ボデー部材としてのアルミ化への潮流
ここでは、広く車をメカニカルとボデーという車両全般に眺める視点で、ボデーのアルミ化という流れで眺めてみたい。なお、アルミ化が主な目的として比重が鉄の概ね1/3という軽さがあるのだが変形し易さ(ヤング率)も概ね1/3だから、製造加工品としての重量は概ね2/3程度の軽量化となる。この様な点で、コストに糸目を付けないレーシングカーとか航空機では、長尺カーボン繊維を熱硬化性樹脂に混浸させて焼き固めたドライカーボン材が使用されるが、1品づつの製造ラニングタイムを要するとか、樹脂の経時変化で長期間の安定性が保証しかねるとか、部分修理が困難とかで、大型製品への使用は限定されることがある。それとアルミにしてもドライカーボンにしても耐熱性の限界が低く、あるみの場合で温度200℃で30%も引っ張り強度が低下すると云う性質があり、マッハ3を超すジェット戦闘機には空気摩擦で気体温度が上がるため使用が困難という問題もある様に聞くが、ドライカーボン材も同様だろう。ただ、カーボン材の中にはC/C材と云われるカーボン繊維とカーボン粉を超高圧高温で焼き固めたものがあり、ロケットのノーズコーンとか主翼前縁部とか、ブレーキディスクなどのある程度単純な形状部位には使用され、鉄を遙かに凌ぐ超高温まで耐えられるが、形状とか大きさの制限が大きく使用部位は限定されることがある。
1.旧世代のアルミボデー
1960年代までのころまでのイタリア車に多かった少量生産車などには、アルミボデーが使用されていることが多かった。旧車フェラーリで高名な246ディノというクルマがあるが、先行生産車である206ディノはアルミボデーであったが、量産ボデーとなった246ディノではプレス金型を使用したスチール製になっている。これ以前の、アルファTZ、SZなどの少量生産車は、アルミボデーで形作られていたが、これらはプレス型を使用せず、大まかな木型に手叩き板金成型した部分パーツを当てがうことで、成型しつつ、部分パーツを接合し、個別部品を作り出していた様だ。この時代、アルミ化の目的は、軽量化もあったのだろうが、それよりも加工のし易さという点で採用がなされていたと感じられる。
なお、F1などは現在はドライカーボンの単一成型品もしくは小数成型品を接着して作られるのが常套的だが、それ以前はアルミ材(板厚、種別、引き抜き材などの別)で折り曲げ加工した板材を組み合わせ、リベット接合した、アルミモノコック材で作られることが多かった。ただし、前後の末端バルクヘッド材などは、大板厚のアルミ材の機械加工したりして、ここにサスペンションビボットを設置したりエンジンマウントを設置したりする構成が多かったと見ている。
2.新世代のオールアルミボデー
ホンダが初代NSXで作り出したオールアルミボデーは、モノコックを構成するすべてのボデーパネルを多種のアルミ材をプレス加工しつつ、スポット溶接およびアルゴンガス雰囲気中のアーク溶接での連続溶接で接合する手法で組み上げられており、世界のスポーツカーメーカーに衝撃を与えたが、やはりコスト増加という点で、一般車に拡大することはなかった。
ただし、一般車でもフード、ドア、トランクリッド、フロントおよびリヤフェンダーなど蓋物ボルト付けパートパーツとしての採用は指向されて云った。このことは、現在では、樹脂パーツとして、フードだとかバックドアなどの表面パネルと裏骨パネルが接合されたパーツでも、採用が拡大しつつある。
3.現代的なアルミボデー
現在ではアルミパネルというよりダイキャストを使用したパートパーツをボデー骨格の要所に使用する事例が増えていると感じる。一番多いのがフロントのストラットタワー部のアルミダイキャスト化なのだが、これはストラットタワーと呼ぶが、実のところハイマウント式のアッパーアームのピボットを含んだもので、ダイキャスト化することで、必用部位の肉厚の自由度が増え、その他の減肉も行えるという自由度と十分な剛性を確保できるところに利点があるのだろうと想像できる。この辺りの構成は、従来の鋼板ボデーでは、強度要求によりパネルを重ね合わせて強度を得ていたのだが、余分な部分まで重ね合わせ面積が広がり、重量の点で不利となることを、ダイキャストの板厚自由度で補っているのだろう。
なお、これらアルミ材とスチール材の接合は、ボルトやセルフピアッシングリベットと接着剤の併用で、異種金属間でも溶接に頼らず、接合強度を得ている様だ。

なお、BMWなどでは、E60(2003年)以降でフロント骨格全体をアルミ化し、ダッシュパネル以降のスチールパネルと接合する構造が、常套手段として他の車種に拡大しつている。
4.現代的なオールアルミボデー
オールアルミボデーの車種は多くはないが、フェラーリや一部少量生産車では引き続いている。ここで、NSXなどとの違いは、骨格などのアルミ材は、なるべく引き抜き材を多用し、単純な断面での直線的に近い形状とし、その結合部にアルミダイキャストの結合点を持たせる構造が多くなっている様に見受けている。また、この結合点は、サスペンションビボットなどの局部応力を受ける部位でもあり、ダイキャストによる板厚自由度の利点を生かしていると思える。


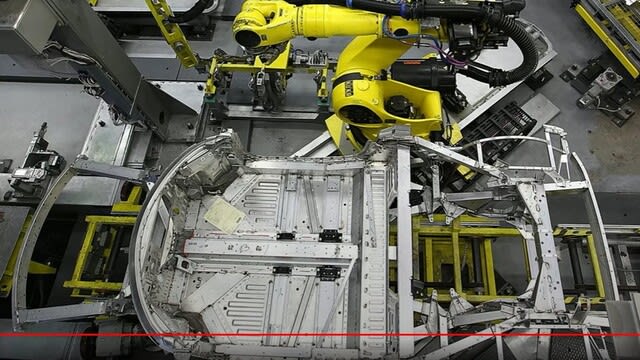
5.次世代の大物ダイキャスト材の使用によるオールアルミボデー
これはテスラの最新型モデルYなどで知れることだが、テスラというメーカーは、EVおよび自動運転を指向するメーカーだと思っていたが、クルマ作りを根本から変革しようという野望を秘めているメーカーだということを感じるところだ。アルミダイキャストは、そもそもボデー以前に、エンジンブロックとかトランスミッションケースと云った製品に、極めて短時間サイクルの製品作りで、金型を作るのには大きな設備投資が必用だが、多量製品だと劇的にコストを下げる技術なのだが、写真の様に、フロントサイドフレームからインナーフェンダーなどの、従来のプレス製品なら総パネル枚数10枚以上を高精度に組み上げる工程を、1つのアルミダイキャスト製品で作ってしまうという大きなクルマ作りの変革を見るところだ。

#アルミ材のボデーへの導入 #大物ダイキャスト材によるクルマ作りの変革
ここでは、広く車をメカニカルとボデーという車両全般に眺める視点で、ボデーのアルミ化という流れで眺めてみたい。なお、アルミ化が主な目的として比重が鉄の概ね1/3という軽さがあるのだが変形し易さ(ヤング率)も概ね1/3だから、製造加工品としての重量は概ね2/3程度の軽量化となる。この様な点で、コストに糸目を付けないレーシングカーとか航空機では、長尺カーボン繊維を熱硬化性樹脂に混浸させて焼き固めたドライカーボン材が使用されるが、1品づつの製造ラニングタイムを要するとか、樹脂の経時変化で長期間の安定性が保証しかねるとか、部分修理が困難とかで、大型製品への使用は限定されることがある。それとアルミにしてもドライカーボンにしても耐熱性の限界が低く、あるみの場合で温度200℃で30%も引っ張り強度が低下すると云う性質があり、マッハ3を超すジェット戦闘機には空気摩擦で気体温度が上がるため使用が困難という問題もある様に聞くが、ドライカーボン材も同様だろう。ただ、カーボン材の中にはC/C材と云われるカーボン繊維とカーボン粉を超高圧高温で焼き固めたものがあり、ロケットのノーズコーンとか主翼前縁部とか、ブレーキディスクなどのある程度単純な形状部位には使用され、鉄を遙かに凌ぐ超高温まで耐えられるが、形状とか大きさの制限が大きく使用部位は限定されることがある。
1.旧世代のアルミボデー
1960年代までのころまでのイタリア車に多かった少量生産車などには、アルミボデーが使用されていることが多かった。旧車フェラーリで高名な246ディノというクルマがあるが、先行生産車である206ディノはアルミボデーであったが、量産ボデーとなった246ディノではプレス金型を使用したスチール製になっている。これ以前の、アルファTZ、SZなどの少量生産車は、アルミボデーで形作られていたが、これらはプレス型を使用せず、大まかな木型に手叩き板金成型した部分パーツを当てがうことで、成型しつつ、部分パーツを接合し、個別部品を作り出していた様だ。この時代、アルミ化の目的は、軽量化もあったのだろうが、それよりも加工のし易さという点で採用がなされていたと感じられる。
なお、F1などは現在はドライカーボンの単一成型品もしくは小数成型品を接着して作られるのが常套的だが、それ以前はアルミ材(板厚、種別、引き抜き材などの別)で折り曲げ加工した板材を組み合わせ、リベット接合した、アルミモノコック材で作られることが多かった。ただし、前後の末端バルクヘッド材などは、大板厚のアルミ材の機械加工したりして、ここにサスペンションビボットを設置したりエンジンマウントを設置したりする構成が多かったと見ている。
2.新世代のオールアルミボデー
ホンダが初代NSXで作り出したオールアルミボデーは、モノコックを構成するすべてのボデーパネルを多種のアルミ材をプレス加工しつつ、スポット溶接およびアルゴンガス雰囲気中のアーク溶接での連続溶接で接合する手法で組み上げられており、世界のスポーツカーメーカーに衝撃を与えたが、やはりコスト増加という点で、一般車に拡大することはなかった。
ただし、一般車でもフード、ドア、トランクリッド、フロントおよびリヤフェンダーなど蓋物ボルト付けパートパーツとしての採用は指向されて云った。このことは、現在では、樹脂パーツとして、フードだとかバックドアなどの表面パネルと裏骨パネルが接合されたパーツでも、採用が拡大しつつある。
3.現代的なアルミボデー
現在ではアルミパネルというよりダイキャストを使用したパートパーツをボデー骨格の要所に使用する事例が増えていると感じる。一番多いのがフロントのストラットタワー部のアルミダイキャスト化なのだが、これはストラットタワーと呼ぶが、実のところハイマウント式のアッパーアームのピボットを含んだもので、ダイキャスト化することで、必用部位の肉厚の自由度が増え、その他の減肉も行えるという自由度と十分な剛性を確保できるところに利点があるのだろうと想像できる。この辺りの構成は、従来の鋼板ボデーでは、強度要求によりパネルを重ね合わせて強度を得ていたのだが、余分な部分まで重ね合わせ面積が広がり、重量の点で不利となることを、ダイキャストの板厚自由度で補っているのだろう。
なお、これらアルミ材とスチール材の接合は、ボルトやセルフピアッシングリベットと接着剤の併用で、異種金属間でも溶接に頼らず、接合強度を得ている様だ。

なお、BMWなどでは、E60(2003年)以降でフロント骨格全体をアルミ化し、ダッシュパネル以降のスチールパネルと接合する構造が、常套手段として他の車種に拡大しつている。
4.現代的なオールアルミボデー
オールアルミボデーの車種は多くはないが、フェラーリや一部少量生産車では引き続いている。ここで、NSXなどとの違いは、骨格などのアルミ材は、なるべく引き抜き材を多用し、単純な断面での直線的に近い形状とし、その結合部にアルミダイキャストの結合点を持たせる構造が多くなっている様に見受けている。また、この結合点は、サスペンションビボットなどの局部応力を受ける部位でもあり、ダイキャストによる板厚自由度の利点を生かしていると思える。


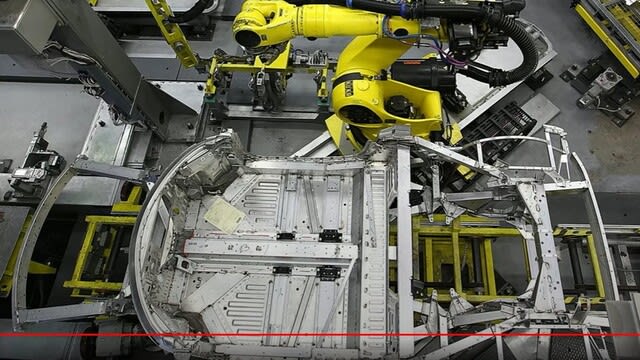
5.次世代の大物ダイキャスト材の使用によるオールアルミボデー
これはテスラの最新型モデルYなどで知れることだが、テスラというメーカーは、EVおよび自動運転を指向するメーカーだと思っていたが、クルマ作りを根本から変革しようという野望を秘めているメーカーだということを感じるところだ。アルミダイキャストは、そもそもボデー以前に、エンジンブロックとかトランスミッションケースと云った製品に、極めて短時間サイクルの製品作りで、金型を作るのには大きな設備投資が必用だが、多量製品だと劇的にコストを下げる技術なのだが、写真の様に、フロントサイドフレームからインナーフェンダーなどの、従来のプレス製品なら総パネル枚数10枚以上を高精度に組み上げる工程を、1つのアルミダイキャスト製品で作ってしまうという大きなクルマ作りの変革を見るところだ。

#アルミ材のボデーへの導入 #大物ダイキャスト材によるクルマ作りの変革