ここに掲載した写真の多くは、寒冷地使用車のもの。融雪剤(塩カリ剤)の影響が、以下にクルマの基本骨格にダメージを与えるかということを感じさせます。
腐食減肉とは恐ろしきもの
2019-07-15 | 技術系情報
腐食減肉とは恐ろしきもの
レストアのことで記事を再掲したところ、予想を超えた好反応を得て、改めてこの分野で旧車に感心を持っている方が多いことを実感しています。197、80年代までのモノコック乗用車では、大方の外板および内板パネルは0.9mm程度の冷延圧延鋼板で作られます。サイドフレームなどの特に強度が必要な部位でも、その板厚は1.6mm程度であり、これだけで強度が不足の場合は、その断面積を増すなどして必要強度得ている若です。従って、鋼板を被覆し保護している塗装が飛び石などのチッピングによりキズ付いたり、角型閉断面構造部位だとか、ドア下部やボンネット先端のアウターとインナーがヘミング処理されてる内部に、長期間水溜まりや、寒冷地の塩カリが含まれた状態で経過すると、その内部から腐食は進行する訳です。ここで船舶だとか重量鉄鋼の厚板鋼板であれば、腐食により減肉が生じても、相当な期間、孔食などを生じることなく耐えることが出来ますが、そもそも鋼板自体が薄いため、一旦錆が生じし始めると腐食はごく短期間で進行し、外面的な孔食程度で済めばまだ良い方で、強度的にまったく不足の状態に陥る訳です。
およそ1980年頃を境に、我が国の車両メーカーも、本格的な錆対策の研究を行い、以下の様な対策を講じてきました。
①下塗りの電着塗装工程(以下ED塗装と記す)ですが、従来のアニオンEDから、その反対電極となるカチオンEDと呼ばれる被塗物がー電極に、水溶性塗料が+電極の電位差で、水溶性塗料を鋼板面に吸着させるという方式に置き換わっています。この利点は、私は塗装の専門家ではありませんが、ED工程の前工程として行われる化成皮膜処理工程という車体をリン酸亜鉛溶液に浸漬させせ、金属表面を適度に荒らす(食いつきを良くする足付け研磨に相当する)と共に、極薄膜のリン酸亜鉛被膜を形成するという工程です。ちなみに、この工程を経て市販される鋼板を、通称ボンデ鋼板と呼ばれます。元々の冷延鋼板と比べると表面が適度に荒れるため、鈍い反射を持つ状態となります。カチオン電着では、このリン酸亜鉛被膜が溶け出さないという利点があることを昔のことですが聞いております。
②ED塗装におけるボデーの塗料溶液への浸漬ですが、最近はある程度深い塗料層を用いて、ベルトコンベアによる移動中にボデーを1回転反転させ、閉断面部に形成させてしまう空気溜りから塗料未着部が生じることを極力防ぐ様にすると共に、適宜エア抜き用のホールを設置し、複雑な閉断面構造におけるエア溜まりが生じない様にも留意しています。
③ED塗装の水性塗料ですが、より耐候性と密着性として樹脂性能が良好なエポキシ樹脂塗料を使用に変更しています。なお、この1液水性エポキシ塗料ですが、ブロック材を混入してあり、塗装後の焼き付け硬化工程において、重合反応(架橋反応とも云う)により、分子構造が網目構造となることで、高い耐候性と耐溶剤性を確保しています。
④それでも水溜まりが生じ易い車両の主に下部などの閉断面部や車両の外部などで、チッピングと呼ばれる自車両が跳ね上げた飛び石などによる塗膜の剥がれから発錆が進行するのを防止するため、両面亜鉛メッキ鋼板が錆びに厳しい部位に使用されます。なお、純な亜鉛メッキは塗料の密着性が悪化することや塗装面に品質が劣るため、外面側の亜鉛メッキ層を深層では亜鉛を多く、表層では亜鉛を少なくして外面の塗装品質を落とさない様にした亜鉛メッキ鋼板(商品名の例としてはエクセライト鋼板など)に類したものを主に外板パネルに使用し、外板面の塗膜品質を落とさない様に留意している様です。
⑤閉断面とか鋼板合わせ面の隙間の適宜シーリングにより塞ぐことで、鋼板の合わせ目に水分が浸透し、滞留することを防止することに留意したボデー設計とすると共に、適宜水抜き穴を設置するなどして、長期間の身時溜まりを防止する様に留意しています。
⑥塗装後に鋼板面の新たに艤装する各種トリミング材やブラケット類の装着は、鋼板の塗装を破壊しない様、中間に樹脂グロメットを介在しスクリューで固定するなどして、塗膜破壊部からの錆の発生の起点となることを防止しています。その他、従来は、ボデー面装着のエンブレム等は、その装着部位を確実にするため、差し込み内部拡張式の金属金具が使用されていましたが、ほとんどが両面テープによる接着に変化し、差し込み式を使用する場合でも中間に軟質樹脂グロメットを介在させ塗膜の破壊を防止しています。なお、軽量樹脂部品の装着では、樹脂クリップの使用により塗膜の破壊が生じない様留意しています。
⑦以上でも防錆上で不安が持たれる部位(主に閉断面部)には、防錆ワックス(蝋)を加熱噴射して防錆力をさらに補強しています。これは私の個人的観察ですが、日本車より欧州車の方が防錆ワックスの塗布量は多いと感じています。これは、使用過程において、ドアのモールやアウトサイドハンドルなどの隙間から流れ落ちる縦方向の染みが、欧州車に多いと感じることから推察している傾向なのです。
以上の様な防錆力の向上を図った国産車ですが、沿岸地区や北国の仕様車においては、驚くべき腐食の現状が新車から20年以内で生じている現実があるのです。以下の写真は、それら主に車体骨格部の極めて重要な構造部に破滅的な腐食を生じているという現実写真を羅列してみます。
なお、ふそう大型バスのフロントサスペンションロワアームを支持するセンターメンバ部については、新車登録後20年を越えてリコール処理が行われているものです。この部位は板厚が7.0mmもある厚板鋼板ですが、大型車のカチオンED塗装は乗用車に比べ20年後に始まったものであることや、水はけの悪いことなどが招いたものです。しかし、同メーカーに対する、それまでの行って来た不審から生じた罰でもあるのだとは私見なのです。








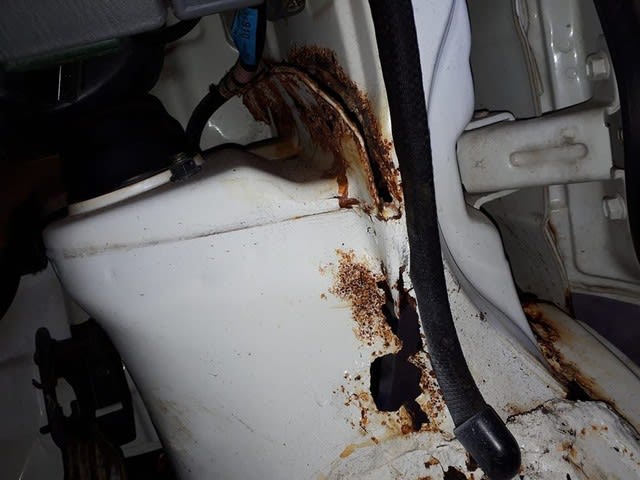


腐食減肉とは恐ろしきもの
2019-07-15 | 技術系情報
腐食減肉とは恐ろしきもの
レストアのことで記事を再掲したところ、予想を超えた好反応を得て、改めてこの分野で旧車に感心を持っている方が多いことを実感しています。197、80年代までのモノコック乗用車では、大方の外板および内板パネルは0.9mm程度の冷延圧延鋼板で作られます。サイドフレームなどの特に強度が必要な部位でも、その板厚は1.6mm程度であり、これだけで強度が不足の場合は、その断面積を増すなどして必要強度得ている若です。従って、鋼板を被覆し保護している塗装が飛び石などのチッピングによりキズ付いたり、角型閉断面構造部位だとか、ドア下部やボンネット先端のアウターとインナーがヘミング処理されてる内部に、長期間水溜まりや、寒冷地の塩カリが含まれた状態で経過すると、その内部から腐食は進行する訳です。ここで船舶だとか重量鉄鋼の厚板鋼板であれば、腐食により減肉が生じても、相当な期間、孔食などを生じることなく耐えることが出来ますが、そもそも鋼板自体が薄いため、一旦錆が生じし始めると腐食はごく短期間で進行し、外面的な孔食程度で済めばまだ良い方で、強度的にまったく不足の状態に陥る訳です。
およそ1980年頃を境に、我が国の車両メーカーも、本格的な錆対策の研究を行い、以下の様な対策を講じてきました。
①下塗りの電着塗装工程(以下ED塗装と記す)ですが、従来のアニオンEDから、その反対電極となるカチオンEDと呼ばれる被塗物がー電極に、水溶性塗料が+電極の電位差で、水溶性塗料を鋼板面に吸着させるという方式に置き換わっています。この利点は、私は塗装の専門家ではありませんが、ED工程の前工程として行われる化成皮膜処理工程という車体をリン酸亜鉛溶液に浸漬させせ、金属表面を適度に荒らす(食いつきを良くする足付け研磨に相当する)と共に、極薄膜のリン酸亜鉛被膜を形成するという工程です。ちなみに、この工程を経て市販される鋼板を、通称ボンデ鋼板と呼ばれます。元々の冷延鋼板と比べると表面が適度に荒れるため、鈍い反射を持つ状態となります。カチオン電着では、このリン酸亜鉛被膜が溶け出さないという利点があることを昔のことですが聞いております。
②ED塗装におけるボデーの塗料溶液への浸漬ですが、最近はある程度深い塗料層を用いて、ベルトコンベアによる移動中にボデーを1回転反転させ、閉断面部に形成させてしまう空気溜りから塗料未着部が生じることを極力防ぐ様にすると共に、適宜エア抜き用のホールを設置し、複雑な閉断面構造におけるエア溜まりが生じない様にも留意しています。
③ED塗装の水性塗料ですが、より耐候性と密着性として樹脂性能が良好なエポキシ樹脂塗料を使用に変更しています。なお、この1液水性エポキシ塗料ですが、ブロック材を混入してあり、塗装後の焼き付け硬化工程において、重合反応(架橋反応とも云う)により、分子構造が網目構造となることで、高い耐候性と耐溶剤性を確保しています。
④それでも水溜まりが生じ易い車両の主に下部などの閉断面部や車両の外部などで、チッピングと呼ばれる自車両が跳ね上げた飛び石などによる塗膜の剥がれから発錆が進行するのを防止するため、両面亜鉛メッキ鋼板が錆びに厳しい部位に使用されます。なお、純な亜鉛メッキは塗料の密着性が悪化することや塗装面に品質が劣るため、外面側の亜鉛メッキ層を深層では亜鉛を多く、表層では亜鉛を少なくして外面の塗装品質を落とさない様にした亜鉛メッキ鋼板(商品名の例としてはエクセライト鋼板など)に類したものを主に外板パネルに使用し、外板面の塗膜品質を落とさない様に留意している様です。
⑤閉断面とか鋼板合わせ面の隙間の適宜シーリングにより塞ぐことで、鋼板の合わせ目に水分が浸透し、滞留することを防止することに留意したボデー設計とすると共に、適宜水抜き穴を設置するなどして、長期間の身時溜まりを防止する様に留意しています。
⑥塗装後に鋼板面の新たに艤装する各種トリミング材やブラケット類の装着は、鋼板の塗装を破壊しない様、中間に樹脂グロメットを介在しスクリューで固定するなどして、塗膜破壊部からの錆の発生の起点となることを防止しています。その他、従来は、ボデー面装着のエンブレム等は、その装着部位を確実にするため、差し込み内部拡張式の金属金具が使用されていましたが、ほとんどが両面テープによる接着に変化し、差し込み式を使用する場合でも中間に軟質樹脂グロメットを介在させ塗膜の破壊を防止しています。なお、軽量樹脂部品の装着では、樹脂クリップの使用により塗膜の破壊が生じない様留意しています。
⑦以上でも防錆上で不安が持たれる部位(主に閉断面部)には、防錆ワックス(蝋)を加熱噴射して防錆力をさらに補強しています。これは私の個人的観察ですが、日本車より欧州車の方が防錆ワックスの塗布量は多いと感じています。これは、使用過程において、ドアのモールやアウトサイドハンドルなどの隙間から流れ落ちる縦方向の染みが、欧州車に多いと感じることから推察している傾向なのです。
以上の様な防錆力の向上を図った国産車ですが、沿岸地区や北国の仕様車においては、驚くべき腐食の現状が新車から20年以内で生じている現実があるのです。以下の写真は、それら主に車体骨格部の極めて重要な構造部に破滅的な腐食を生じているという現実写真を羅列してみます。
なお、ふそう大型バスのフロントサスペンションロワアームを支持するセンターメンバ部については、新車登録後20年を越えてリコール処理が行われているものです。この部位は板厚が7.0mmもある厚板鋼板ですが、大型車のカチオンED塗装は乗用車に比べ20年後に始まったものであることや、水はけの悪いことなどが招いたものです。しかし、同メーカーに対する、それまでの行って来た不審から生じた罰でもあるのだとは私見なのです。








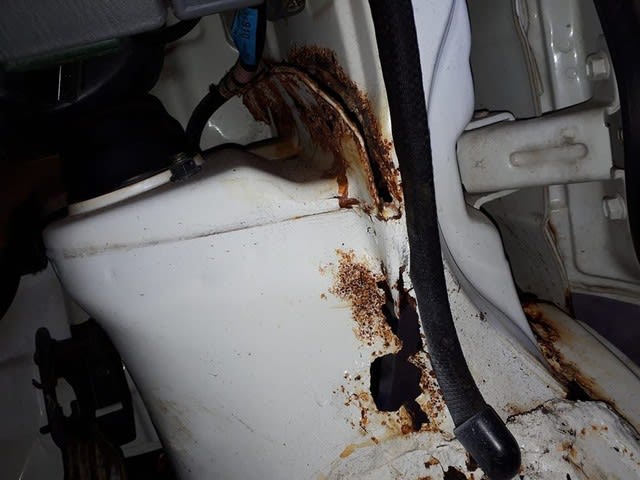


