The Rest Room of ISO Management
ISO休戦
“ISOを活かす― 9. ISOの効果的な運用によって、新製品をタイムリーに開発する”
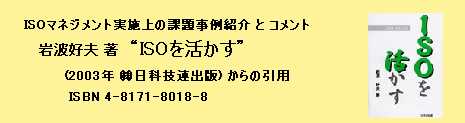
今回は IT産業での製品開発へのISO9001適用が テーマです。
【組織の問題点】
パソコンメーカーのA社は 5年前にISOの認証を取得した。次々新製品を市場に提供しなければならないA社では設計・開発途中のやり直しで 開発期間が長くなることが多い。また生産開始直後のトラブルも多く、本格量産に入るまで時間がかかっている。このA社はISOをどのように活用するべきか、というものです。
【磯野及泉のコメント】
新技術の開発が 早いと言われるIT産業の一角を担う、パソコンメーカーで重要なことは 新機軸を盛り込んだ製品をいち早く市場に展開することです。それに、品質の確保は当然で 品質不良で市場というか顧客の信頼を失うようでは 元も子もありません。そこで パソコンの新製品開発で重要なことは 次の2つと指摘されています。
“①設計・開発中のやり直しを少なくすることによって、新機種の設計・開発期間を短縮する。
②生産開始後に品質問題が起こらないようにすることによって、設計・開発が終了すると同時に、本格的な量産が開始できるようにする。”
そこで、①に対してはISO9001で規定されているデザインレビューを確実に行うことで(7.3.4項)、設計・開発のやり直しを 少なくするとともに、以前の類似した設計情報の活用(7.3.2項)で 設計・開発期間を短縮することができる。
②に対しては、製造仕様書など製造につながる設計・開発のアウトプットの検証(7.3.5項)と 設計の妥当性確認(7.3.6項)を確実に行うことで、早期に本格量産へ移行できる。
と、この著者・岩波氏は書いています。
著者・岩波氏によればISO9001が あたかも万病に効く万能薬のような 表現になっていますが 具体性に欠ける印象です。
“過去の設計情報の活用”、“デザインレビュー(設計のレビュー)”、“設計・開発のアウトプットの検証”、“妥当性確認”を“効果的に”そして“確実に”実施することで 本当に“開発期間の短縮”や “設計・開発が終了すると同時に本格的な量産開始” が 可能なのでしょうか。そもそも“「効果的に」あるいは「確実に」実施する”とは どうすることなのでしょうか。実は これが 肝心なところだと思うのですが 残念ながら明確に示されていません。
念のため 設計・開発のプロセスを 分解し図示すると下図のようになります。これが 基本的な設計・開発プロセスだと言えます。どの順序で 何をすれば ISO9001の規定要求事項を満足するのか理解しやすいと思います。

この図を見て 分かるように 大抵の会社では このようなことは 意識・無意識に実施されていると思うのです。それを、ISO9001の規定要求事項を 厳密に手順化して、顕在意識下で実施したからと言って それが抜本的改善につながり、“開発期間の短縮”や “設計・開発が終了すると同時に本格的な量産開始” が 可能となるとは 思えません。これまでの手抜きによる ポカミスのようなものが改善される程度のような気がします。まぁ それだけの改善でも ことが設計・開発だけに 十分に意味あることだとは 思いますが、この著者・岩波氏の 説明は 少々誇大な印象です。
こうした 設計・開発プロセスで失敗しないために 従来から様々な手法が提案されています。
私が 最初に 注目したのは 信頼性技法としてのFMEAを中心にした一連の技法でした。ですが、FMEAは 過去の実績や経験をベースにしていますので、経験の積み重ねが重要です。逆に 経験がなければ 非常に無力です。故障モードの摘出は 経験ある関係者のブレーン・ストーミングが ベースになっており、これが重要ポイントになっています。FTAにしても 各部品の故障率というか信頼性の数字を ベースに システム全体の信頼性を推計し、改善の余地をさぐることになっています。要するに 既に データ(経験値)が 有ることが前提になっています。
次に注目したのは 品質機能展開QFDの手法でした。これも 開発の必要事項を もれなく実施するということで 非常に有意義です。ですが もれなく行うには、他社の製品との比較など 製品そのものの技術情報よりも 製品に付随する その他情報を入手することにも 精力を注がなければなりません。それに 実際に 情報を展開すると 一部屋分の広さの紙が 必要だということも聞いたことがあり、あまり実用的とは言えません。
これらに 対して 品質工学の適用は 過去の経験を問うことや、他社製品の情報も 気にすることはありません。開発する製品の基本機能の 安定を目指すものだからです。製品の基本機能を 見誤らないことが重要で これを見抜くことに経験が 必要です。ですが、本質を見抜くことは 人生の全ての問題に 要求されることですので 逆に 品質工学を適用するために、こうした経験を積むことは 大いに意味のあることだと思います。
かつて あるテレビ番組で マツダの再生と復活を紹介したことがありました。その番組では、フォード・グループ内で 新車の開発をした時のことが紹介されていました。
その時、マツダは その開発チームでエンジンの開発を担当し、予想外に短期間に エンジン開発を終了したそうです。そのコンパクトで安定したエンジンに、他のチーム・メンバーのフォードやボルボの担当者を驚嘆させた、ということです。これが キッカケでマツダは 自らの自動車に搭載するより多い数量のエンジンを生産することになったそうです。自動車の基幹部品であるエンジンを 世界中のフォード・グループの会社に供給することになったのですが、これが マツダの収益に大きく寄与しているであろうことは 想像に難くありません。
マツダは つとに 品質工学の適用に熱心な会社であるのは有名ですが、恐らくは 品質工学で 部品ごとの基本機能のデータ・ベースを所有しており、これをベースに まずシミュレーション開発し、試作を最小限にし、設計を短期間で完了させたものと私は想像しています。
このように 各社独自の その業界に適した設計・開発の システムを持つことが 重要だと思うのですが、その際に 品質工学の手法をどこかで 使用することが決め手では ないかと思うのです。

コメント ( 2 ) | Trackback ( )

« フェッタンボ... | 井上靖の“風林... » |
私のブログで
こちらの記事を紹介させて頂きましたので
ご連絡させて頂きました。
紹介記事は
http://ko7209.blog79.fc2.com/blog-entry-236.html
です。
これからもよろしくお願いいたします^^
私の自動車情報ブログで
こちらの記事を紹介させて頂きましたので
ご連絡させて頂きました。良かったらご覧下さい。
紹介記事は
http://sinsyajyouhou.blog95.fc2.com/blog-entry-185.html
です。
これからもよろしくお願いいたします^^