was sliced into something like 5 mm
length. What is seen below is just a confirmation test,
with the neosium magnets and the sliced out soft iron counterparts.
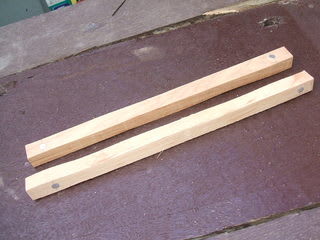
I made 5 mm holes and they were just about right, and
what I did subsequently was to glue them in the holes
so that I can verify my theory of tow halves of my
chopstics covers sticking together with enough force.
Without bonding these pieces will shoot out from the
holes and I will see for sure that I am right,
only tommorrow, or later this evening.
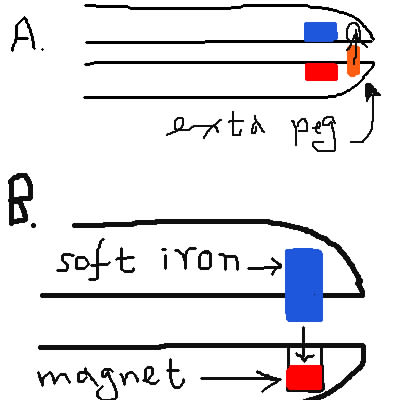
The schematic above is in relaton to precise
alingnment of the covers. Magnets and their
soft iron counterparts are only meant for
closing the gap between the covers. Actually,
with the presence of the magnets they are
intrinsically self-alligning (mis-spelling!).
However, an idea was put forward that we need
something more to ensure an exact contact. A very
naieve solution would have been to have
protruding pegs and counterpart holes to accept them,
as in A here.
My instinctive solution is to make the soft iron
itself to protrude as in B. Of course, tips will have
to be rounded and in the worst case bore diamtre may
have to be altered, but the basic idea is there,
I think.
Anyway, these are the thoughts which emerged today
during the boring process of groove cutting.
Tomorrow, I will be working on the chopstics containers
in earnest!


