加工開始!
いつも通りの手順で
図面を両面テープで貼り付け→穴あけから
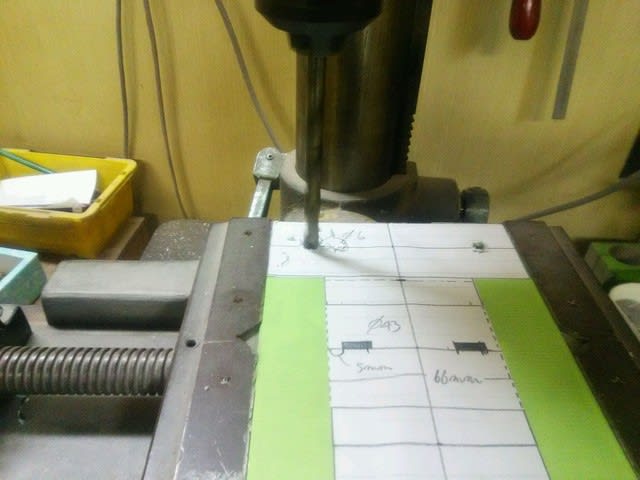
鉄ノコでCUT

頻繁に使用している2mm厚より楽チン
0.5mmで、こんなにも差が出るとは

ホースバンドを通す穴を、ヤスリで整えて
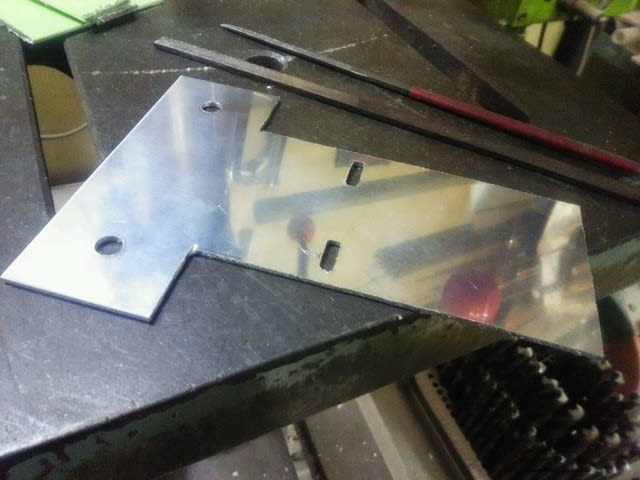
切断面とRは、粗方グラインダーで整える

段ボールを巻いて作った
バッテリーレスのダミーを目安にし

φ40の丸棒を当て木に、叩き曲げ
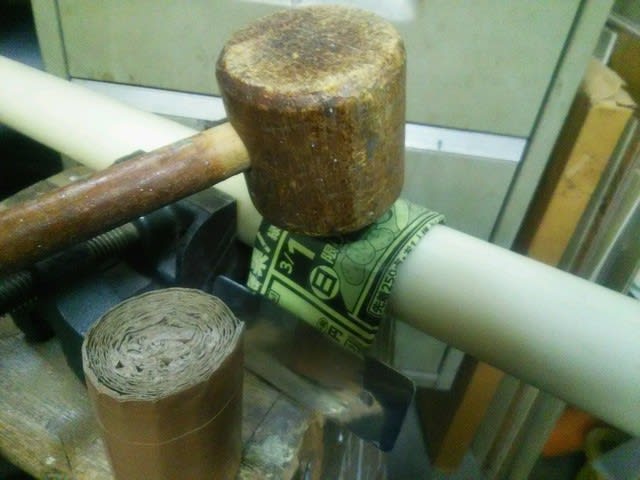
表面の50%程度をクランプし
ホースバンドを本体へ挿し通し、固定する設計です!

まぁ…
折れてしまいましたがねw

先にホースバンドを通す穴を、あけた事が失敗です。
実は 木槌で叩いた一発目で 曲面というよりは鈍角に曲がって
いや…
曲がってと言うより 折れてしまいました。
後は叩いている間に、じわりじわりと。。。
2mm厚だったら、もう少し何とかなったかも知れませんが
曲面処理を行うには、やはり1.5mm厚が正解だった印象です。
いやぁ~
久々に加工中に破損してしまいました(T_T)
さて、どうしたものか…
ご訪問ありがとうございます!!
地味にランキング参加中。お気持ちでクリックをm(_ _)m
↓
にほんブログ村
いつも通りの手順で
図面を両面テープで貼り付け→穴あけから
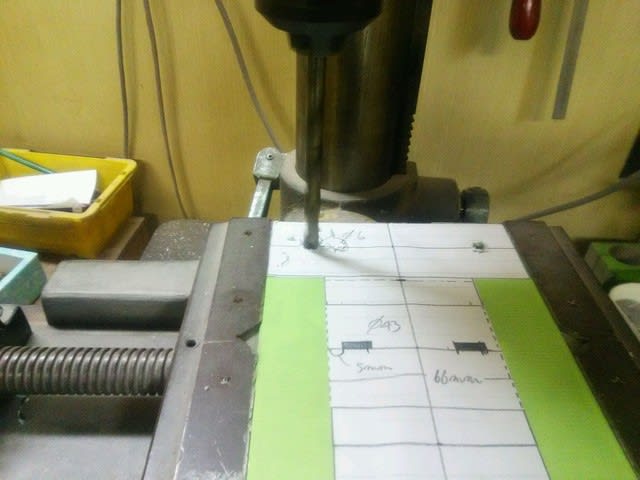
鉄ノコでCUT

頻繁に使用している2mm厚より楽チン
0.5mmで、こんなにも差が出るとは

ホースバンドを通す穴を、ヤスリで整えて
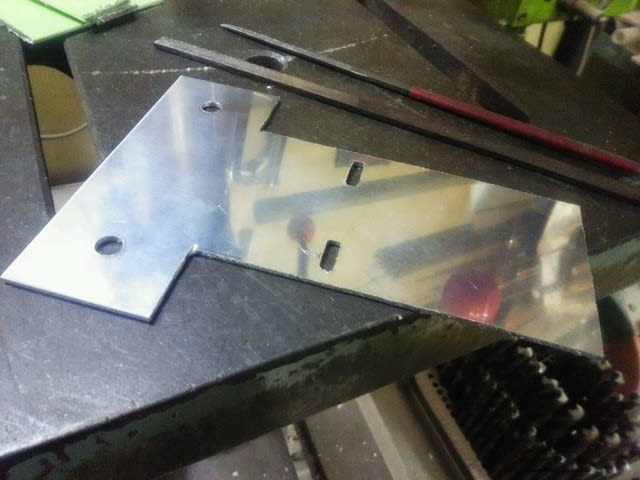
切断面とRは、粗方グラインダーで整える

段ボールを巻いて作った
バッテリーレスのダミーを目安にし

φ40の丸棒を当て木に、叩き曲げ
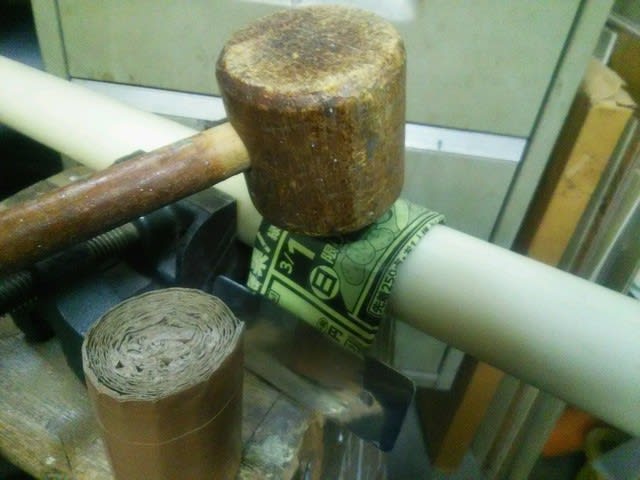
表面の50%程度をクランプし
ホースバンドを本体へ挿し通し、固定する設計です!

まぁ…
折れてしまいましたがねw

先にホースバンドを通す穴を、あけた事が失敗です。
実は 木槌で叩いた一発目で 曲面というよりは鈍角に曲がって
いや…
曲がってと言うより 折れてしまいました。
後は叩いている間に、じわりじわりと。。。
2mm厚だったら、もう少し何とかなったかも知れませんが
曲面処理を行うには、やはり1.5mm厚が正解だった印象です。
いやぁ~
久々に加工中に破損してしまいました(T_T)
さて、どうしたものか…
ご訪問ありがとうございます!!
地味にランキング参加中。お気持ちでクリックをm(_ _)m
↓
