日々のパソコン案内板
【Excel関数】 No.1(A~I) No.2(J~S) No.3(T~Y)
【Excelの小技】 【HTMLタグ&小技】
【PDFの簡単セキュリティ】
【複数フォルダーを一括作成するんならExcelが超便利だよ!!】
【アップデートが終わらない!? Windowsの修復ツールを使ってみる方法】
【削除してしまったファイルやデータを復元する方法ー其の一(以前のバージョン)】
【削除ファイルやデータを復元する方法ー其の二(ファイル履歴)】
【Excel振替伝票の借方に入力したら貸方に対比する科目を自動記入】
【手書きで書くように分数表記する方法】
【Web上のリンクさせてある文字列を選択する方法】
【Excel2010以降は条件付き書式設定での文字色にも対応!】
【Windows10のWindows PowerShellでシステムスキャンの手順】
![]() | 品番<962> 幅 20mm |
羽衣ラメトーションレース 自分で小物を創って・・・ 小物のアクセント付けに!! 用途に応じて幅も柄も色々取り揃えています! 小売りのカット売りも可能ですので、ご遠慮なくご相談下さい! |
昨日、ポストに「Gift Show Autumn 2016」の封書が投函されていた・・・
且つて、大阪でもやっていたので結構通っていたんですが、
大阪では開催されなくなり、自然と足が遠のいていました・・・
この封書を見て、内心「何年も行ってないのに未だに来るんやな・・・」
東京まで足を伸ばすことはできないから、処分しておこうか・・・と何気に差出人を見れば
大阪の弊社のお得意様からの招待でした。
この企業様は、あくまでも国内生産にこだわりを持たれており、
ハンドメイドで一点一点創り上げられているアパレルメーカーさんなんですね。
何度かお取引をさせて頂いたのですが、
原料からのこだわりが非常に強く、時には1Kg2万円近くする糸を持って来られることもありました。
オリジナル服や装飾品を全国の専門店へ直接卸されてるようです。
3日ほど前にもお電話を頂きましたが、
お互いの日時の調整がつかず、後日の打ち合わせとなりましたが、
このメーカーさんの取り組みを見ていて、
創る立場の人間が少しでも消費者に近づいて行くようなシステム作りの大切さを改めて認識させられております。
世界の企業も安い人件費探しから、ITの高度化を活用し自国生産に回帰しつつあるようです。
今朝は、そんな経済の現場からの記事を転載してみようと思います。
~以下、9月3日読売新聞朝刊より抜粋~
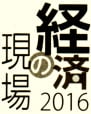
日本橋高島屋(東京都中央区)に出店する衣料ブランド「ビスコテックス」で、50歳代の女性が柄や色、形など47万通りの組み合わせから選んだ「自分だけのワンピース」を笑顔で受け取った。
繊維メーカー・セーレンが、客の好みに応じたオーダーメイド生産を昨年から始めた。消費者は店内の端末でデザインを決め、等身大モニターに移した自分の姿に重ねて「試着」する。
第4次産業革命
データは福井県の工場にネットで送られ、自社開発のインクジェットプリンターが生地を自動で染色、縫製して約3週間で出来上がる。進むIT化 脱・大量生産
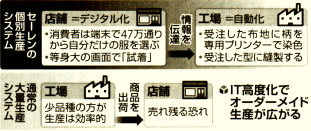
個別製品の生産は、膨大なデータの処理といった情報技術(IT)の高度化、モノ作りの自動化など最新の技術で可能になった。
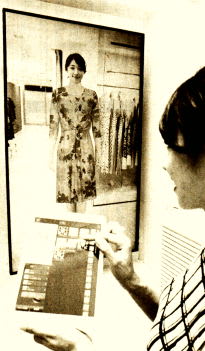
富士通は島根県出雲市の子会社で、パソコンやタブレット端末を個別の注文に応じて数個単位から製造している。多種多様な仕様の製品を年間200万台出荷する。
注文ごとに様々な部品を、最適なタイミングで集めて組み立てる。製造ラインの情報を共有するシステムを構築し、ロボットと人が連携することで効率的な「スマート工場」が実現した。生産にかかる期間は2日前後と、通常の半分程度だ。
セーレンの「仮装試着」。デジタル化と自動化でオーダーメイド生産が可能になった(東京都中央区で)=高橋美帆撮影
子会社の宇佐美隆一社長は「顧客の個別の要望に応えるには、徹底して生産性を高める必要がある。日本のもの作りを守ることにもつながる」と話す。
消費者のニーズを素早く捉えるには、消費地で生産した方が有利だ。先進国の企業は、安い人件費を求めて途上国に進出してきたが、技術の進化で製造コストは大きく下がった。先進国で生産拠点の自国回帰が進む。
コンタクトレンズ大手のメニコンが昨年末、岐阜県各務原市で稼働を始めた工場は、31年ぶりの国内新工場だ。コンタクトレンズは視力や眼球の形などに応じて数万通りの製品が求められ、コストの安いアジアなど海外工場で製造している。自社製品の利用者約110万人分のデータを分析し、需要を先読みする技術を高め、無駄のない生産で国内回帰を実現した。
もの作り大国のドイツでも、スポーツ用品大手のアディダスが、ロボット技術を活用し、シューズを自国内で生産する「スピードファクトリー」計画を打ち出した。「メイド・イン・ドイツ」は約四半世紀ぶりになる。米国でも、外国企業への生産委託が中心だったアップルが国内生産に切り替えている。
消費者一人一人のニーズに応えるため、どこで、どのように作るか――。企業は対応を迫られている。