3.業務改善の事例
実際の改善提案の内容は千差万別だが、ここではタイの日系工場の事例を紹介する。
(1)専門語の説明
事例の紹介に先立ち、この説明に出てくる生産管理用語を簡単に解説する。
1)単独工程
1台(セット)の機械または装置で材料を加工し、部品や製品を生産する工程をいう。
例:鉄板から部品を打ち抜く工程
2)連続工程
複数の工程を連結した工程をいう。初工程に材料を投入し、最終工程で部品や製品を仕上げる。
途中の工程で別の材料を投入することもある。例:鉄板を投入⇒切断⇒穴あけ⇒仕上げ
3)サイクルタイム(Cycle Time)
単独工程や連続工程が1つの部品や製品を仕上げる時間。機械部品の場合は秒単位が多い。
例:サイクルタイム=30秒 ならば 30秒に1個の部品や製品が仕上る。
4)生産基礎情報
品目テーブル(材料、部品、製品などのデータ)、部品表(使用材料のデータ)、工程順序表(加工順序
やサイクルタイムなどのデータ)などの総称で、工場のデータベースである。
(2)事例の説明
現状分析の結果、主力製品の生産性に問題があることが分かった。生産性の問題と同時に、当時、材料の高騰と為替レートの悪化で製品コストの削減も急務となっていた。
そこで、主力製品の一つに的を絞って、生産指示数、サイクルタイム、オペレーター達の動作など、「人、もの、情報」の流れを分析した。この工程は製品ABCの最終組立てラインで、見直し作業にはオペレーターも参加した。
説明が長くなるので詳しい内容は省略するが、問題を要約すると下の図のようになる。図の黄色の部分は「Before(改善前)」、緑の部分は「After(改善後)」を示している。
生産性改善の事例---改善前と改善後
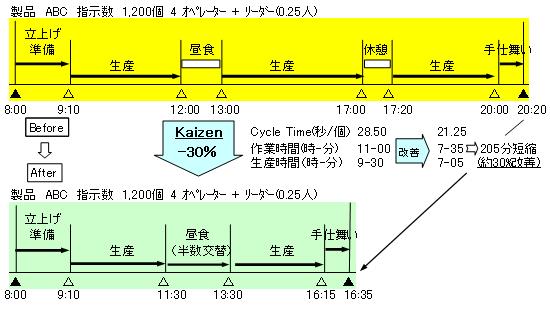
出典:筆者著“生産管理の理論と実践” COMM Bangkok、2010
上の図に示すとおり、改善前の工程は朝8時-20時の作業で1,200個の製品ABCを生産していた。「プリセット」「組立て」「塗装/乾燥/検査」の3つの単独工程で編成したこの組立工程を4人の女性オペレーターが担当していた。
改善策
1)3つの単独工程を1つの連続工程に変更、この変更に伴う生産基礎情報の見直し。
2)改善前の作業効率は、サイクルタイムベースで68.4%だった。
工程の連結とその運用を改善し、サイクルタイムを22秒に短縮した。
試算の結果、余裕率を考慮しても製品ABCの生産は17時頃に終了すると判断した。
3)“効率68.4%は、100点満点の70点程度、これはCクラスの仕事である。
せめて80点前後のBクラス、できれば90点以上のAクラスを達成し、世界の工場に向かって胸を
張って欲しい”とオペレーターのプライドに訴えた。
結果
1)約2週間の試行錯誤で、図の緑色に示すように作業時間を約30%短縮した。
2)昼食時間の半数交替はオペレーター達の発案、これにより塗装乾燥装置は連続運転になった。
3)女性オペレーターの自発的な改善は、サイクルタイムベースで91.7%とAクラスに到達した。
生産性は非常に高いが、時どき機械周りを掃除・整頓する余裕が残っていた。
4)工程の連続化のために設備を移動しただけで、他のコストは発生しなかった。
5)この改善は工場全体に知れ渡り、自分たちも“やればできる(Can do)”という自信を持つと同時に、
“Kaizen”への関心が高まった。
(注:単純化のため説明を省いたが、実際にはこの製品ABCを21時から翌朝6時まで引続き生産
していたので、改善の効果は大きかった)
この改善が引金となって、全社的にサイクルタイムや生産指示数の見直しが始まった。やがて、他製品の生産性の見直しに波及し、増産への道が開けた。また、新しいデータにもとづく原価分析で、顧客・工場の双方が納得できる価格交渉が成立した。
次回のグローバルシステムは休み、代わりに石垣島旅行を10月末に掲載する。