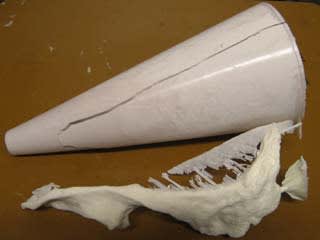
前回に引き続き流木の型取り
無事にシリコーンゴムが硬化しました
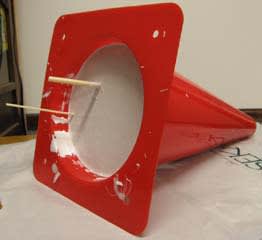
型枠からゴム型を抜きます
だが、がっちりとくっついていて抜けない、そこでプッチンプリン方式で底に穴をあけて押しだす方法でと思ったのだがゴムの方に突き出し棒がめり込んで無理
仕方ないので型枠を切ってはずします、バックアップジャケットとして使用できなくなったので、同じコーンをもう1個買ってくる
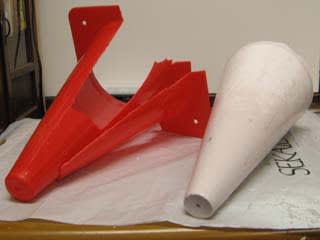
ゴム型をカッターで切り裂いて、原型をはずす
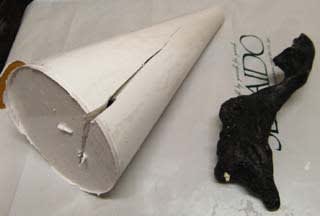
注入口を広げる

再度コーンにセットする、切り目がずれないように注意する
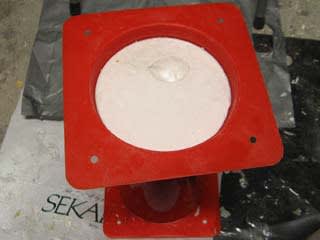
プラキャストを注型する、GSIクレオスのMr.キャスト・ノンキシレンアイボリーを使用
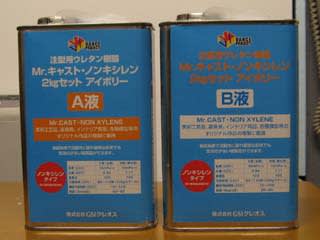
秤でA液、B液を等量計る、100gづつにしています
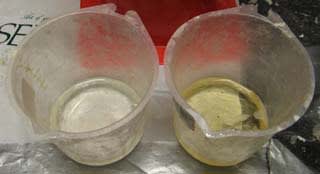
キャストの量をどうやって決めるか
缶に記載されている物性表では、比重がA液0.94、B液1.11となっています
混合して硬化させた時の比重は大体1.0と見てよいでしょう
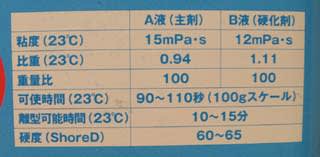
原型の体積を測定する
原型を水を張った水槽に沈めて増えた水位で体積を求める
体積×比重で、キャスト必要量を算出する
水槽を用意するのが面倒ですね、今回はもっと適当に行います
原型の重さを秤で測る、今回のは200g、水に浮く木なので比重は1.0以下と考えられます、それで、A液、B液ともに100g+αにして注型する、注型後に余ったキャストの量を測って次回の注型からこの分を引いた量にします
注型する、硬化するまで振動させて空気を抜く
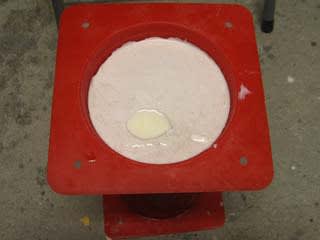
硬化後、型からはずす
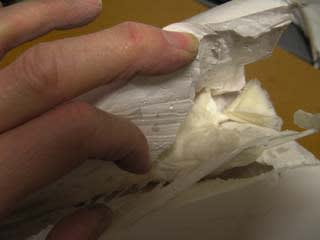
型に無理がかかっているので、はずすたびに型が裂けていってますが、注型数が少ないので問題ありません
型から取り出した状態
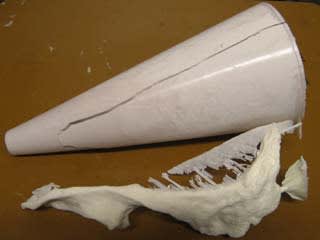
成型品
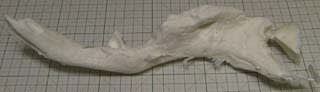
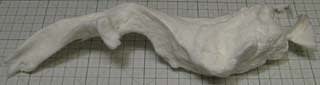
気泡が結構ありますが、この方法では、空気抜きを後で追加は難しい

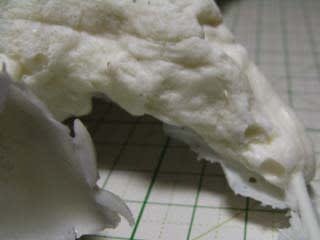
いろいろ問題点がある型取り方法ですが、早く型取りできるのが良いところです
流木を型取りしていったいどうするのか、全ては謎のまま型取りの説明は終わり、次回はガンダムの作業に戻ります
前回を読む
シリコーンゴムによる型取り(流木を型取りする 1回)
無事にシリコーンゴムが硬化しました
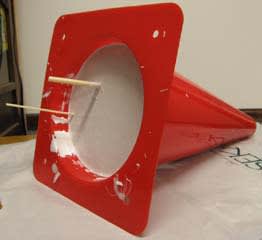
型枠からゴム型を抜きます
だが、がっちりとくっついていて抜けない、そこでプッチンプリン方式で底に穴をあけて押しだす方法でと思ったのだがゴムの方に突き出し棒がめり込んで無理
仕方ないので型枠を切ってはずします、バックアップジャケットとして使用できなくなったので、同じコーンをもう1個買ってくる
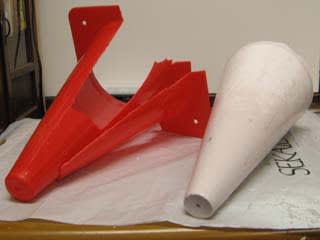
ゴム型をカッターで切り裂いて、原型をはずす
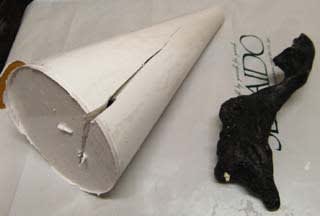
注入口を広げる

再度コーンにセットする、切り目がずれないように注意する
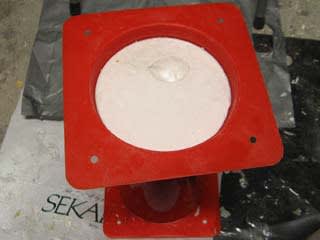
プラキャストを注型する、GSIクレオスのMr.キャスト・ノンキシレンアイボリーを使用
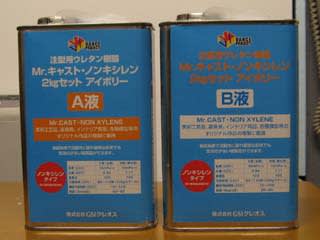
秤でA液、B液を等量計る、100gづつにしています
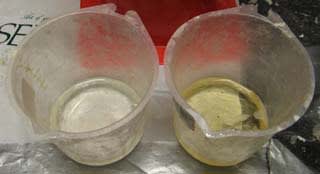
キャストの量をどうやって決めるか
缶に記載されている物性表では、比重がA液0.94、B液1.11となっています
混合して硬化させた時の比重は大体1.0と見てよいでしょう
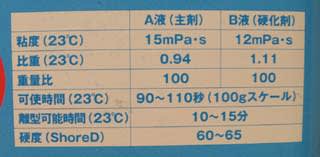
原型の体積を測定する
原型を水を張った水槽に沈めて増えた水位で体積を求める
体積×比重で、キャスト必要量を算出する
水槽を用意するのが面倒ですね、今回はもっと適当に行います
原型の重さを秤で測る、今回のは200g、水に浮く木なので比重は1.0以下と考えられます、それで、A液、B液ともに100g+αにして注型する、注型後に余ったキャストの量を測って次回の注型からこの分を引いた量にします
注型する、硬化するまで振動させて空気を抜く
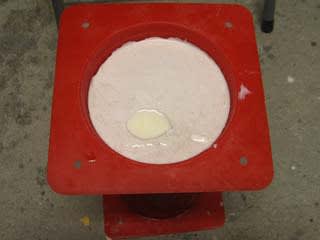
硬化後、型からはずす
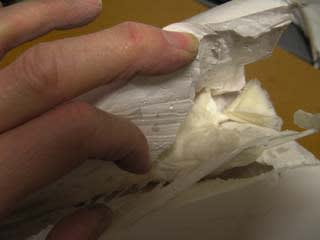
型に無理がかかっているので、はずすたびに型が裂けていってますが、注型数が少ないので問題ありません
型から取り出した状態
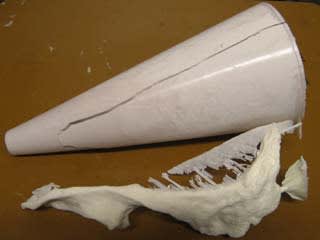
成型品
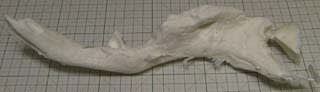
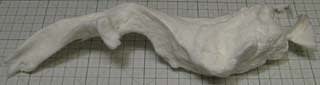
気泡が結構ありますが、この方法では、空気抜きを後で追加は難しい

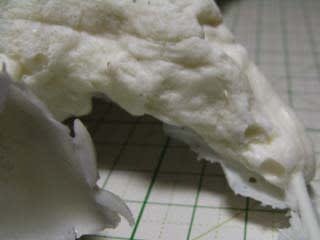
いろいろ問題点がある型取り方法ですが、早く型取りできるのが良いところです
流木を型取りしていったいどうするのか、全ては謎のまま型取りの説明は終わり、次回はガンダムの作業に戻ります
前回を読む
シリコーンゴムによる型取り(流木を型取りする 1回)
※コメント投稿者のブログIDはブログ作成者のみに通知されます