時々、クルマのメカ解説の記事で「クローズドデッキとオープンデッキ」とか「サイアミーズ」なるワードが出てきますが、多分クルマのメカに精通していたり整備に携わっている方ならご存じの内容でしょう。そうはいうものの、案外知らないというウンチク知らずの方向けに、関連情報も含めて知ったかぶりの解説を記してみます。ただし、かなりの私見(と偏見)を含むので、真偽は自らが確かめながら理解して戴けたらと思います。
さて、クローズドデッキとオープンデッキというワードはエンジンのシリンダーブロック関連として出てくるものです。その違いは写真の1がクローズドデッキで、写真2がオープンデッキであり、即座に判るでしょう。そもそも、昔はオープンデッキなるものは、余程特殊なエンジン(センチュリーの4V型とか)にしか使われなかったもので、ほとんど総てのエンジンがクローズドデッキだったものです。
それは何故か?ですが、総てのシリンダーブロックは砂型鋳造(鋳鉄)で作られていたからなのです。そもそも鋳造とは溶かした金属を鋳型の隙間(キャビティと呼ぶ)に流し込み成型する技法で、奈良の大仏も青銅を鋳造で作られたと知ります。ただし、あんな大きな大仏を一気に鋳造できる訳もなく、粘度で覆った鋳型を、段々に積み上げて形作ったそうです。エンジンの鋳造は、砂型鋳造と呼ばれる砂に樹脂を混ぜて固めた鋳型(外型と中子と呼ばれる内部の鋳型で構成)し、その隙間に溶けた金属を流し込む(もしくは軽度に圧入するか、キャビティ内を真空にして吸い込む)ことで製品を作ります。
昔のエンジンは小型車でも、鋳鉄で作られましたから、鋳型を鋼で作ると鋳型自身が溶けてしまうので成立しません。そこで形が自由になる砂が使われたということです。今でも、大型エンジンとか、ディーゼルエンジンのシリンダーブロックは、主に鋳鉄で作られる事例が多く、従ってクローズドデッキとなるのです。なお、砂型鋳造では、流し込んだ鋳鉄が冷えて固まった後、周辺の鋳型を壊すことや、適宜の振動を与えることで、内部に設置された中子(なかご)としての鋳型を抜き取ります。その抜き取りのために、適する位置にタイトホールが設置され、機械加工後にタイトプラグと呼ぶ鋼板製のフタが嵌め込まれて水密、油密を保つ様になされます。長年の使用において冷却水の管理が悪かったり、寒冷時の凍結でタイトプラグが外れたりして、水漏れを起こすというトラブルがあるのはご存じの通りです。
さて、比較的近代になって、鋳鉄でなくアルミ合金や一部にはマグネシウム合金、亜鉛合金などの鋼に比べれば低融点の金属が軽量化などの目的で使用される様になって来ました。こうなると、砂型で型を毎回作るより、鋼製の鋳型(ダイと呼ぶ)で作って何度も同じ型が繰り返し仕える様にしたのがダイカストなのです。そこで、ダイカスト化により量産性が可能なシリンダーブロック等までが、主にアルミ合金で作るのが主流になったという訳です。それでも、アルミのシリンダーヘッドなどは、写真3に示す事例の通り吸排気ポートや冷却水通路が複雑な関係で、複雑な中子が必要になることから、外面のみ金属製ダイで、中子は砂型としての鋳造で作っているのが現状の様です。それと、関連して現在はやや少なくなりましたが、一時増えた、ヘッド上にカムホルダーを積層する方式も、ヘッド本体は砂型鋳造で、カムホルダーはダイキャスト化することで生産性を上げたと考えています。
ダイカストでは、雄型と雌型(固定型と可動型と呼ばれる)を鋼で精密に作成し、その間のキャビティ(隙間)に高圧で溶けた金属を注入することで、高品質(高精度)な製品が短時間に作られるます。ただし、高精度なダイを作るのにコストを要しますし、あまりにも大きな製品には向かないという欠点があります。なお、ダイカストには、ダイカストマシンという専用機械が使用されます。その概観は、参考写真の様なものですが、固定型と可動型を取り付けるダイプレートというのがあり、可動型を取り付けたダイプレートは可動(スライド)して、強力(シリンダーブロック用としては最大クラスとして3~4千トン程)で可動型を固定型に押し付け密着させます。その状態で、固定型側にあるプランジャー機構で溶けた金属(アルミなら700℃、亜鉛なら400℃程)で強力に圧入します。溶融金属圧入後、設定時間(製品の大きさにもよるが1~数秒程)で可動型を開き、製品を取り出します。なお、ダイキャストマシンの写真には写っていませんが、マシンに隣接して溶融金属を一定温度で溶解させる熔解炉があり、そこからひしゃく(ラドルと呼ぶ)で必要注入量を汲み取って、プランジャーに供給します。これら一連の作業は、シーケンサーもしくはコンピューターにより様々なパラメーターの設定と共に自動化されています。
というのがダイキャストの概要ですが、ブロックがオープンデッキになっている理由が判るでしょう。つまり、クローズドだと離型時に型が抜き取れないことになります。なお、製品の一部構造には、袋構造とかで、中子が必要な場合がありますが、可動中子という機構で解決しています、これは、可動型が固定型に接近するに従って、可動中子が傾斜ピンとか別途の油圧機構でダイの内部を移動することで中子の働きを持たせています。
なお、最初に記した「サイアミーズ」というワードですが、直訳すると「シャム」(現在のタイ国)の意味ですが、シャム双生児という語源から「くっついている」という意味から呼ばれたものと推察します。つまり、4気筒なら4シリンダー分が連結されて形成されるということです。このサイアミーズ構造は、シリンダーの剛性としては良方向となりますが、シリンダー間の放冷が悪化するという負の部分も持ちます。それと、サイアミーズにしたところでオープンデッキそのものが、クローズドデッキと比べると、ヘッドとの熱変形などによる剛性は悪化する方向となるでしょう。つまり、オーバーヒートなどによるガスケット抜けを生じ易い構造であるとは私見です。
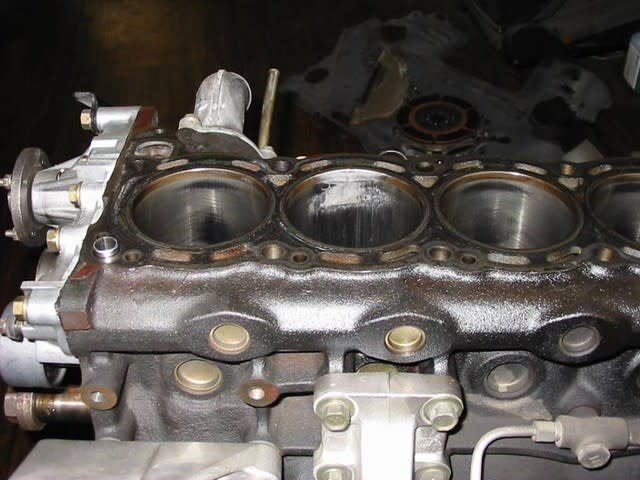


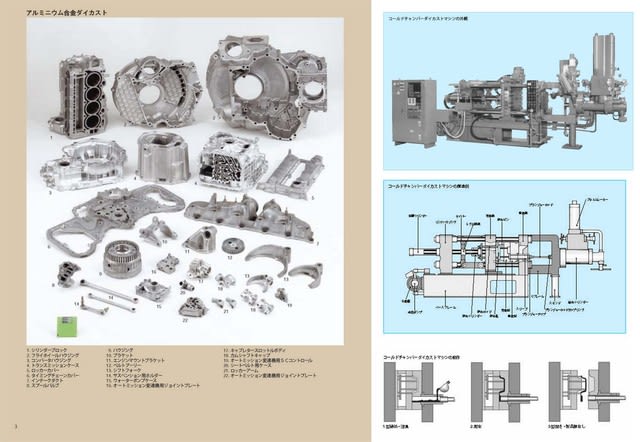
追記
2つほど関連することを記してみます。
1つは、最近のダイカストによるオープンデッキシリンダーブロックですが、ほとんどアルミ合金製ですが、シリンダー壁面はアルミでは耐久製に難がありますので、薄肉鋼製スリーブもしくは鋼系のメッキもしくは溶射処理とか、ポルシェで云うニカシル(ニッケル・シリコンのメッキ処理)が施されます。また、サイアミーズシリンダーのボア間隔は5mmに満たない程に狭い場合も珍しくありません。ということは、ボアアップは到底不可能ですし、加給圧上げとか高回転化による出力向上への余地は昔のエンジンより相当な制限を受けるということを感じます。
2つめですが、その昔(たぶん昭和30年頃まで)行われた、鋳造後の製品を数ヶ月から1年程も、錆の出るまま放置する「枯らし」(シーズニング)という期間を経て、その後の機械加工に入ったという話しです。これは、鋳造時に生じた熱による内部の残留応力を抜くために放置し、機械加工後の変形を防ぐ目的であったとのことです。現在では、この様な長時間の枯らしは行われませんが、それは設計時点で、肉厚をなるべく一定にするとか残留応力を生じない様に留意している様です。ついでに、鋼の熱処理に一つとして「焼鈍」というのがあります。これも、主に鋼製厚板部品で溶接成型される、例えば原子炉圧力容器(厚さ15cm、総重量300トン)みたいな巨大なものも、「焼鈍」処理により残留応力を抜く作業を経ているそうです。
さて、クローズドデッキとオープンデッキというワードはエンジンのシリンダーブロック関連として出てくるものです。その違いは写真の1がクローズドデッキで、写真2がオープンデッキであり、即座に判るでしょう。そもそも、昔はオープンデッキなるものは、余程特殊なエンジン(センチュリーの4V型とか)にしか使われなかったもので、ほとんど総てのエンジンがクローズドデッキだったものです。
それは何故か?ですが、総てのシリンダーブロックは砂型鋳造(鋳鉄)で作られていたからなのです。そもそも鋳造とは溶かした金属を鋳型の隙間(キャビティと呼ぶ)に流し込み成型する技法で、奈良の大仏も青銅を鋳造で作られたと知ります。ただし、あんな大きな大仏を一気に鋳造できる訳もなく、粘度で覆った鋳型を、段々に積み上げて形作ったそうです。エンジンの鋳造は、砂型鋳造と呼ばれる砂に樹脂を混ぜて固めた鋳型(外型と中子と呼ばれる内部の鋳型で構成)し、その隙間に溶けた金属を流し込む(もしくは軽度に圧入するか、キャビティ内を真空にして吸い込む)ことで製品を作ります。
昔のエンジンは小型車でも、鋳鉄で作られましたから、鋳型を鋼で作ると鋳型自身が溶けてしまうので成立しません。そこで形が自由になる砂が使われたということです。今でも、大型エンジンとか、ディーゼルエンジンのシリンダーブロックは、主に鋳鉄で作られる事例が多く、従ってクローズドデッキとなるのです。なお、砂型鋳造では、流し込んだ鋳鉄が冷えて固まった後、周辺の鋳型を壊すことや、適宜の振動を与えることで、内部に設置された中子(なかご)としての鋳型を抜き取ります。その抜き取りのために、適する位置にタイトホールが設置され、機械加工後にタイトプラグと呼ぶ鋼板製のフタが嵌め込まれて水密、油密を保つ様になされます。長年の使用において冷却水の管理が悪かったり、寒冷時の凍結でタイトプラグが外れたりして、水漏れを起こすというトラブルがあるのはご存じの通りです。
さて、比較的近代になって、鋳鉄でなくアルミ合金や一部にはマグネシウム合金、亜鉛合金などの鋼に比べれば低融点の金属が軽量化などの目的で使用される様になって来ました。こうなると、砂型で型を毎回作るより、鋼製の鋳型(ダイと呼ぶ)で作って何度も同じ型が繰り返し仕える様にしたのがダイカストなのです。そこで、ダイカスト化により量産性が可能なシリンダーブロック等までが、主にアルミ合金で作るのが主流になったという訳です。それでも、アルミのシリンダーヘッドなどは、写真3に示す事例の通り吸排気ポートや冷却水通路が複雑な関係で、複雑な中子が必要になることから、外面のみ金属製ダイで、中子は砂型としての鋳造で作っているのが現状の様です。それと、関連して現在はやや少なくなりましたが、一時増えた、ヘッド上にカムホルダーを積層する方式も、ヘッド本体は砂型鋳造で、カムホルダーはダイキャスト化することで生産性を上げたと考えています。
ダイカストでは、雄型と雌型(固定型と可動型と呼ばれる)を鋼で精密に作成し、その間のキャビティ(隙間)に高圧で溶けた金属を注入することで、高品質(高精度)な製品が短時間に作られるます。ただし、高精度なダイを作るのにコストを要しますし、あまりにも大きな製品には向かないという欠点があります。なお、ダイカストには、ダイカストマシンという専用機械が使用されます。その概観は、参考写真の様なものですが、固定型と可動型を取り付けるダイプレートというのがあり、可動型を取り付けたダイプレートは可動(スライド)して、強力(シリンダーブロック用としては最大クラスとして3~4千トン程)で可動型を固定型に押し付け密着させます。その状態で、固定型側にあるプランジャー機構で溶けた金属(アルミなら700℃、亜鉛なら400℃程)で強力に圧入します。溶融金属圧入後、設定時間(製品の大きさにもよるが1~数秒程)で可動型を開き、製品を取り出します。なお、ダイキャストマシンの写真には写っていませんが、マシンに隣接して溶融金属を一定温度で溶解させる熔解炉があり、そこからひしゃく(ラドルと呼ぶ)で必要注入量を汲み取って、プランジャーに供給します。これら一連の作業は、シーケンサーもしくはコンピューターにより様々なパラメーターの設定と共に自動化されています。
というのがダイキャストの概要ですが、ブロックがオープンデッキになっている理由が判るでしょう。つまり、クローズドだと離型時に型が抜き取れないことになります。なお、製品の一部構造には、袋構造とかで、中子が必要な場合がありますが、可動中子という機構で解決しています、これは、可動型が固定型に接近するに従って、可動中子が傾斜ピンとか別途の油圧機構でダイの内部を移動することで中子の働きを持たせています。
なお、最初に記した「サイアミーズ」というワードですが、直訳すると「シャム」(現在のタイ国)の意味ですが、シャム双生児という語源から「くっついている」という意味から呼ばれたものと推察します。つまり、4気筒なら4シリンダー分が連結されて形成されるということです。このサイアミーズ構造は、シリンダーの剛性としては良方向となりますが、シリンダー間の放冷が悪化するという負の部分も持ちます。それと、サイアミーズにしたところでオープンデッキそのものが、クローズドデッキと比べると、ヘッドとの熱変形などによる剛性は悪化する方向となるでしょう。つまり、オーバーヒートなどによるガスケット抜けを生じ易い構造であるとは私見です。
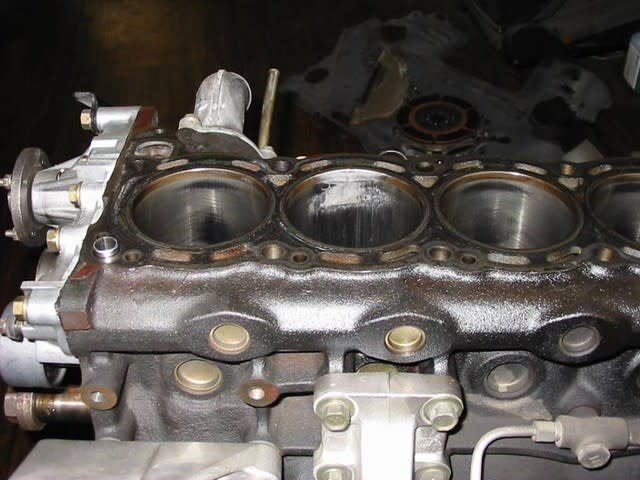


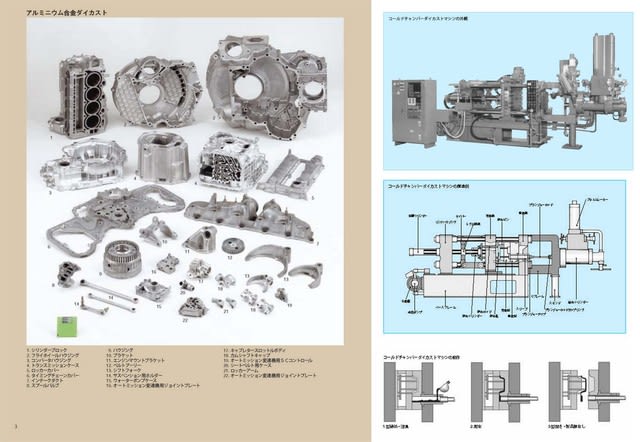
追記
2つほど関連することを記してみます。
1つは、最近のダイカストによるオープンデッキシリンダーブロックですが、ほとんどアルミ合金製ですが、シリンダー壁面はアルミでは耐久製に難がありますので、薄肉鋼製スリーブもしくは鋼系のメッキもしくは溶射処理とか、ポルシェで云うニカシル(ニッケル・シリコンのメッキ処理)が施されます。また、サイアミーズシリンダーのボア間隔は5mmに満たない程に狭い場合も珍しくありません。ということは、ボアアップは到底不可能ですし、加給圧上げとか高回転化による出力向上への余地は昔のエンジンより相当な制限を受けるということを感じます。
2つめですが、その昔(たぶん昭和30年頃まで)行われた、鋳造後の製品を数ヶ月から1年程も、錆の出るまま放置する「枯らし」(シーズニング)という期間を経て、その後の機械加工に入ったという話しです。これは、鋳造時に生じた熱による内部の残留応力を抜くために放置し、機械加工後の変形を防ぐ目的であったとのことです。現在では、この様な長時間の枯らしは行われませんが、それは設計時点で、肉厚をなるべく一定にするとか残留応力を生じない様に留意している様です。ついでに、鋼の熱処理に一つとして「焼鈍」というのがあります。これも、主に鋼製厚板部品で溶接成型される、例えば原子炉圧力容器(厚さ15cm、総重量300トン)みたいな巨大なものも、「焼鈍」処理により残留応力を抜く作業を経ているそうです。