製作中の溶接機の冷却水循環装置の続き、その7です。
前回に続き、大まかな配線を終えたので基本的な動作チェックと修正(デバッグ)です。
前回のブログの終わりに書いた電源ONの際に数秒間、冷却用のポンプやファンが作動してしまうというやつ。
大した事でもないし別に実害もないという微妙な存在。
でも気持ちがスッキリしないのはハッキリしている。
こんな予想外な事に対して実害がないとスルーできる人と、立ち止まって悩む人がいる。
世間では
『細かな事を気にしてたら前に進まない』だとか
『成功したいなら細かな事は気にせず前に進め』とか言う。
シグナルタワーに割り付けた青LEDの光がこんな時には反って目障りな感じ。
成功する人になりたくて、もちろんスルー。

・・・・・分かっちゃいるけど何度も電源を入り切りしてしまう。
なんにもしていないので、何も変わらない。
点かないで欲しいときに点いたり、回って欲しくないときに回るのって作り手としては鬱陶しい。
電源を入り切りしているとその間、温コンの内部リレーの音がするのと前面パネルの小さな緑色の表示が点灯している。
準備時間の間に接点がONしてるという事。
3.8Aほどあった起動電流(ピーク値)はどちらかというとファンが食うみたい。

接点がONで冷却系を起動さていたのをOFFで起動するようにリレー回路を見直して、温コンの出力動作を逆にする事で対策したけど、
そのうち何故か電源を入れてもその現象自体出なくなった。
理由は何か分からないけど新品でも無いのでそんなのもあるのかもしれない。
このままでもよかったけど不自然な回路になるので回路や設定を元に戻した。
お次はアラームについて。
流量低下時にはシグナルタワーの黄色LEDが点灯し、温度異常時は赤色LEDが点灯するようにしている。
溶接作業中はLEDが光っても気付かないと思ったのでブザーも併用することにし、ブザーを回路図に書き加えようとしたときに
気づいたのが、信号は2系統(黄色LEDと赤色LED)、ブザーは1個。
ブザーを共通にするとそのままでは片側の信号で両方のLEDが点灯してしまう。
干渉しないようにするか、ブザーを独立してそれぞれに付けなければならない。
音色を変えるとか理由があって2個にするならいいけど、意味もなく分けるのは芸が無いように思う。
干渉しないようにするには1個10円そこそこのダイオードが2個あれば済む話だけど手持ちにはなく、昔なら日本橋まで
買いに行ったけど今は面白みも無い日本橋にわざわざ行く気にもならない。
(昔は電子パーツを求めて電気屋街にオタクがいたけど、いまはオタク街にオタクがいるだけ。
電子工作が好きなんて女の子に言えない時代を過ごした自分としては、変に市民権を得た『オタク』には違和感を感じる。
がんばれ本当のオタク達)
ネットを探してマルツオンラインというショップに注文した。
25本で120円。送料が掛かるけど電車賃と変わらない。ガラス管ヒューズや熱収縮チューブも一緒に頼んだ。
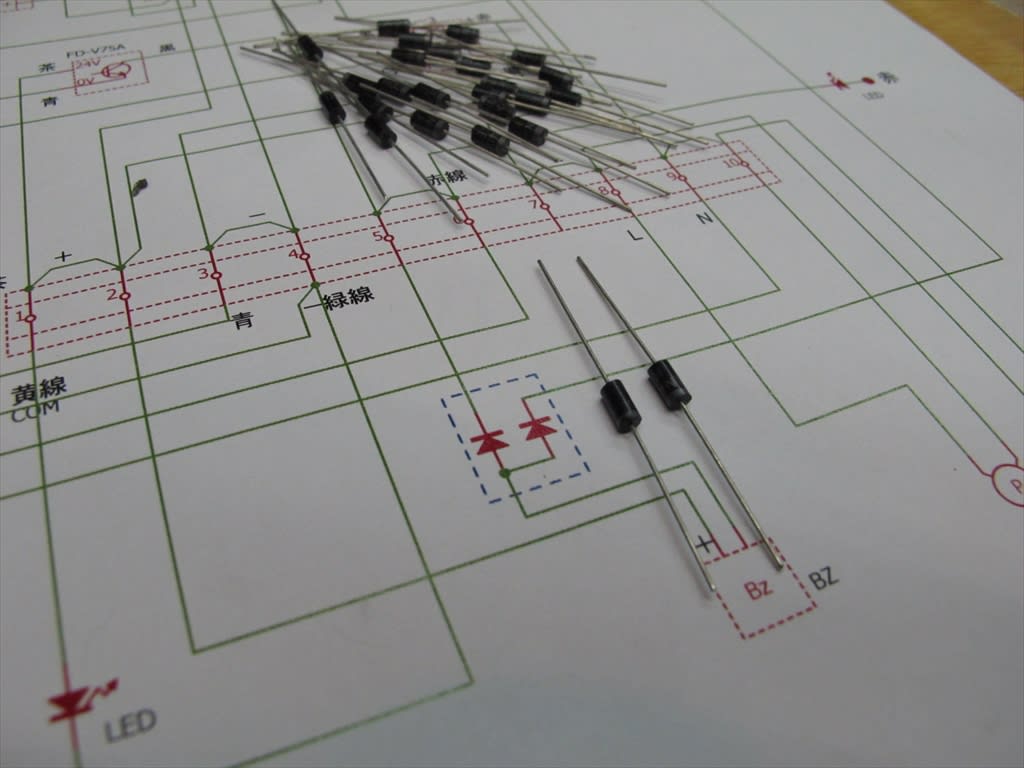
実はこれ、今年の正月2日の話。
この頃のことを今頃ブログにアップしているのも遅いといわれそうだけど、それよりも元旦に組んでいてダイオードが必要になって
早く欲しいからとあれこれ探し、2日からやっていたこのショップに注文し3日に手元についたのは驚いた。
ダイオードは熱収縮チューブに納めるため“蛇の目基板”を細長く適当に切って取り付けた。
基板は安いからと言って紙フェルールとか使うと良くないと思っている。
特に車とかバイクをいじる場合は温度も上がるので紙だと何年かしたら飴みたいにになってしまう。

昔、親父に半田付けを習った。
半田の表面がツルンとして光ったようにならないとダメだと言われた。
熱を入れすぎると光沢がなくなり半田コテを抜く際に糸を引く。
“ぬれ肌”になっているか、他人が作った基板を見る時そんな半田付けを見てしまう。

こんな小さな基板やミニチュアリレーなどを配線の途中に入れた時にその処理のことを考える。
そのまま配線の途中でぶら下げることもあるけど、小さなリレーとかはどこかに固定しておいた方がいいのではないかと思う事がある。
タイラップも有効手段だけど、そればかりではこれまた芸がない気がする。
ときどきブログの写真のバックに写り込んでいるるCB750F。
こいつをいじってた時に気付いたことで、エンジン付近のハーネスの結束はアルミ製のバンドが使われていた。
安全じゃ何じゃと言われる最近のことではなく30年くらい前のこと。
当時、ホンダはこういった所に気を配っていているなと感心したのを覚えている。
真似てみることにした。

ホンダ純正は裸のアルミのままで、形状はベルト通しがあってそこに通して折り返して固定するようになっていた。
なのでちょっとタイプ違い。
熱収縮チューブは私の優しさのおすそ分け。素材には優しく。
女性には言い寄られないけど“素材”が現実にいたらきっと好かれているだろうと思っている。ああ妄想・・・・。
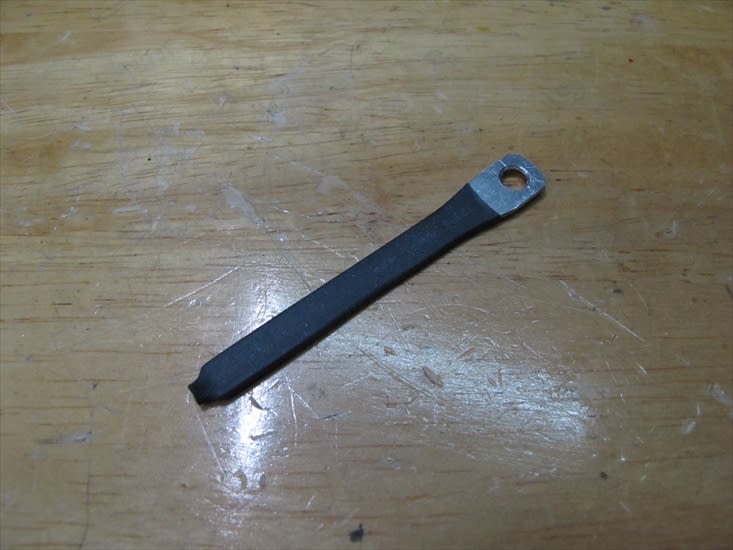
ミニチュアリレーに巻き付けて近くにあったターミナルのネジで固定した。
安心してリレーが動作してくれそうに思う。 ああ妄想・・・

来客あり。

二つ目の問題というか課題は、温度が上がって冷却系のポンプが起動した際、流量が上がって設定流量を超えるまで流量低下で
アラームが鳴ってしまう。
ほんの1秒ほど。なのでこれもさほど問題では無いけれど、冷却系が立ち上がる度にアラームが鳴るのは格好いいものではない。
ものの出来上がりを考えた時に、自分一人だとこんなことはきっと自分の中で消化してしまう。
これが仮に誰か第三者がいて、『今の音、何?』って聞かれたらあれこれ説明する羽目になる。
それは格好悪いし、それこそ完成度の低い機械ということになる。
これは遅延させるしかない。
“大人のおもちゃ箱”から遅延リレーを見つけだして回路に追加した。

1.5秒ほど遅延させると流量低下で引っかからなくなった。
動作的にはステキになった。何か嬉しい。
できればステキな女性も言い寄ってきて欲しい。 ああ願望。

温コンや流量センサーの出力は大抵、『抵抗負荷』となっている。
ヒーターなどは抵抗負荷だけどモーターなどは誘導負荷で突入電流が大きい。
壊れたら簡単に買い換えるほど資金をガレージワークに充てれないので壊れないように、それと何より機器に優しいようにとメーカーの指定に従い、
一旦小型リレーで受けてからモーターを駆動させている。
そんなことをしたり、余計な機能を増やしたため、電気部品の構成がごちゃついてしまった。

カバーは相変わらず何かに使っていたモノを再利用。
傷もあるけど懐にはやさしい。
冷却ファンが熱気をはき出すために側面のカバーにホールソーで空気取り入れ口を開けた。

冷却水の水は腐敗するため定期的に入れ替えが必要。
なのでその面のパネルは手で回せるネジにした。

職場に装置のメンテナンスをする人がいて、手袋をした手でやりにくそうに、パネルのネジをしょっちゅう緩めて開け閉めしていた。
お世話になっている人だったので作業性が良くなるようにとネジにちょっと細工してあげた。
ネジの先端を殺す。

ネジを殺した部分が案内役になり、スゥ~っとねじ穴に入ってくる。
ネジ部も必要なところだけ残すことで、無用にねじを回さなくてすむ。

自分のにも同じ事をした。

便利で効率的になるものは、ちょこっとしたことでも作っていて楽しい。
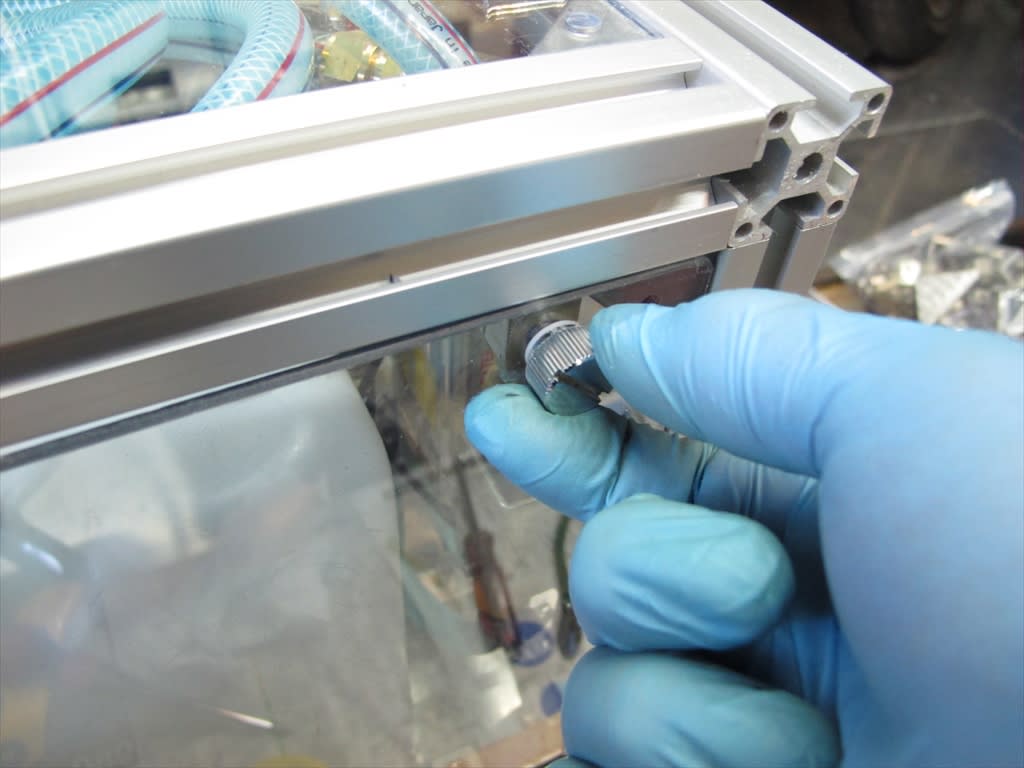
熱交換器の高さを上げたため背面のパネルを作り直したけど、ファンの開口径がちょっと大きくなってしまいブサイクになってしまった。
それをご近所の工作友達のkagayakiさんに見つかってしまった。

あまりの“ぶちゃいくさ”に同情してくれたのか、自作のCNCフライス盤でお洒落なファンカバーを作ってくれた。
材料はペット樹脂と言っていた。
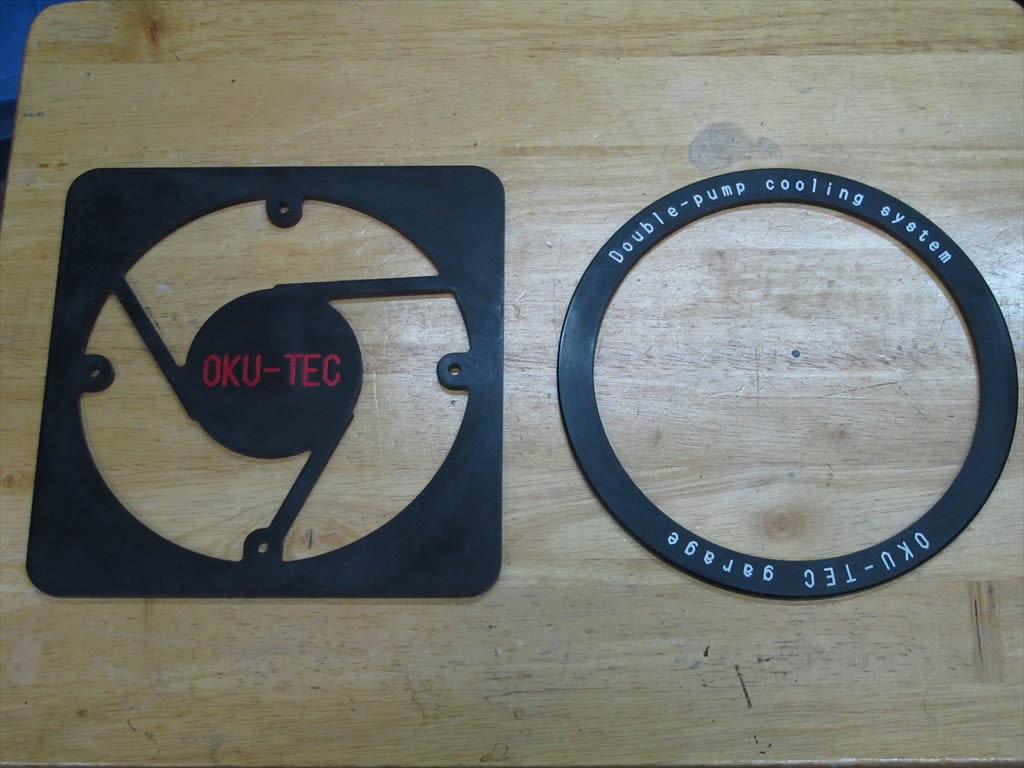
『Double-pomp cooling system』
名前負けしそうなネーミング。
実はこれを見てちゃんと作らないといけないと思った。
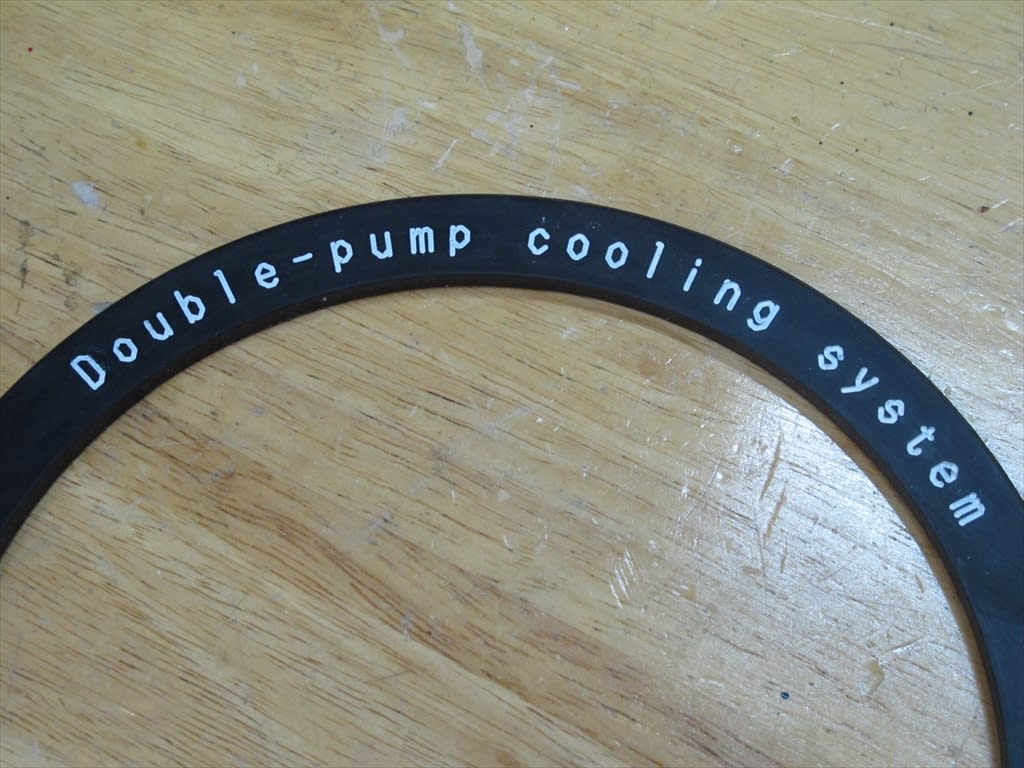
ファンと背面パネルには隙間があるので旋盤でカラーを作ってみた。

引き締まった感がして稚拙な機械がかっこよく見えた。

アレコレ触っていて怒られて、しょげた。

随分掛かりましたが機械的には一応完成しました。
これから溶接機に接続して本当に使い物になるか検証していきます。

お次は溶接機本体とこの冷却水循環装置を載せるラックを作ります。
続きはまた今度。
前回に続き、大まかな配線を終えたので基本的な動作チェックと修正(デバッグ)です。
前回のブログの終わりに書いた電源ONの際に数秒間、冷却用のポンプやファンが作動してしまうというやつ。
大した事でもないし別に実害もないという微妙な存在。
でも気持ちがスッキリしないのはハッキリしている。
こんな予想外な事に対して実害がないとスルーできる人と、立ち止まって悩む人がいる。
世間では
『細かな事を気にしてたら前に進まない』だとか
『成功したいなら細かな事は気にせず前に進め』とか言う。
シグナルタワーに割り付けた青LEDの光がこんな時には反って目障りな感じ。
成功する人になりたくて、もちろんスルー。

・・・・・分かっちゃいるけど何度も電源を入り切りしてしまう。
なんにもしていないので、何も変わらない。
点かないで欲しいときに点いたり、回って欲しくないときに回るのって作り手としては鬱陶しい。
電源を入り切りしているとその間、温コンの内部リレーの音がするのと前面パネルの小さな緑色の表示が点灯している。
準備時間の間に接点がONしてるという事。
3.8Aほどあった起動電流(ピーク値)はどちらかというとファンが食うみたい。

接点がONで冷却系を起動さていたのをOFFで起動するようにリレー回路を見直して、温コンの出力動作を逆にする事で対策したけど、
そのうち何故か電源を入れてもその現象自体出なくなった。
理由は何か分からないけど新品でも無いのでそんなのもあるのかもしれない。
このままでもよかったけど不自然な回路になるので回路や設定を元に戻した。
お次はアラームについて。
流量低下時にはシグナルタワーの黄色LEDが点灯し、温度異常時は赤色LEDが点灯するようにしている。
溶接作業中はLEDが光っても気付かないと思ったのでブザーも併用することにし、ブザーを回路図に書き加えようとしたときに
気づいたのが、信号は2系統(黄色LEDと赤色LED)、ブザーは1個。
ブザーを共通にするとそのままでは片側の信号で両方のLEDが点灯してしまう。
干渉しないようにするか、ブザーを独立してそれぞれに付けなければならない。
音色を変えるとか理由があって2個にするならいいけど、意味もなく分けるのは芸が無いように思う。
干渉しないようにするには1個10円そこそこのダイオードが2個あれば済む話だけど手持ちにはなく、昔なら日本橋まで
買いに行ったけど今は面白みも無い日本橋にわざわざ行く気にもならない。
(昔は電子パーツを求めて電気屋街にオタクがいたけど、いまはオタク街にオタクがいるだけ。
電子工作が好きなんて女の子に言えない時代を過ごした自分としては、変に市民権を得た『オタク』には違和感を感じる。
がんばれ本当のオタク達)
ネットを探してマルツオンラインというショップに注文した。
25本で120円。送料が掛かるけど電車賃と変わらない。ガラス管ヒューズや熱収縮チューブも一緒に頼んだ。
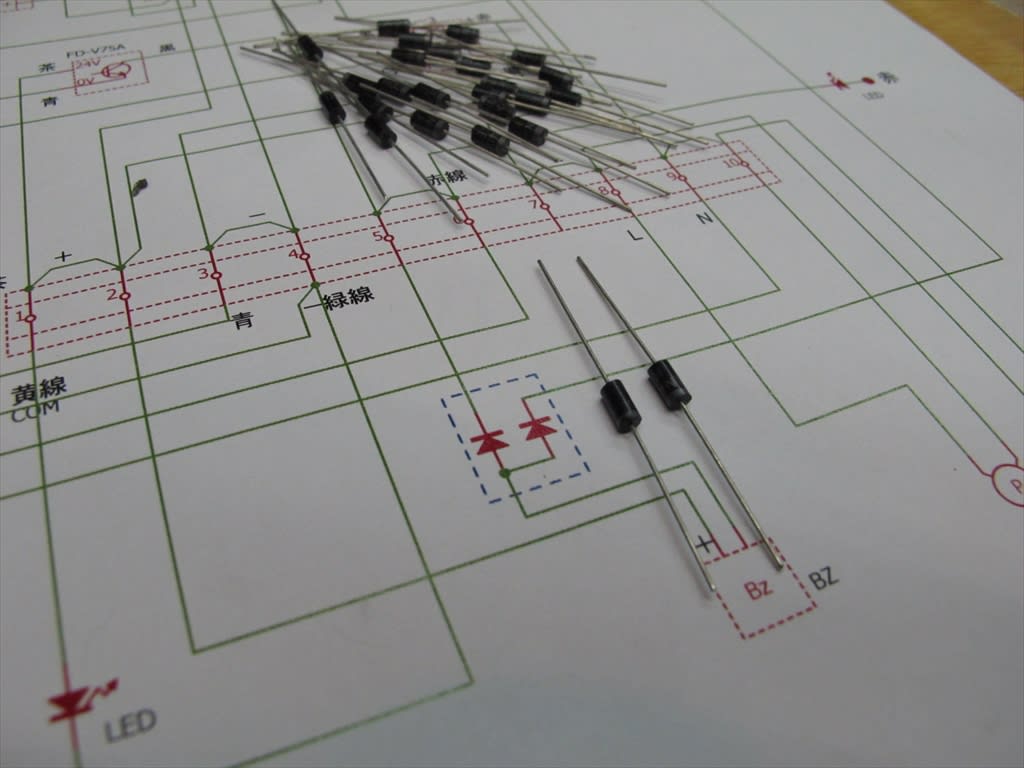
実はこれ、今年の正月2日の話。
この頃のことを今頃ブログにアップしているのも遅いといわれそうだけど、それよりも元旦に組んでいてダイオードが必要になって
早く欲しいからとあれこれ探し、2日からやっていたこのショップに注文し3日に手元についたのは驚いた。
ダイオードは熱収縮チューブに納めるため“蛇の目基板”を細長く適当に切って取り付けた。
基板は安いからと言って紙フェルールとか使うと良くないと思っている。
特に車とかバイクをいじる場合は温度も上がるので紙だと何年かしたら飴みたいにになってしまう。

昔、親父に半田付けを習った。
半田の表面がツルンとして光ったようにならないとダメだと言われた。
熱を入れすぎると光沢がなくなり半田コテを抜く際に糸を引く。
“ぬれ肌”になっているか、他人が作った基板を見る時そんな半田付けを見てしまう。

こんな小さな基板やミニチュアリレーなどを配線の途中に入れた時にその処理のことを考える。
そのまま配線の途中でぶら下げることもあるけど、小さなリレーとかはどこかに固定しておいた方がいいのではないかと思う事がある。
タイラップも有効手段だけど、そればかりではこれまた芸がない気がする。
ときどきブログの写真のバックに写り込んでいるるCB750F。
こいつをいじってた時に気付いたことで、エンジン付近のハーネスの結束はアルミ製のバンドが使われていた。
安全じゃ何じゃと言われる最近のことではなく30年くらい前のこと。
当時、ホンダはこういった所に気を配っていているなと感心したのを覚えている。
真似てみることにした。

ホンダ純正は裸のアルミのままで、形状はベルト通しがあってそこに通して折り返して固定するようになっていた。
なのでちょっとタイプ違い。
熱収縮チューブは私の優しさのおすそ分け。素材には優しく。
女性には言い寄られないけど“素材”が現実にいたらきっと好かれているだろうと思っている。ああ妄想・・・・。
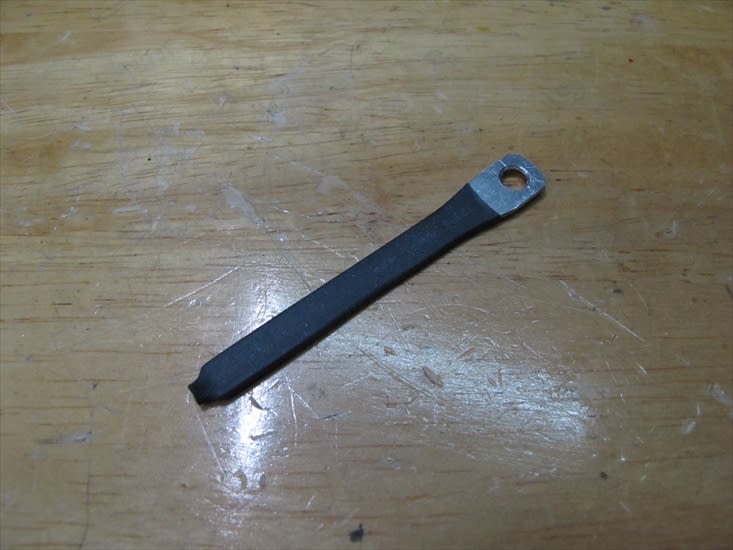
ミニチュアリレーに巻き付けて近くにあったターミナルのネジで固定した。
安心してリレーが動作してくれそうに思う。 ああ妄想・・・

来客あり。

二つ目の問題というか課題は、温度が上がって冷却系のポンプが起動した際、流量が上がって設定流量を超えるまで流量低下で
アラームが鳴ってしまう。
ほんの1秒ほど。なのでこれもさほど問題では無いけれど、冷却系が立ち上がる度にアラームが鳴るのは格好いいものではない。
ものの出来上がりを考えた時に、自分一人だとこんなことはきっと自分の中で消化してしまう。
これが仮に誰か第三者がいて、『今の音、何?』って聞かれたらあれこれ説明する羽目になる。
それは格好悪いし、それこそ完成度の低い機械ということになる。
これは遅延させるしかない。
“大人のおもちゃ箱”から遅延リレーを見つけだして回路に追加した。

1.5秒ほど遅延させると流量低下で引っかからなくなった。
動作的にはステキになった。何か嬉しい。
できればステキな女性も言い寄ってきて欲しい。 ああ願望。

温コンや流量センサーの出力は大抵、『抵抗負荷』となっている。
ヒーターなどは抵抗負荷だけどモーターなどは誘導負荷で突入電流が大きい。
壊れたら簡単に買い換えるほど資金をガレージワークに充てれないので壊れないように、それと何より機器に優しいようにとメーカーの指定に従い、
一旦小型リレーで受けてからモーターを駆動させている。
そんなことをしたり、余計な機能を増やしたため、電気部品の構成がごちゃついてしまった。

カバーは相変わらず何かに使っていたモノを再利用。
傷もあるけど懐にはやさしい。
冷却ファンが熱気をはき出すために側面のカバーにホールソーで空気取り入れ口を開けた。

冷却水の水は腐敗するため定期的に入れ替えが必要。
なのでその面のパネルは手で回せるネジにした。

職場に装置のメンテナンスをする人がいて、手袋をした手でやりにくそうに、パネルのネジをしょっちゅう緩めて開け閉めしていた。
お世話になっている人だったので作業性が良くなるようにとネジにちょっと細工してあげた。
ネジの先端を殺す。

ネジを殺した部分が案内役になり、スゥ~っとねじ穴に入ってくる。
ネジ部も必要なところだけ残すことで、無用にねじを回さなくてすむ。

自分のにも同じ事をした。

便利で効率的になるものは、ちょこっとしたことでも作っていて楽しい。
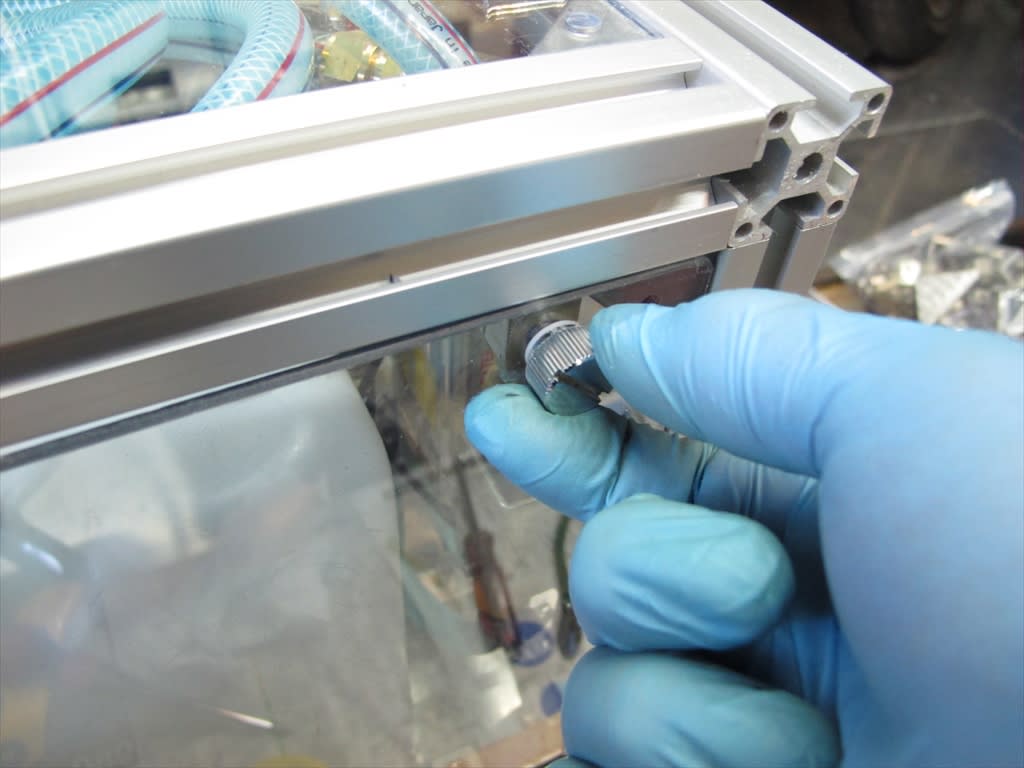
熱交換器の高さを上げたため背面のパネルを作り直したけど、ファンの開口径がちょっと大きくなってしまいブサイクになってしまった。
それをご近所の工作友達のkagayakiさんに見つかってしまった。

あまりの“ぶちゃいくさ”に同情してくれたのか、自作のCNCフライス盤でお洒落なファンカバーを作ってくれた。
材料はペット樹脂と言っていた。
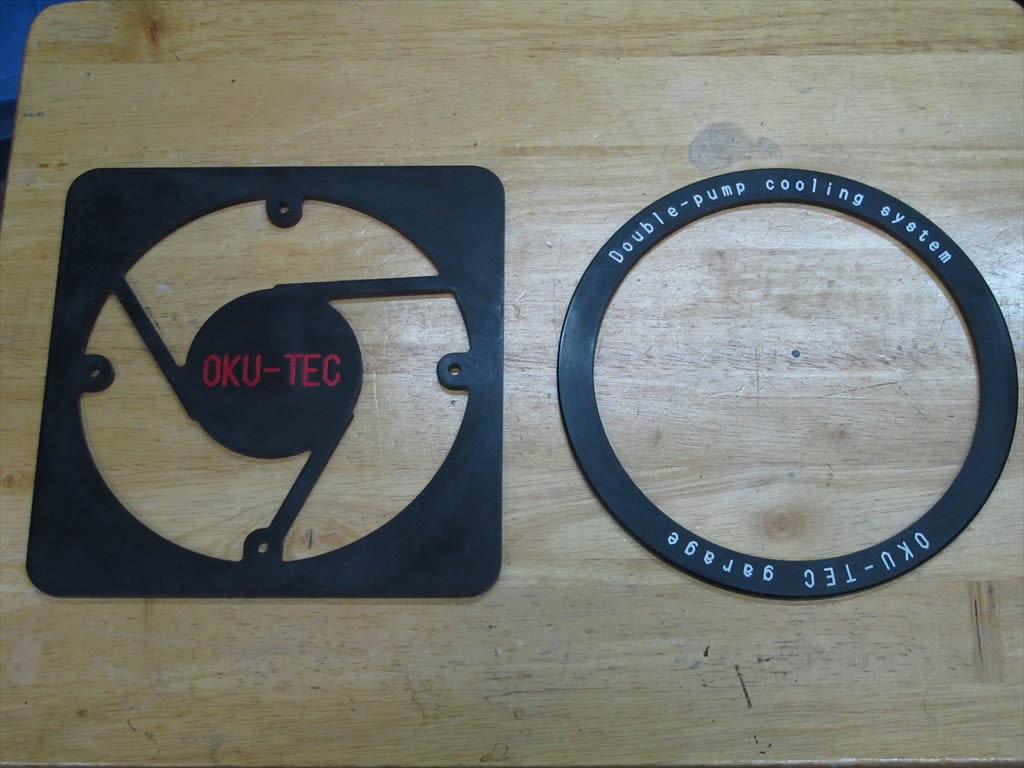
『Double-pomp cooling system』
名前負けしそうなネーミング。
実はこれを見てちゃんと作らないといけないと思った。
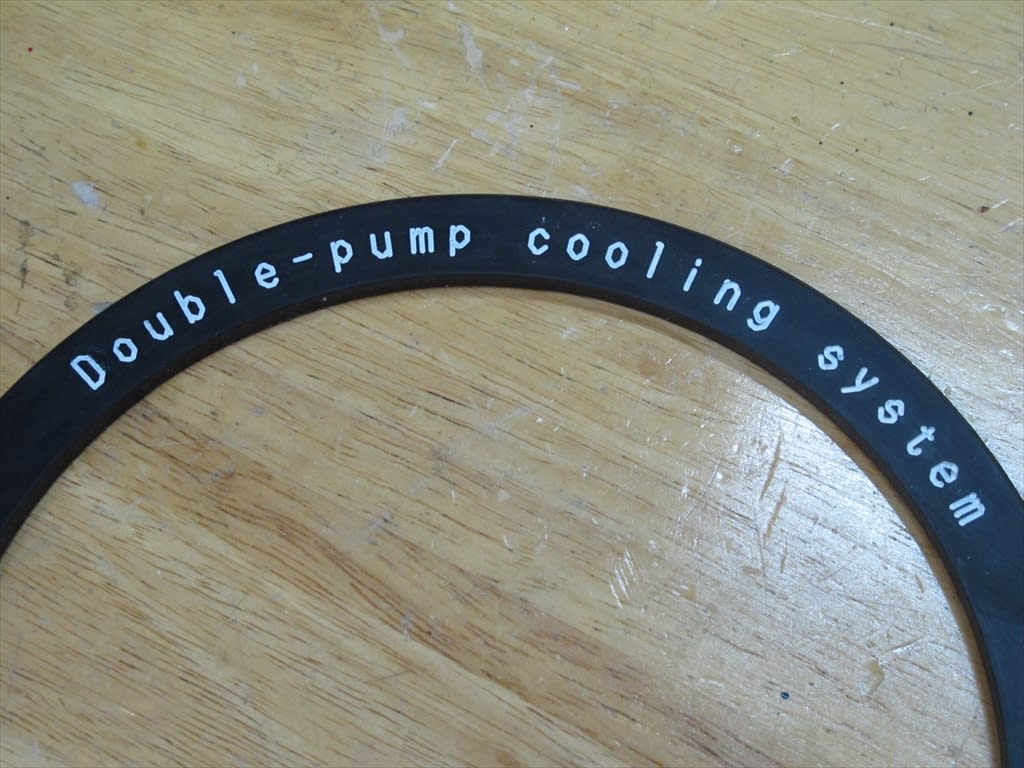
ファンと背面パネルには隙間があるので旋盤でカラーを作ってみた。

引き締まった感がして稚拙な機械がかっこよく見えた。

アレコレ触っていて怒られて、しょげた。

随分掛かりましたが機械的には一応完成しました。
これから溶接機に接続して本当に使い物になるか検証していきます。

お次は溶接機本体とこの冷却水循環装置を載せるラックを作ります。
続きはまた今度。