膨張室/固定方法の見直し
他車種流用となれば、多少の工夫は必須
汎用ステーで、一旦は固定したが…
そこは工作好きw
ステップホルダー共締めは活かし プレートを製作
固定した事で、現物合せのざっくり図面も出来て
まぁ 遠回りだが無駄では無し

程良い端材を選び
勘が働き、手書きで少し長めに変更
いつもの手順でボール盤から
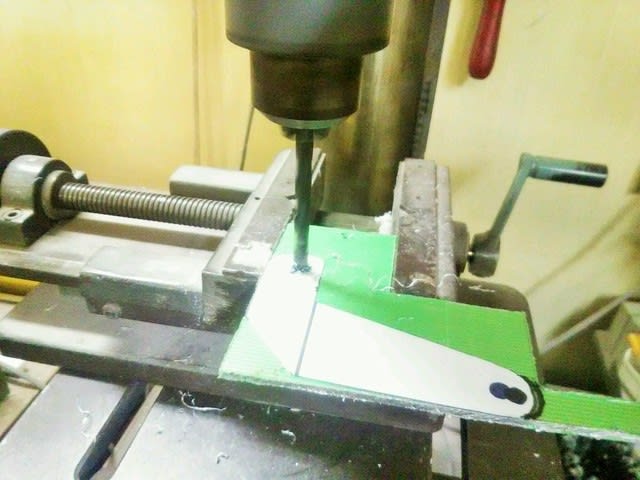
ギコギコして

粗方整え 40度程に曲げる

厚みは2mmか3mmで悩んだが
2mmをチョイスし、曲げ部のレングスを稼げるデザインにし
材料の厚みによる、強度不安を補う
とりま形に

ホルダー側へM8タップを切り

仮組 少しホルダーからはみ出ている
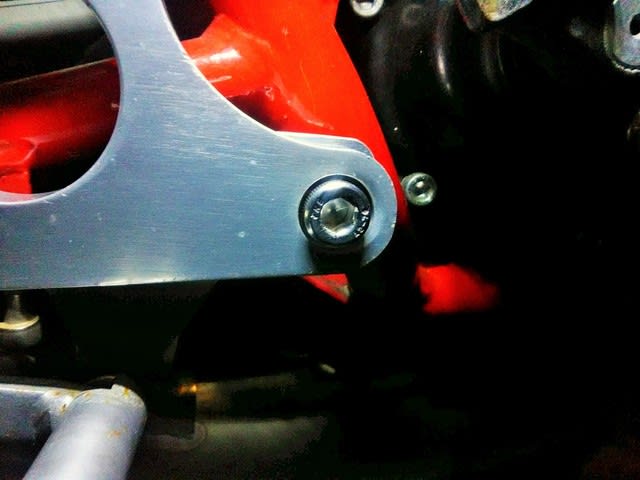
はみ出た部分をマーキングし
現物合せで削り込み

最近 グラインダーで楽してたから
ちと おっくうw
再度仮組→OK
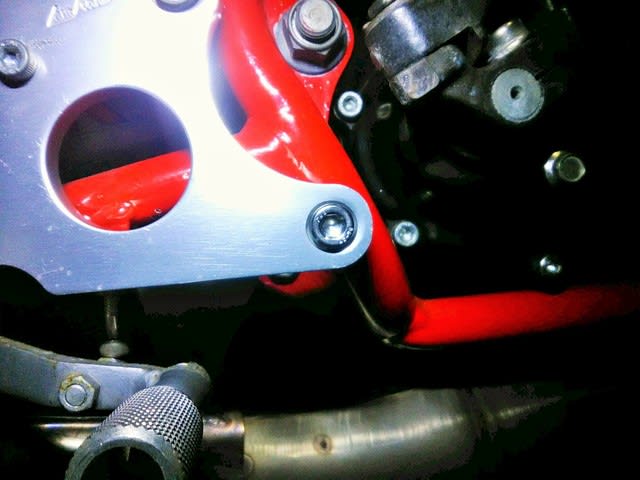
膨張室を固定し作業終了!

勘が冴えた様で、数mmの延長でジャスト
チャンバーを外すには、膨張室側のボルトを
ステップを外すには、ホルダー側のボルトを
各々ミニマムの分解で済む設計
目指したのは、機能美と造形美の両立(*`・ω・)ゞ
副産物的に、ホルダーと膨張室が引き合う事で
ホルダー側の補強にも一役
少し距離を走ってから、耐震処理が必要か判断
これにてチャンバー交換 完了!
ご訪問ありがとうございます!!
地味にランキング参加中。お気持ちでクリックをm(_ _)m
↓
にほんブログ村
他車種流用となれば、多少の工夫は必須
汎用ステーで、一旦は固定したが…
そこは工作好きw
ステップホルダー共締めは活かし プレートを製作
固定した事で、現物合せのざっくり図面も出来て
まぁ 遠回りだが無駄では無し

程良い端材を選び
勘が働き、手書きで少し長めに変更
いつもの手順でボール盤から
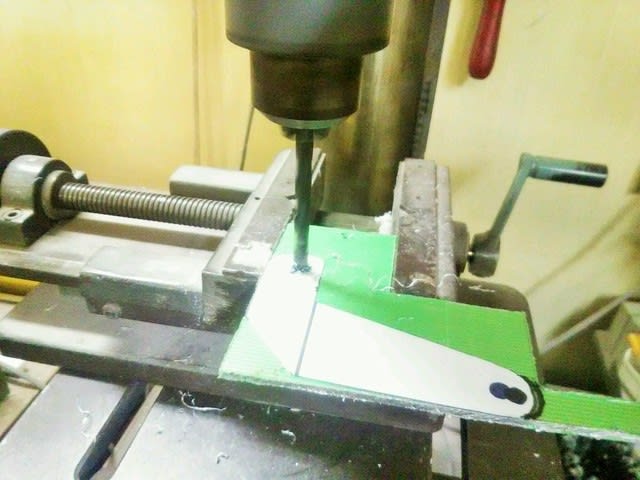
ギコギコして

粗方整え 40度程に曲げる

厚みは2mmか3mmで悩んだが
2mmをチョイスし、曲げ部のレングスを稼げるデザインにし
材料の厚みによる、強度不安を補う
とりま形に

ホルダー側へM8タップを切り

仮組 少しホルダーからはみ出ている
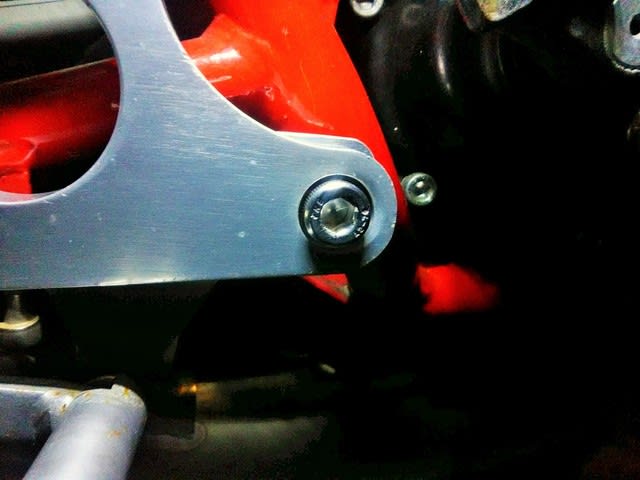
はみ出た部分をマーキングし
現物合せで削り込み

最近 グラインダーで楽してたから
ちと おっくうw
再度仮組→OK
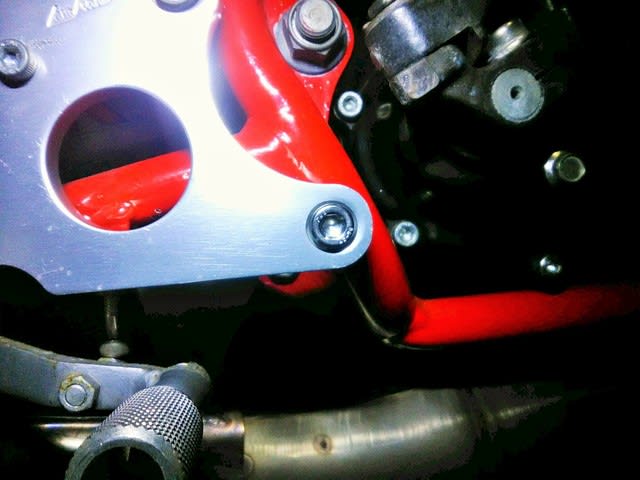
膨張室を固定し作業終了!

勘が冴えた様で、数mmの延長でジャスト
チャンバーを外すには、膨張室側のボルトを
ステップを外すには、ホルダー側のボルトを
各々ミニマムの分解で済む設計
目指したのは、機能美と造形美の両立(*`・ω・)ゞ
副産物的に、ホルダーと膨張室が引き合う事で
ホルダー側の補強にも一役
少し距離を走ってから、耐震処理が必要か判断
これにてチャンバー交換 完了!
ご訪問ありがとうございます!!
地味にランキング参加中。お気持ちでクリックをm(_ _)m
↓
