現代車は何故ボンネット先端とその前パネルに見切りがあるのか
この表題の意味だが、旧来から一部車種にはボンネット前に鋼板もしくはアルミパネルがあるという車種は少ないながらあった。日本車だと初代のコスモとかルーチェ、輸入車だとアルファロメオやフェラーリモデナなどだ。これらは、現代車では、溶接もしくはボルトでパネル同士を結合し、パネル同士の切れ目を隠す場合はハンダ仕上げで仕上げるなどすれば、およそそのコスト高から量産車では使われることはなかろう。
一方、70年頃の米車などはGMのシボレーブランドとしてトランザム、フォーミラ400とかカマロなどの兄弟車で、通称フロントマスクパネルという前部をバンパー一体の樹脂製ソフトフェイシアで覆うデザインもあった。この流れは現在でも、ボンネットの前方傾斜ラインとフロントバンパーの一体化デザインとして、主にスポーツカーかスポーティ車では少なからずある。代々のRX7とかマツダロードスター、最近の86(BRZ)やフェラーリなどは、常套的なデザインだ。
さて、ここで述べるのは、そういう特段スポーツ車でもなく、ファミリーカーから高級車まで、ここ10年ばかりの世界の量販車でボンネット前に別パネルの同色パネルがあるが、実のところ実態は樹脂製のバンパー本体部品であり、様はパンパーを大型化しているに過ぎない構造の車両が極めて多くなっていることに気づかない者はいないだろう。

しかし、何故その様な構造が普及というか極当たり前ともいえる構造になったのか、その理由を問われ明確に答えられる者も少ないのではなかろうか。かくいう私自身も車両メーカーの設計者でもなく、量産コスト管理の担当者でもないのだが、車両メーカーのコスト管理とか対サプライヤーとの関係を知る時、ある程度の想像はできうることとして、今回の題材に取り上げてみたい。

端的云えば、この構造はコスト低減にあるのだが、それは一つはバンパーは樹脂金型で射出成型で一体で製造するのだが、バンパーを大型化することで、部品点数を減じることでのコスト低減が一つあるだろう。また、その組付けの工数についても、これはあくまで新車製造ラインにおいての問題だが、一体部品で大型化することで、その取り付けボルトなりクリップ数がバンパー単体として多少は増えたにしても、部品数が多い場合より取り付け工数は低減できるだろう。

それと、樹脂部品のバンパーとかインストルメントパネルなどは車両組み立てを行うアッセンブリー工場で製造されることは少なく、それぞれその種目毎の協力メーカー工場で作られ塗装まで施工されるのが一般的だろう。この場合、プレス部品の大物部品でも同様のことが生産技術として要求される場合がある様だが、大物部品になると、その移動(輸送)とか保管の際に、部品自体のある程度の剛性を確保してやらないと、移動や保管中に変型を生じて、アッセンブリーラインでの工数増を招きかねないという問題が想定できる。
これは、現在の車両ではサイドパネルがA、B、C(クオータ-)と各ピラーまで一体化プレスした大物部品となるが、単に車両組み立て後の剛性だけでなく、部品単体での剛性も考慮しないと、その保持とか移動時に変型を生じてしまうという問題がある。
このことはフロントバンパーでも同様で、例えばバンパーのグリル部分が分離していると、部品自体の剛性がないが故に、過大な変型を生じると、塗膜の割れや剥がれまでを生じかねないという問題がある。その点で、バンパー上部となるボンネット延長パネルに相当する部分を一体化させることで、バンパーフェイシア一体としての剛性を高め、その様な不具合を起こさないということもあるのだろうと想像している。
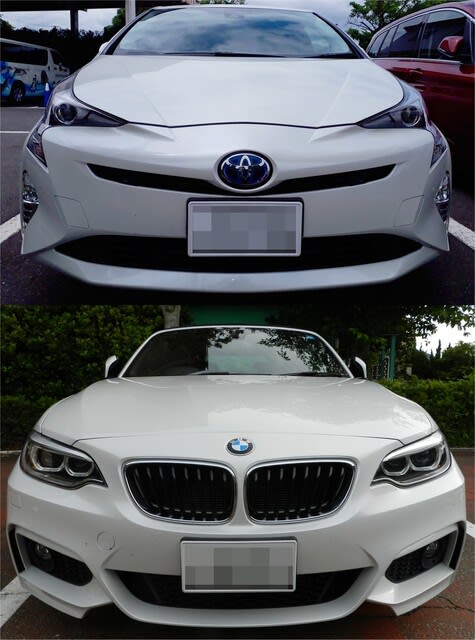
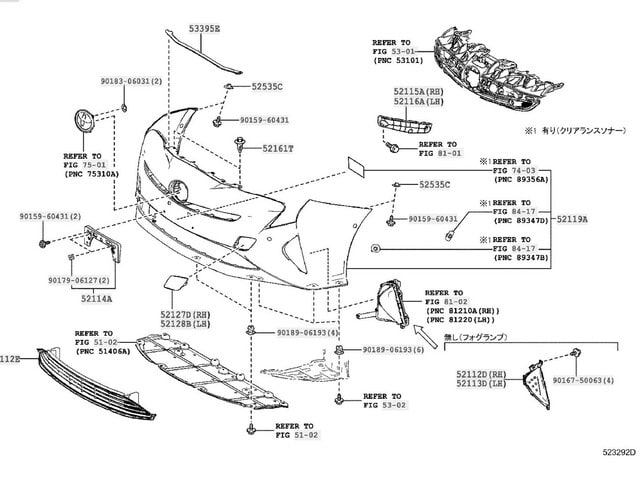
ここまでが、あくまで想像とはなるが車両メーカーの思いを代弁した理由だ。ところで、私自身の評価は、今回題材に上げたパネル間の見切りは、良いという認識はまったくない。その理由だが、特にボンネットからその前部分に連続する別パネル(パンパー)の間に傾斜が付けられたりしている場合は顕著になるが、ちょっとしたパネル間の高さとかチリの間隔の違いにより、不揃いが露呈しやすいと云うことがある。これは、プリウス30のボンネットが見る角度によっては、半開きになっている様に見えたり、添付写真のBMW(F30)の例の様に、ボンネットの前方視の中央部凸の極僅かなR差が顕在化するとか、気になる車両は結構目に付いてしまう。
私の場合は、単に論評者として記しているのだが、問題はこの損傷車を修復するBP業においては、かなり神経を使わざるを得ない部分になることだろう。得てして修理受託した車両が商用車とか古くやつれた車両ならともかく、比較的新しい車両となると、今回の様に新車でさえある程度欠点が目立つ部位まで、不具合として指摘を受けたり、受けるリスクを回避するため、その解消作業に時間を要するという問題を生むと想像できる。
ついでに話しを発展させると、日本ではBP系の作業工数に損保が出資して作った自研センターで策定した指数と云うのが何故か普及してしまったのだが、BP工場の中には現状の指数値はあまりに実情と比べ過小ではないかという意見も聞かれる。今や世界で最多車両製造しているのが日本車であるが、米国でも多数の米国工場製や日本からの輸出車が使用されている。そして、米国でのBP作業も行われている訳だが、米国の場合はBP作業の工数として最もメジャーとなってるのはミッチェル社の策定した工数なのだが、下記リンクのとおり今年6月に指数とミッチェル工数の比較を同じプリウス30で比較検証してみたところ、米ミッチェル工数は指数の平均2倍の値であることが判って驚いている。
指数の疑問 その9【米ミッチェル工数との対比考察】 2022-06-09
https://blog.goo.ne.jp/wiseman410/e/104b2b3dff5caa97b250efc1580aaf76
この指数について、現在の自研センターに説明を求めると、最終的な要旨として概ね次の様な言葉を云う。「指数はあくまで自研センター独自の考えで策定したもので、これを使用する使用しないは工場が決めるべきことで自研センターとして強要できる立場にない。」一方、保険金を支払う損保の説明はかなり違っており、概ね次の様な要旨の意見を宣う。「指数は私共会社として全幅の信頼を置いている自研センターで科学的に求めた値であり、概ね全国の多くの工場に理解され使用して戴いており、それが飲めないのなら修理費は協定できない。」
と云う様な現状を知るのだが、損保調査員に指数のことを聞いても、疑問は解けないし、自研センターに聞いても先の文言を云われるに過ぎないのだ。実のところ、私は元損保調査員であり、ある時期まで自研センターの云い分は現在と異なっており、当時は指数の中身に踏み込んで説明をし始めた時期があったことを回想するのだ。それは、指数策定は全車種同一作業を実測している訳でなく、世界的に眺めても現在自研センターで云う基表方式に準じた手法が取られている。そもそもそんな現車の作業観測で確かめ様としたら、1台につき10回は同一作業を繰り返し、作業時間として平準化もしくは安定化した時間を把握しなければならず、到底人物金と効果の点で間尺に合わないだろう。
話しを戻すが、ある時期まで自研センターは各損保の本社所在員に対し、基表の一部具体的な数値までを公開しつつ、その策定原理を公開しつつあった時期があるのだ。それが、私は損保を離れる以前、ある時期からそういう動きは一切止まってしまったことを回想するのだ。このある時期とは、損保が独禁法で公取から注意勧告を受けた時期に符合する。この公取の注意勧告は、あくまで対応単価(これもそれ以前は指数対応単価と呼んでいたが指数が除かれた表記となった)についてだったのだが、自研センターとしては、指数値そのものが独禁法に抵触すると云われかねない恐れを抱いたと云うところだろうと想像している。つまり、以後、指数については対外的には純科学的に策定しているとは云いながら、具体論となると、それは自研センターの知的資産で対外的に公表できないなどと述べる様になったのだ。そして、先に述べた様に、自研センターの云い分としては使い使わないは自由と言い放つが、それを実運用する損保は、使うことをほぼ強要に近い形で要求しつつ、中身を聞いても答えられないと云う実態にあるのだ。
私は思う。修理料金は指数値×対応単価で算出するからには、対応単価だけでなく指数値についても、その使用を要求する限りにおいては、その中身の説明責任は自研センターもしくは運用する損保に生じるものと考えているのだが・・・。
この表題の意味だが、旧来から一部車種にはボンネット前に鋼板もしくはアルミパネルがあるという車種は少ないながらあった。日本車だと初代のコスモとかルーチェ、輸入車だとアルファロメオやフェラーリモデナなどだ。これらは、現代車では、溶接もしくはボルトでパネル同士を結合し、パネル同士の切れ目を隠す場合はハンダ仕上げで仕上げるなどすれば、およそそのコスト高から量産車では使われることはなかろう。
一方、70年頃の米車などはGMのシボレーブランドとしてトランザム、フォーミラ400とかカマロなどの兄弟車で、通称フロントマスクパネルという前部をバンパー一体の樹脂製ソフトフェイシアで覆うデザインもあった。この流れは現在でも、ボンネットの前方傾斜ラインとフロントバンパーの一体化デザインとして、主にスポーツカーかスポーティ車では少なからずある。代々のRX7とかマツダロードスター、最近の86(BRZ)やフェラーリなどは、常套的なデザインだ。
さて、ここで述べるのは、そういう特段スポーツ車でもなく、ファミリーカーから高級車まで、ここ10年ばかりの世界の量販車でボンネット前に別パネルの同色パネルがあるが、実のところ実態は樹脂製のバンパー本体部品であり、様はパンパーを大型化しているに過ぎない構造の車両が極めて多くなっていることに気づかない者はいないだろう。

しかし、何故その様な構造が普及というか極当たり前ともいえる構造になったのか、その理由を問われ明確に答えられる者も少ないのではなかろうか。かくいう私自身も車両メーカーの設計者でもなく、量産コスト管理の担当者でもないのだが、車両メーカーのコスト管理とか対サプライヤーとの関係を知る時、ある程度の想像はできうることとして、今回の題材に取り上げてみたい。

端的云えば、この構造はコスト低減にあるのだが、それは一つはバンパーは樹脂金型で射出成型で一体で製造するのだが、バンパーを大型化することで、部品点数を減じることでのコスト低減が一つあるだろう。また、その組付けの工数についても、これはあくまで新車製造ラインにおいての問題だが、一体部品で大型化することで、その取り付けボルトなりクリップ数がバンパー単体として多少は増えたにしても、部品数が多い場合より取り付け工数は低減できるだろう。

それと、樹脂部品のバンパーとかインストルメントパネルなどは車両組み立てを行うアッセンブリー工場で製造されることは少なく、それぞれその種目毎の協力メーカー工場で作られ塗装まで施工されるのが一般的だろう。この場合、プレス部品の大物部品でも同様のことが生産技術として要求される場合がある様だが、大物部品になると、その移動(輸送)とか保管の際に、部品自体のある程度の剛性を確保してやらないと、移動や保管中に変型を生じて、アッセンブリーラインでの工数増を招きかねないという問題が想定できる。
これは、現在の車両ではサイドパネルがA、B、C(クオータ-)と各ピラーまで一体化プレスした大物部品となるが、単に車両組み立て後の剛性だけでなく、部品単体での剛性も考慮しないと、その保持とか移動時に変型を生じてしまうという問題がある。
このことはフロントバンパーでも同様で、例えばバンパーのグリル部分が分離していると、部品自体の剛性がないが故に、過大な変型を生じると、塗膜の割れや剥がれまでを生じかねないという問題がある。その点で、バンパー上部となるボンネット延長パネルに相当する部分を一体化させることで、バンパーフェイシア一体としての剛性を高め、その様な不具合を起こさないということもあるのだろうと想像している。
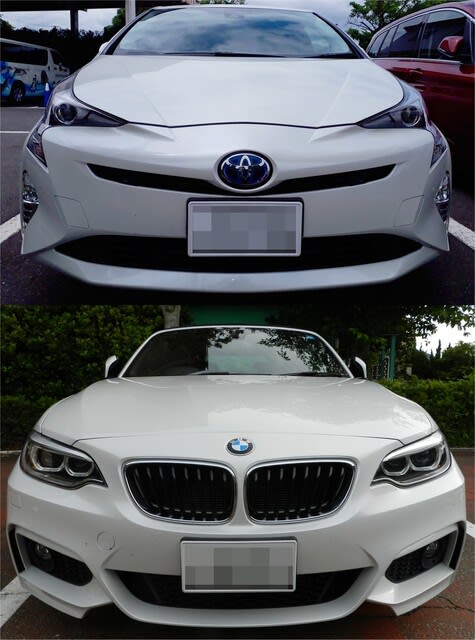
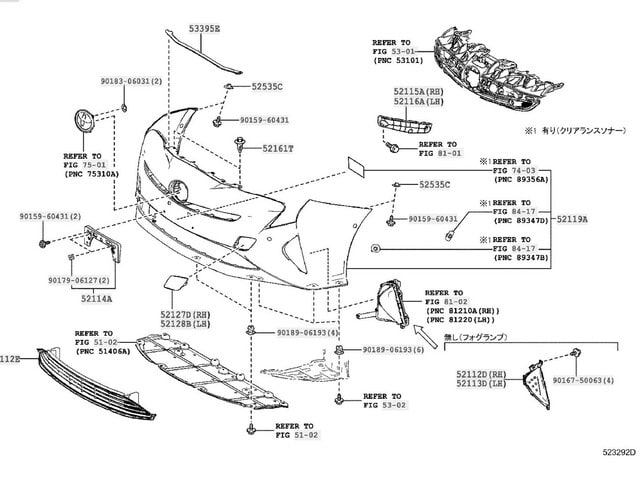
ここまでが、あくまで想像とはなるが車両メーカーの思いを代弁した理由だ。ところで、私自身の評価は、今回題材に上げたパネル間の見切りは、良いという認識はまったくない。その理由だが、特にボンネットからその前部分に連続する別パネル(パンパー)の間に傾斜が付けられたりしている場合は顕著になるが、ちょっとしたパネル間の高さとかチリの間隔の違いにより、不揃いが露呈しやすいと云うことがある。これは、プリウス30のボンネットが見る角度によっては、半開きになっている様に見えたり、添付写真のBMW(F30)の例の様に、ボンネットの前方視の中央部凸の極僅かなR差が顕在化するとか、気になる車両は結構目に付いてしまう。
私の場合は、単に論評者として記しているのだが、問題はこの損傷車を修復するBP業においては、かなり神経を使わざるを得ない部分になることだろう。得てして修理受託した車両が商用車とか古くやつれた車両ならともかく、比較的新しい車両となると、今回の様に新車でさえある程度欠点が目立つ部位まで、不具合として指摘を受けたり、受けるリスクを回避するため、その解消作業に時間を要するという問題を生むと想像できる。
ついでに話しを発展させると、日本ではBP系の作業工数に損保が出資して作った自研センターで策定した指数と云うのが何故か普及してしまったのだが、BP工場の中には現状の指数値はあまりに実情と比べ過小ではないかという意見も聞かれる。今や世界で最多車両製造しているのが日本車であるが、米国でも多数の米国工場製や日本からの輸出車が使用されている。そして、米国でのBP作業も行われている訳だが、米国の場合はBP作業の工数として最もメジャーとなってるのはミッチェル社の策定した工数なのだが、下記リンクのとおり今年6月に指数とミッチェル工数の比較を同じプリウス30で比較検証してみたところ、米ミッチェル工数は指数の平均2倍の値であることが判って驚いている。
指数の疑問 その9【米ミッチェル工数との対比考察】 2022-06-09
https://blog.goo.ne.jp/wiseman410/e/104b2b3dff5caa97b250efc1580aaf76
この指数について、現在の自研センターに説明を求めると、最終的な要旨として概ね次の様な言葉を云う。「指数はあくまで自研センター独自の考えで策定したもので、これを使用する使用しないは工場が決めるべきことで自研センターとして強要できる立場にない。」一方、保険金を支払う損保の説明はかなり違っており、概ね次の様な要旨の意見を宣う。「指数は私共会社として全幅の信頼を置いている自研センターで科学的に求めた値であり、概ね全国の多くの工場に理解され使用して戴いており、それが飲めないのなら修理費は協定できない。」
と云う様な現状を知るのだが、損保調査員に指数のことを聞いても、疑問は解けないし、自研センターに聞いても先の文言を云われるに過ぎないのだ。実のところ、私は元損保調査員であり、ある時期まで自研センターの云い分は現在と異なっており、当時は指数の中身に踏み込んで説明をし始めた時期があったことを回想するのだ。それは、指数策定は全車種同一作業を実測している訳でなく、世界的に眺めても現在自研センターで云う基表方式に準じた手法が取られている。そもそもそんな現車の作業観測で確かめ様としたら、1台につき10回は同一作業を繰り返し、作業時間として平準化もしくは安定化した時間を把握しなければならず、到底人物金と効果の点で間尺に合わないだろう。
話しを戻すが、ある時期まで自研センターは各損保の本社所在員に対し、基表の一部具体的な数値までを公開しつつ、その策定原理を公開しつつあった時期があるのだ。それが、私は損保を離れる以前、ある時期からそういう動きは一切止まってしまったことを回想するのだ。このある時期とは、損保が独禁法で公取から注意勧告を受けた時期に符合する。この公取の注意勧告は、あくまで対応単価(これもそれ以前は指数対応単価と呼んでいたが指数が除かれた表記となった)についてだったのだが、自研センターとしては、指数値そのものが独禁法に抵触すると云われかねない恐れを抱いたと云うところだろうと想像している。つまり、以後、指数については対外的には純科学的に策定しているとは云いながら、具体論となると、それは自研センターの知的資産で対外的に公表できないなどと述べる様になったのだ。そして、先に述べた様に、自研センターの云い分としては使い使わないは自由と言い放つが、それを実運用する損保は、使うことをほぼ強要に近い形で要求しつつ、中身を聞いても答えられないと云う実態にあるのだ。
私は思う。修理料金は指数値×対応単価で算出するからには、対応単価だけでなく指数値についても、その使用を要求する限りにおいては、その中身の説明責任は自研センターもしくは運用する損保に生じるものと考えているのだが・・・。