OK, very similar to yesterday's, but the tongs just
before being assembled. They are drying after wet
sanding...

What follows shows them, temporarily put together. Today,
I could not do anything else, really...
For a start, it was very warm today, and I was being
lethergic, anyway. Taking it all easy, sitting at the back
of my house in the shadow, that sort of thing...

Reaching the stage above was not easy, at all. Simply becase
each tong was different, yes, I intedned them to be of the
same dimenstion, but they are not, in reality.

Above just shows you the pieces left over from my cutting
operation, that is to say that I had to cut short those
mini bolts to suit my tongs. However, that was not easy,
either.
I will come on to that shortly.

Problem is this. You cannot shorten those mini bolts
to the exact lengths required. Lucky that I have this machine,
which is a bandsaw for metal cutting! Very expensive, but versatile!
Now, you inevitably have protrusions above the mini nuts.
You want to get rid of them, to make space for the trench
lids, or covers, or whatever you might call them.
Ideally, I want somthing like 3 mm clearance, above the
nut and bellow the trench surface...
So, what do you do? I used this diamond disk sander,
shown above. OK, that is one thing you can do.
However, there is a fundamental issue, as illustrated
bellow.
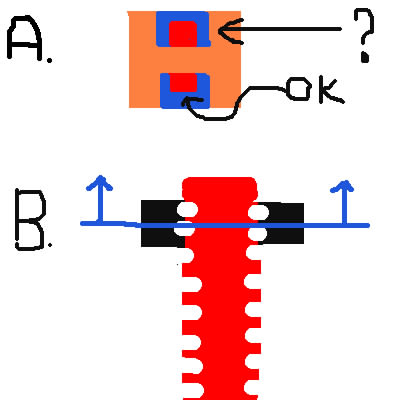
Schematic A is very misleading, but I will dare
explain the reason. The starting material (that is,
the handle thickness) is about...? 15 mm, plus or minus
1 mm...
Cutting depth is the same, at 5 mm, plus or minus 0.5 mm...
OK, one end of a mini bolt is fixed, but with the other end
I must close it with a mini nut, which is not fixed.
That is where protrusions sneak in...
What I am on about is that at the end of the day I want
a sufficient depth for my trench lids. Basically, I will
need to glue the lids in the trench space, and for that
I need some depth...
A is conceptual and distorted and out of balance
in view of that fact the cutting depth was the same,
but it does show you my point.
The obviously less depth is representative of my thinking,
the tickness of the mini nut and the protrusion
therewith...
I can do two things here. As shown with the schematic B
I can use my milling machine to make thinner nuts.
That is, I can remove anything above the blue line,
and obtain more depth for glueing the lids to the sides
of the trench.
However, my instinctive and current thinking is to go for
something like 18 mm handle thickness in the first place.
Cutting metals is very carbon intensive, but using slightly
thicker wooden pieces to work with would mean much lower
carbon released into the atmosphere...
That is my judgement.


before being assembled. They are drying after wet
sanding...

What follows shows them, temporarily put together. Today,
I could not do anything else, really...
For a start, it was very warm today, and I was being
lethergic, anyway. Taking it all easy, sitting at the back
of my house in the shadow, that sort of thing...

Reaching the stage above was not easy, at all. Simply becase
each tong was different, yes, I intedned them to be of the
same dimenstion, but they are not, in reality.

Above just shows you the pieces left over from my cutting
operation, that is to say that I had to cut short those
mini bolts to suit my tongs. However, that was not easy,
either.
I will come on to that shortly.

Problem is this. You cannot shorten those mini bolts
to the exact lengths required. Lucky that I have this machine,
which is a bandsaw for metal cutting! Very expensive, but versatile!
Now, you inevitably have protrusions above the mini nuts.
You want to get rid of them, to make space for the trench
lids, or covers, or whatever you might call them.
Ideally, I want somthing like 3 mm clearance, above the
nut and bellow the trench surface...
So, what do you do? I used this diamond disk sander,
shown above. OK, that is one thing you can do.
However, there is a fundamental issue, as illustrated
bellow.
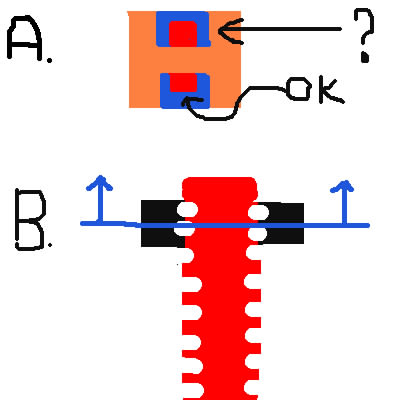
Schematic A is very misleading, but I will dare
explain the reason. The starting material (that is,
the handle thickness) is about...? 15 mm, plus or minus
1 mm...
Cutting depth is the same, at 5 mm, plus or minus 0.5 mm...
OK, one end of a mini bolt is fixed, but with the other end
I must close it with a mini nut, which is not fixed.
That is where protrusions sneak in...
What I am on about is that at the end of the day I want
a sufficient depth for my trench lids. Basically, I will
need to glue the lids in the trench space, and for that
I need some depth...
A is conceptual and distorted and out of balance
in view of that fact the cutting depth was the same,
but it does show you my point.
The obviously less depth is representative of my thinking,
the tickness of the mini nut and the protrusion
therewith...
I can do two things here. As shown with the schematic B
I can use my milling machine to make thinner nuts.
That is, I can remove anything above the blue line,
and obtain more depth for glueing the lids to the sides
of the trench.
However, my instinctive and current thinking is to go for
something like 18 mm handle thickness in the first place.
Cutting metals is very carbon intensive, but using slightly
thicker wooden pieces to work with would mean much lower
carbon released into the atmosphere...
That is my judgement.


