本日の山陰は曇り時々晴れでした、この数日を考えればまあ良い天気でしたね。
でも気温は結構低めですね〜午前中に塗料を送る為に郵便局まで行きましたが日陰はまだ凍結中でした・・・(笑)
ホンダライフが4WDである事を感謝しましたね。
まだ1月下旬、数日すると2月ですからね〜
節分頃には毎年寒波が来ますから油断禁物です
体重落としてから一気に寒さに弱くなってしまいました、体調は良いんだけどね〜。
両方良いなんて事は難しいのかもしれませんね・・・
さて本日も仕事です。
後がつかえていますからどんどん作ってゆかなければなりません。
今日はこの部分です
ダッシュボードの上に有るデフロスターの吹き出し口ですね。
キットではエッチング板が一枚貼られるだけです
しかし実車にはこの楕円形の板も無いし吹き出し口の立体感がなさ過ぎですよね〜
その上この位置はフロントウインドウ越しに良く見える部分でもあります
これではちょっと残念なので作り替える事に致します

この吹き出し口の部品を作る事が出来たらデフロスターの問題は簡単に解決すると思いますのでまずはプロクソンのフライスを使って吹き出し口のサンプルを作ってみます
直径を5.5mmに削った真鍮の丸棒にフライスで溝を掘ってゆきます
たまたま持っていたエンドミルが0.8mmしかなかったのでそれで深さを1.5mm程にして掘っています
本来ですと4つ欲しいので4つを一緒に加工するのが良いのですが、溝幅が0.8mmで良いのかまた吹き出し口のフラップが0.3mmで良いのかの確認用として加工を始めます
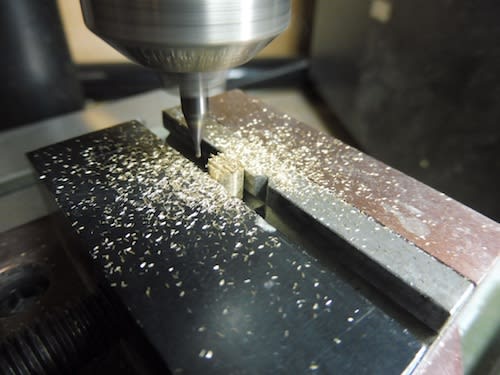
切削が終わったので掃除機を使って切り子を集めて拡大してみました・・・
思ったよりも良い感じなのでこれでいこうかと思います
刃物の位置関係を変えずにそのままの位置関係をそのまま使います

今回使う部品を削ります・・・つまり本番用という事です
所定のサイズにカットした真鍮の丸棒を4つハンダで連結します
上側のリングは一昨日エキゾーストの出口のリングで試作したハンダ線のリングです
もう使い道が無のでこんな場合にハンダ付けに使っています(笑)
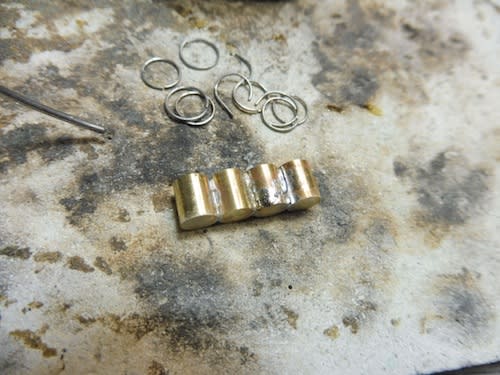
削る面を整えておきます
高さが変化すると最終的に出来る物が歪んでしまったりしますのでここは大切な所です

素材をバイスに固定して刃物の上下方向を調整してから・・・左右方向は絶対に触らず(切削位置が変わってしまいます)・・・切削開始です
1.0mm以下のエンドミルを使う場合彫りの深さにも寄りますが送りの量は最低限にしておかないと必ず刃物を折ってしまうので注意しながら慎重な作業が要求されます
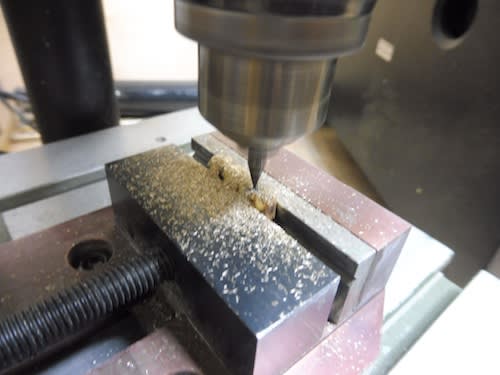
完成したのがこちらです・・・
全て一体に加工しましたのでハンダ付けの位置関係が狂っていなければこの様に全て同じ様に切削出来ます
まだデフロスターの吹き出し口には見えませんが・・・(笑)

4つの部品のハンダは外さないままバイスに固定します
そして各々の中央に有る吹き出しのフラップの角度を調整する部分を差し込む為のスリ割りを入れてゆきましょう
これくらいならフライスを使わなくても糸鋸で十分です

加工して来た部品を分解しまして中央のスリ割り(先ほど糸鋸で入れた部分ですね)に0.3mmの真鍮板を差し込んでハンダ付けです
余分なハンダが回らない様に気をつけないと修正が難しくなります

両端の飛び出した余分な部分を削って仕上げます
この部品は手で向きを変える為に両端が持ち上がった様な形状をしています
実車ではここを指でつまんで回したり吹き出しの角度を変えたりするんですね

続いてまた旋盤でリングを削り出しています
このリングは内径が5.5mm外径が6.0mmです
つまり厚みは0.25mmという事になりますね

リングはこんな風に使います
これで吹き出し口らしくなってきましたかね〜!?(笑)

リングの仮組が出来た所で引き出し口のパーツを薄く切り出しましょう
と言うのも切り出さなくても良いのですがそのままですとダッシュボードの上側の穴が深くなってしまうので加工が難しくなってしまうのです
ですから奥行きは欲しいけどいい加減な部分でカットして使わなければなりません
今回は飛び出したツマミの部分は別として厚みを2.5mmとしています

ダッシュボードに先ほどの部品を埋め込む為に穴を掘らなければなりませんがこの硬質のレジンにいきなりフリーハンドで穴を掘るのは危険ですよね
そこであの役に立たない!?エッチング板の吹き出し口の部分に6.0mmの穴を開けてダッシュボードに瞬間接着剤で貼付けました
そうなんですこれをガイドにして掘り込んでゆく作戦ですね
穴の配置もバランスが必要ですから直接ケガキ線を入れて削るよりもこの方が間違いが有りません

エッチング板をガイドにして穴を掘り込んでみました
最初は丸いボールエンドのビットを使って2.5mm程掘り込みまして後は大きめの円筒形の物を使って整えています
硬いレジンなので強くリューターのビットを当てると欠けてしまって隣りの穴とつながりそうなので緊張しました
いつもよりも時間がかかったのはそのせいですね〜。

作った部品を穴の中に入れて仮組をしてみました
如何ですか?
これだけ作るのに約一日と時間はかかりましたがエッチング一枚では出ない立体感が出たんじゃないかと・・・

明日はコクピット内の部品の塗装にかかりましょうかね〜
でも気温は結構低めですね〜午前中に塗料を送る為に郵便局まで行きましたが日陰はまだ凍結中でした・・・(笑)
ホンダライフが4WDである事を感謝しましたね。
まだ1月下旬、数日すると2月ですからね〜
節分頃には毎年寒波が来ますから油断禁物です
体重落としてから一気に寒さに弱くなってしまいました、体調は良いんだけどね〜。
両方良いなんて事は難しいのかもしれませんね・・・
さて本日も仕事です。
後がつかえていますからどんどん作ってゆかなければなりません。
今日はこの部分です
ダッシュボードの上に有るデフロスターの吹き出し口ですね。
キットではエッチング板が一枚貼られるだけです
しかし実車にはこの楕円形の板も無いし吹き出し口の立体感がなさ過ぎですよね〜
その上この位置はフロントウインドウ越しに良く見える部分でもあります
これではちょっと残念なので作り替える事に致します

この吹き出し口の部品を作る事が出来たらデフロスターの問題は簡単に解決すると思いますのでまずはプロクソンのフライスを使って吹き出し口のサンプルを作ってみます
直径を5.5mmに削った真鍮の丸棒にフライスで溝を掘ってゆきます
たまたま持っていたエンドミルが0.8mmしかなかったのでそれで深さを1.5mm程にして掘っています
本来ですと4つ欲しいので4つを一緒に加工するのが良いのですが、溝幅が0.8mmで良いのかまた吹き出し口のフラップが0.3mmで良いのかの確認用として加工を始めます
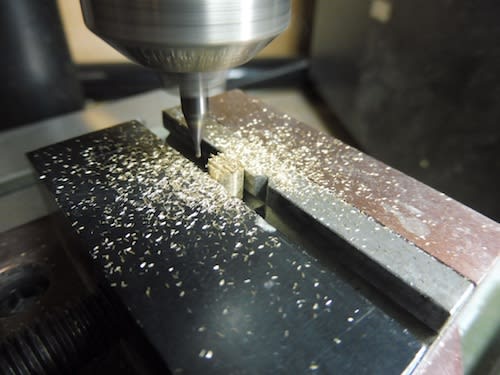
切削が終わったので掃除機を使って切り子を集めて拡大してみました・・・
思ったよりも良い感じなのでこれでいこうかと思います
刃物の位置関係を変えずにそのままの位置関係をそのまま使います

今回使う部品を削ります・・・つまり本番用という事です
所定のサイズにカットした真鍮の丸棒を4つハンダで連結します
上側のリングは一昨日エキゾーストの出口のリングで試作したハンダ線のリングです
もう使い道が無のでこんな場合にハンダ付けに使っています(笑)
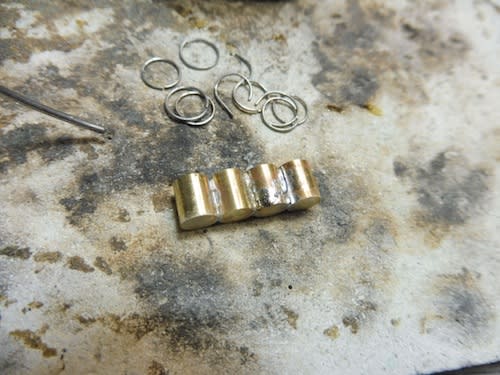
削る面を整えておきます
高さが変化すると最終的に出来る物が歪んでしまったりしますのでここは大切な所です

素材をバイスに固定して刃物の上下方向を調整してから・・・左右方向は絶対に触らず(切削位置が変わってしまいます)・・・切削開始です
1.0mm以下のエンドミルを使う場合彫りの深さにも寄りますが送りの量は最低限にしておかないと必ず刃物を折ってしまうので注意しながら慎重な作業が要求されます
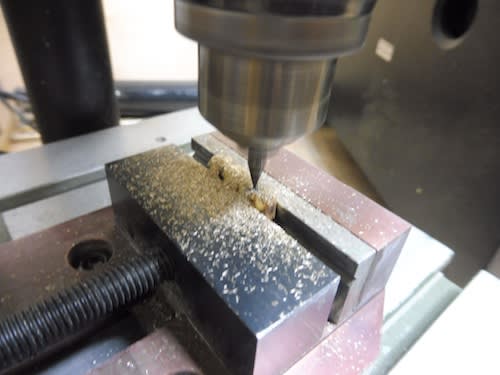
完成したのがこちらです・・・
全て一体に加工しましたのでハンダ付けの位置関係が狂っていなければこの様に全て同じ様に切削出来ます
まだデフロスターの吹き出し口には見えませんが・・・(笑)

4つの部品のハンダは外さないままバイスに固定します
そして各々の中央に有る吹き出しのフラップの角度を調整する部分を差し込む為のスリ割りを入れてゆきましょう
これくらいならフライスを使わなくても糸鋸で十分です

加工して来た部品を分解しまして中央のスリ割り(先ほど糸鋸で入れた部分ですね)に0.3mmの真鍮板を差し込んでハンダ付けです
余分なハンダが回らない様に気をつけないと修正が難しくなります

両端の飛び出した余分な部分を削って仕上げます
この部品は手で向きを変える為に両端が持ち上がった様な形状をしています
実車ではここを指でつまんで回したり吹き出しの角度を変えたりするんですね

続いてまた旋盤でリングを削り出しています
このリングは内径が5.5mm外径が6.0mmです
つまり厚みは0.25mmという事になりますね

リングはこんな風に使います
これで吹き出し口らしくなってきましたかね〜!?(笑)

リングの仮組が出来た所で引き出し口のパーツを薄く切り出しましょう
と言うのも切り出さなくても良いのですがそのままですとダッシュボードの上側の穴が深くなってしまうので加工が難しくなってしまうのです
ですから奥行きは欲しいけどいい加減な部分でカットして使わなければなりません
今回は飛び出したツマミの部分は別として厚みを2.5mmとしています

ダッシュボードに先ほどの部品を埋め込む為に穴を掘らなければなりませんがこの硬質のレジンにいきなりフリーハンドで穴を掘るのは危険ですよね
そこであの役に立たない!?エッチング板の吹き出し口の部分に6.0mmの穴を開けてダッシュボードに瞬間接着剤で貼付けました
そうなんですこれをガイドにして掘り込んでゆく作戦ですね
穴の配置もバランスが必要ですから直接ケガキ線を入れて削るよりもこの方が間違いが有りません

エッチング板をガイドにして穴を掘り込んでみました
最初は丸いボールエンドのビットを使って2.5mm程掘り込みまして後は大きめの円筒形の物を使って整えています
硬いレジンなので強くリューターのビットを当てると欠けてしまって隣りの穴とつながりそうなので緊張しました
いつもよりも時間がかかったのはそのせいですね〜。

作った部品を穴の中に入れて仮組をしてみました
如何ですか?
これだけ作るのに約一日と時間はかかりましたがエッチング一枚では出ない立体感が出たんじゃないかと・・・

明日はコクピット内の部品の塗装にかかりましょうかね〜