車体軽量化技術の動向
車体軽量化とは、同じ出力とエネルギー効率なら、軽い方が加速も良く制動吸収ネネルギーも良く、燃費(電費)も良いと云うことで軽いに超したことはないのだが、クルマはどんどん重くなる傾向を示してる。その理由には種々あるのだろうが、ボデーサイズの拡大、衝突安全性能の改善、贅沢装備の充実と云ったところであろうか。これからEV車が何処まで増えるか断定できないところもあるが、バッテリー重量というのが、従来のエンジンに代わって、最重量部品となることは間違いない様に思える。
そんな車両の重量増大の傾向はあるが、それでも軽量化の努力は続いているのだが、軽量化とは極論すれば、鋼(比重7.8程)に比べアルミ(比重2.7程)や樹脂(0.9-1.5程)という比重の軽い素材に置き換えるという思考だ。
ただし、アルミにしても簡易な説明とすれば同板厚のアルミは比重は1/3程だが、変型のし易さ、つまり剛性指標となるヤング率も1/3となるので、製品重量としてはそれなりに板厚を増すので2/3程の軽量化しかできない。樹脂に至っては、比重は小さいが、比強度は著しく小さく、一般的には強度部材には使えない。ただし、カーボンファイバーなどは同断面の鋼より10倍程の比強度を得るのだが、ファイバーだけで形状を維持することができずエポキシ樹脂との複合材として強度部材として使用できるが、コストが飛び上がるのと、樹脂の特性上から耐熱温度の限界が低い。
総論として軽量化として、アルミや樹脂の使用量は増しているが、アルミは素材原価としては上がるが、製法として板材でなく、ダイキャストを利用できるとなれば、パーツ点数と製造サイクルタイムの著しい低減によりコスト圧縮に向く。ただし、鋼板のプレス金型、ダイキャストの金型、樹脂射出成型の金型と何れにしても金型を使用するが、素材により金型コストも変わるが、何れにしても大物製品の金型コストは相当高額になるので、少量製品だと金型コストを吸収できない。
今回、図書館で借りだした「自動車軽量化の生産技術」という技術書だが、自動車の整備とか修理には直接関わらないが、こういう内容を知っているのと知らないのでは、ものの見方が変わると云うか視野が広がるという点から、拙人として感心を持った部位のみを抽出して記してみたい。
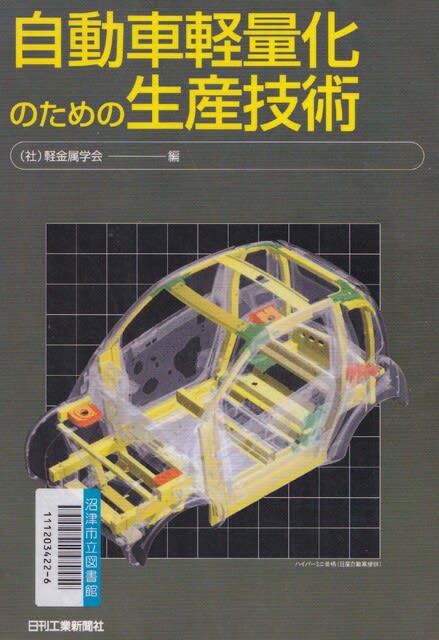
アルミボデーだが図に示す資料は90年から2000年頃までど若干古いが、90年のホンダNSXは初の量産オールアルミボデー車だ。ここで、気が付くこととして、材料構成比として、板材、押出材(引抜材も同意語)、鋳造材と三区分されているが、押出材とは同形状断面の連続体部位のみ成立する鍛造材に近い性能を持つが板材の一種と考えて良かろう。また、鋳造材とはダイキャストも鋳造の製法の一つと考えれば、ダイキャスト材と考えて良かろう。こういう点で、NSXは総て板材だったことが判る。

それが、以後の車両では、板材よりダイキャスト材が増加しているのが判る資料だ。現在でも、オールアルミボデー車は一部車両に残るが、やはり主流は鋼板ボデーで、アルミ材を使用するのは蓋物パーツとして呼ばれる、ボンネットとかフロントフェンダーやドアなどのボルトオンパーツに多い。一時、ベンツCLなどのリヤフェンダーとかルーフにアルミパネルが使用されたことがあったが、鋼板基本骨格にアルミ外板を強度負担パネルとして装着することは、溶接不可であり、接着剤とSPR(セルフピアッシングリベット)であり、日本メーカーならマスプロダクションの自動化に馴染まない絶体採用しない方式だろう。
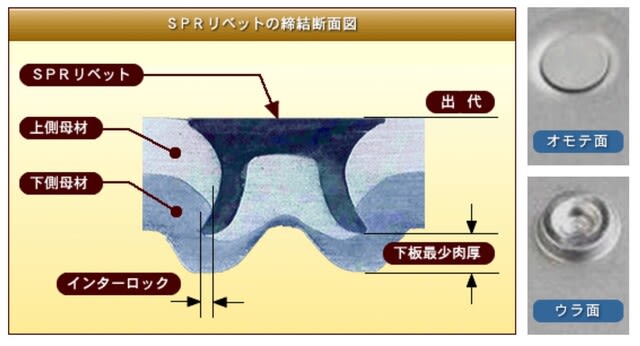
NSX以降でダイキャスト材が増えつつ板材がとして減ってはいるのだが、押出材は増えているという理由だが、ダイキャスト材の利用部位とは、サスペンションアームが装着される部位とか、押出材同士が集合する部位となる。こういう部位は、局部剛性が要求されたり、ラーメーン構造体(剛結構造体)として結合剛性が要求されるので、鋼板ボデーではスティフナーとかパッチと呼ばれる局部重ね補強構造が要求されたり、二重三重の重ね構造が要求されるが、ダイキャストだと形状の各部で要求板厚が自由自在になるとう利点がある。
このことは、現代車においても、基本鋼板ボデーだがフロントストラットタワー部のみアルミダイキャスを採用しているのは国産車でも、フロントアパーマウント式ダブルウッシュボーンサスの高級志向の車両に多くを見る。この場合、タワー下部のフロントサイドフレームまでをアルミにしているのは量産車ではBMW程度で、他はサイドフレームは鋼板製だ。
それと、現代車は、フロントバンパーは樹脂製なのは90年頃車と変わらないが、ぞの上部に位置してフード前のパネルとなる外装パネルまでフロントバンパーと一体成型の大型パネルになっているのは世界共通の構造的な傾向となった。フロントグリルは装着されるが、その取り付け相手部位は、このフロントエンドパネルとなる。こうして、樹脂フロントバンパーはフロントエンドパネルとして実質大型化している。
なお、この本とは別資料からの引用だが、テスラの思考を表すものとして、モデルYに途中から採用される様になっている前後骨格を丸ごとダイキャスト化した構造車が出て来ている。これは、従来の板材なら、優に100点を超える個別パーツを溶接なしに1ピース化できる構造で、マスプロダクション化により数分単位のサイクルタイムで成型でき、車体中央のキャビン部との接合も短時間かつ合理的だ。ただし、骨格損傷とか変型(というか素材特性上クラックとか割損となりそうだ)が生じると、極めて高額な修理費となり、事実上修理しないという事態になりそうだ。
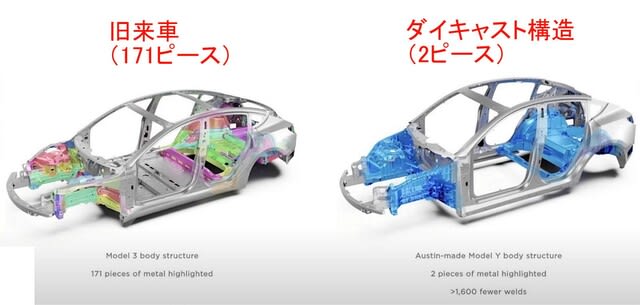
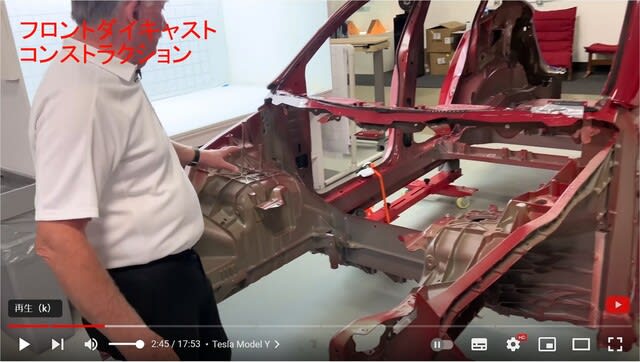
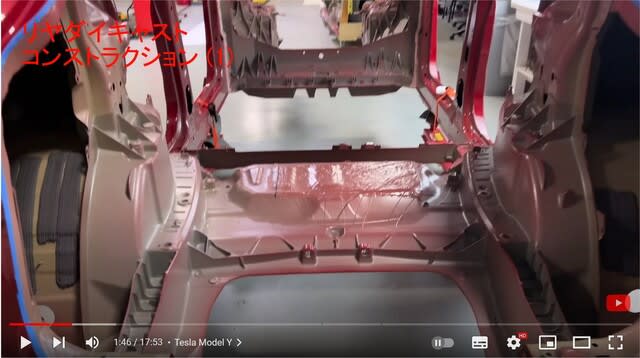
もう一つの話題として、フォーミングという形容詞があるが、日本語に直訳すると成型となる。このフォーミングの中にプレス成型とかダイキャストも含まれるのだが、プレス成型にしてもダイキャスや射出成型は雄型と雌型(固定型と可動型)とのセットで成立するが、固定型の単体で、その内側から高温気体を圧送するブロー成型という手法が、樹脂燃料タンクとか吸気マニホールドなどに使用される様になっている。
一方、高温気体でなく高圧液体を加圧することで、閉断面円柱を金型の断面に押し付け成型するチューブフォーミングという技法がエンジンメンバーなどに採用され出している。これは、従来、上下一対のプレス成型品を溶接で作っていたのを、溶接を少なくし、板厚も一定で寸法形状も優れるという工法だ。ここの参照図で「三五提供」と記してあるが、マフラー屋がサスペンションクロスメンバーを作るという技術の応用という点で気付きを思う。
車体軽量化とは、同じ出力とエネルギー効率なら、軽い方が加速も良く制動吸収ネネルギーも良く、燃費(電費)も良いと云うことで軽いに超したことはないのだが、クルマはどんどん重くなる傾向を示してる。その理由には種々あるのだろうが、ボデーサイズの拡大、衝突安全性能の改善、贅沢装備の充実と云ったところであろうか。これからEV車が何処まで増えるか断定できないところもあるが、バッテリー重量というのが、従来のエンジンに代わって、最重量部品となることは間違いない様に思える。
そんな車両の重量増大の傾向はあるが、それでも軽量化の努力は続いているのだが、軽量化とは極論すれば、鋼(比重7.8程)に比べアルミ(比重2.7程)や樹脂(0.9-1.5程)という比重の軽い素材に置き換えるという思考だ。
ただし、アルミにしても簡易な説明とすれば同板厚のアルミは比重は1/3程だが、変型のし易さ、つまり剛性指標となるヤング率も1/3となるので、製品重量としてはそれなりに板厚を増すので2/3程の軽量化しかできない。樹脂に至っては、比重は小さいが、比強度は著しく小さく、一般的には強度部材には使えない。ただし、カーボンファイバーなどは同断面の鋼より10倍程の比強度を得るのだが、ファイバーだけで形状を維持することができずエポキシ樹脂との複合材として強度部材として使用できるが、コストが飛び上がるのと、樹脂の特性上から耐熱温度の限界が低い。
総論として軽量化として、アルミや樹脂の使用量は増しているが、アルミは素材原価としては上がるが、製法として板材でなく、ダイキャストを利用できるとなれば、パーツ点数と製造サイクルタイムの著しい低減によりコスト圧縮に向く。ただし、鋼板のプレス金型、ダイキャストの金型、樹脂射出成型の金型と何れにしても金型を使用するが、素材により金型コストも変わるが、何れにしても大物製品の金型コストは相当高額になるので、少量製品だと金型コストを吸収できない。
今回、図書館で借りだした「自動車軽量化の生産技術」という技術書だが、自動車の整備とか修理には直接関わらないが、こういう内容を知っているのと知らないのでは、ものの見方が変わると云うか視野が広がるという点から、拙人として感心を持った部位のみを抽出して記してみたい。
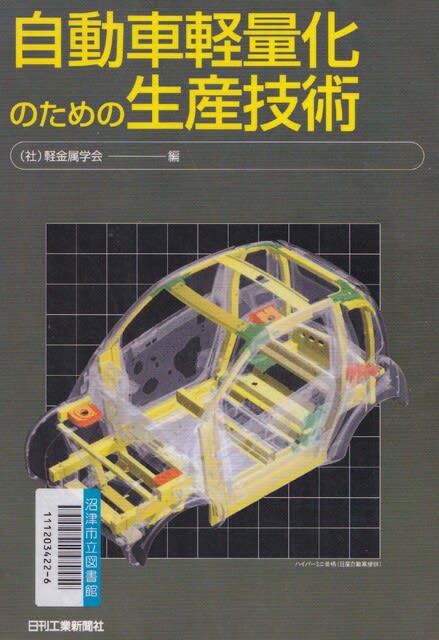
アルミボデーだが図に示す資料は90年から2000年頃までど若干古いが、90年のホンダNSXは初の量産オールアルミボデー車だ。ここで、気が付くこととして、材料構成比として、板材、押出材(引抜材も同意語)、鋳造材と三区分されているが、押出材とは同形状断面の連続体部位のみ成立する鍛造材に近い性能を持つが板材の一種と考えて良かろう。また、鋳造材とはダイキャストも鋳造の製法の一つと考えれば、ダイキャスト材と考えて良かろう。こういう点で、NSXは総て板材だったことが判る。

それが、以後の車両では、板材よりダイキャスト材が増加しているのが判る資料だ。現在でも、オールアルミボデー車は一部車両に残るが、やはり主流は鋼板ボデーで、アルミ材を使用するのは蓋物パーツとして呼ばれる、ボンネットとかフロントフェンダーやドアなどのボルトオンパーツに多い。一時、ベンツCLなどのリヤフェンダーとかルーフにアルミパネルが使用されたことがあったが、鋼板基本骨格にアルミ外板を強度負担パネルとして装着することは、溶接不可であり、接着剤とSPR(セルフピアッシングリベット)であり、日本メーカーならマスプロダクションの自動化に馴染まない絶体採用しない方式だろう。
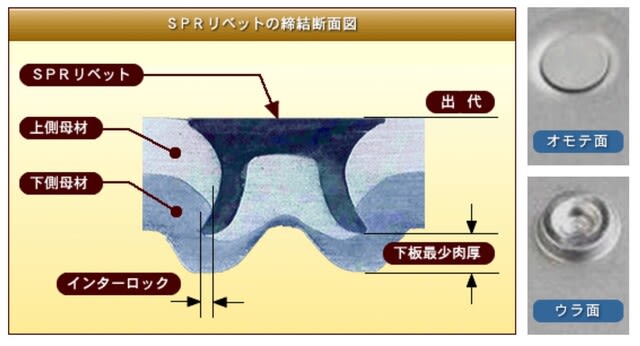
NSX以降でダイキャスト材が増えつつ板材がとして減ってはいるのだが、押出材は増えているという理由だが、ダイキャスト材の利用部位とは、サスペンションアームが装着される部位とか、押出材同士が集合する部位となる。こういう部位は、局部剛性が要求されたり、ラーメーン構造体(剛結構造体)として結合剛性が要求されるので、鋼板ボデーではスティフナーとかパッチと呼ばれる局部重ね補強構造が要求されたり、二重三重の重ね構造が要求されるが、ダイキャストだと形状の各部で要求板厚が自由自在になるとう利点がある。
このことは、現代車においても、基本鋼板ボデーだがフロントストラットタワー部のみアルミダイキャスを採用しているのは国産車でも、フロントアパーマウント式ダブルウッシュボーンサスの高級志向の車両に多くを見る。この場合、タワー下部のフロントサイドフレームまでをアルミにしているのは量産車ではBMW程度で、他はサイドフレームは鋼板製だ。
それと、現代車は、フロントバンパーは樹脂製なのは90年頃車と変わらないが、ぞの上部に位置してフード前のパネルとなる外装パネルまでフロントバンパーと一体成型の大型パネルになっているのは世界共通の構造的な傾向となった。フロントグリルは装着されるが、その取り付け相手部位は、このフロントエンドパネルとなる。こうして、樹脂フロントバンパーはフロントエンドパネルとして実質大型化している。
なお、この本とは別資料からの引用だが、テスラの思考を表すものとして、モデルYに途中から採用される様になっている前後骨格を丸ごとダイキャスト化した構造車が出て来ている。これは、従来の板材なら、優に100点を超える個別パーツを溶接なしに1ピース化できる構造で、マスプロダクション化により数分単位のサイクルタイムで成型でき、車体中央のキャビン部との接合も短時間かつ合理的だ。ただし、骨格損傷とか変型(というか素材特性上クラックとか割損となりそうだ)が生じると、極めて高額な修理費となり、事実上修理しないという事態になりそうだ。
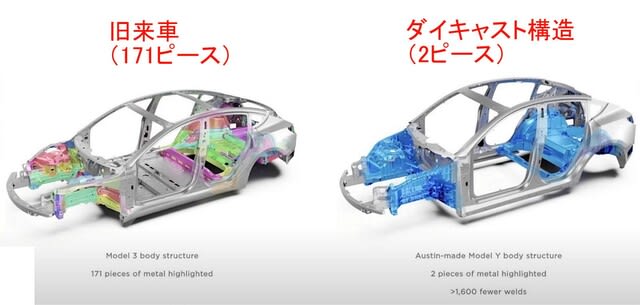
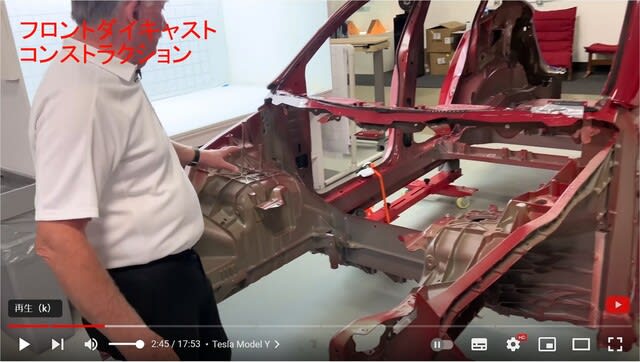
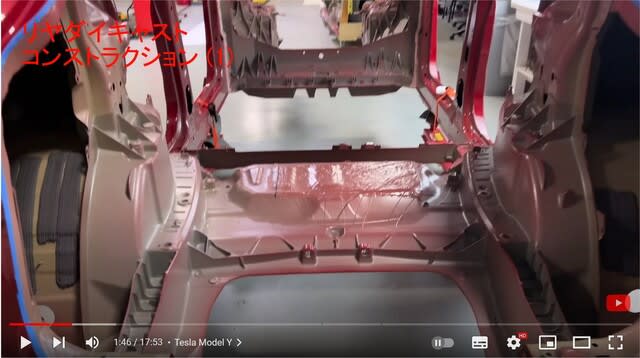
もう一つの話題として、フォーミングという形容詞があるが、日本語に直訳すると成型となる。このフォーミングの中にプレス成型とかダイキャストも含まれるのだが、プレス成型にしてもダイキャスや射出成型は雄型と雌型(固定型と可動型)とのセットで成立するが、固定型の単体で、その内側から高温気体を圧送するブロー成型という手法が、樹脂燃料タンクとか吸気マニホールドなどに使用される様になっている。
一方、高温気体でなく高圧液体を加圧することで、閉断面円柱を金型の断面に押し付け成型するチューブフォーミングという技法がエンジンメンバーなどに採用され出している。これは、従来、上下一対のプレス成型品を溶接で作っていたのを、溶接を少なくし、板厚も一定で寸法形状も優れるという工法だ。ここの参照図で「三五提供」と記してあるが、マフラー屋がサスペンションクロスメンバーを作るという技術の応用という点で気付きを思う。
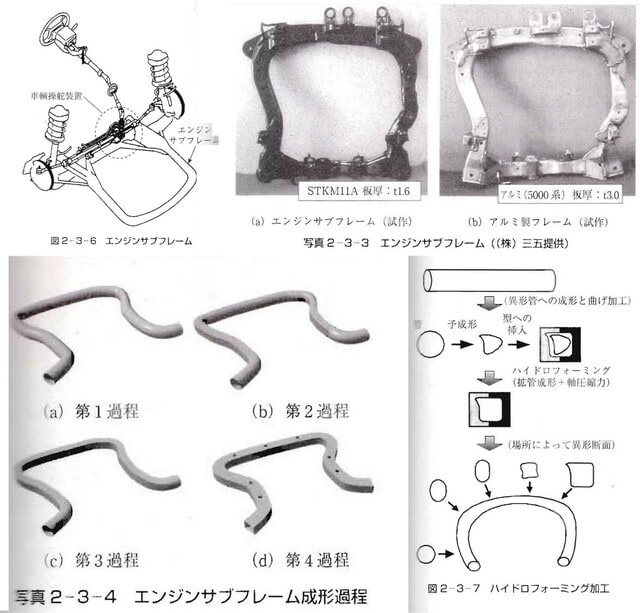