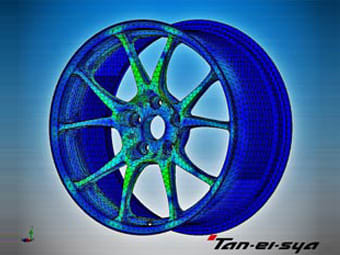
今回の鍛造15インチホイールへのお問い合わせ有難う御座います。
アルミ鍛造製法に関してのご質問が幾つかありましたので少しばかり
Tan-Ei-Syaさんの鍛造製法のご紹介です。
古くは日本刀に代表される鍛造技術、日本の鍛造製造技術は
世界的に見てもトップクラスでそのシェア占有率も圧倒的です。
70年代後半に創業した鍛栄舎さん、80年代初頭に豊富な水力発電に
恵まれた富山県に本社工場を構え、軽量&強度という相反する目標を
徹底的に追求してきてます。
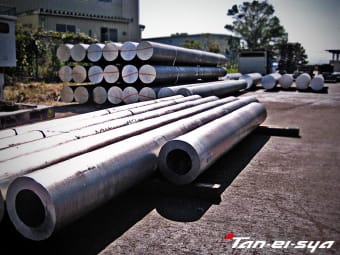
一見、電信柱?! アルミ原材料を円形状に固めたビレット。
このビレットをカットして鍛造前に熱処理されます。
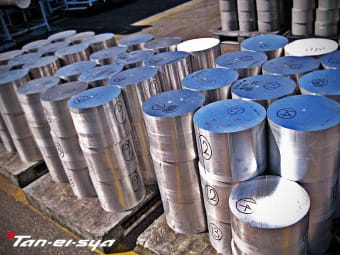
同社では、アルミニウム AL 6061(メイン), 6000系 高強度素材,2000系,5000系,7000系
マグネシウム AZ 80(メイン),その他Mg合金
その他、銅,チタンなどを扱ってます。
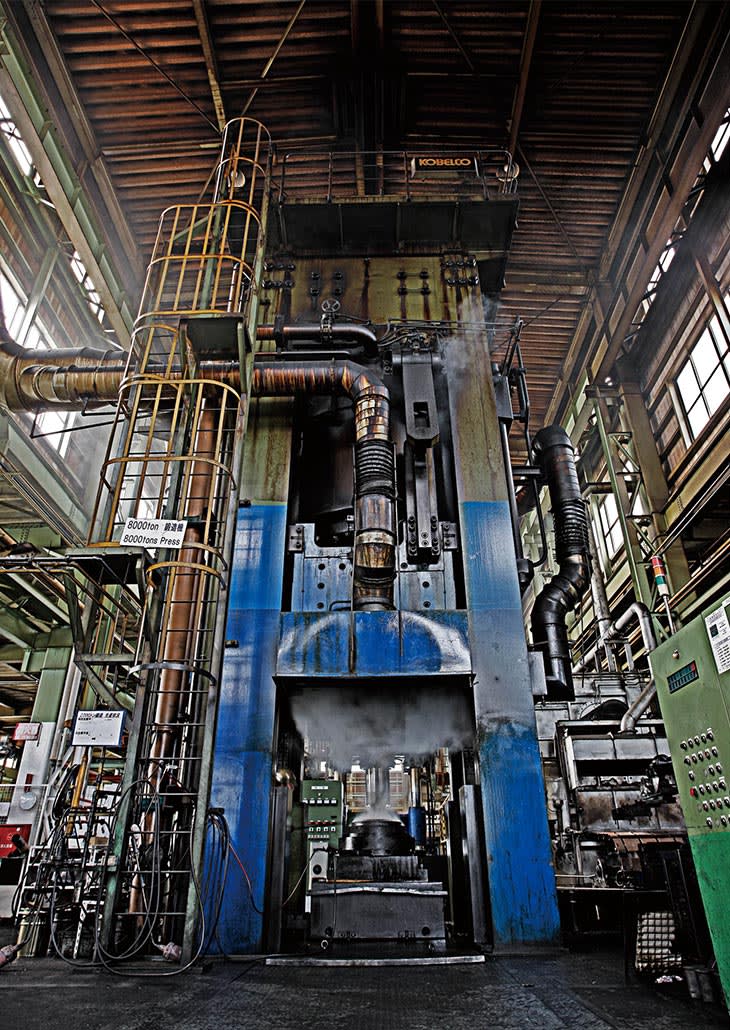
8000tと6000tの加圧能力を誇るプレスマシン、途轍もない迫力です。
この工程で連続した鍛流線を形成、結晶を微細化し、結晶の方向を整えて
鋳造製法では得られない剛性を生み出します。
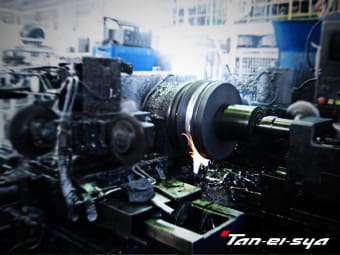
同社独自の冷間裂開。
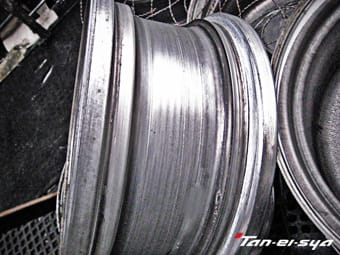
「裂開」「スピニング」とは、ろくろを使って陶芸をするイメージで、鍛造後の
素材をローラーでリム幅を伸ばすと同時に圧延する加工技術です。
これらの加工は、時間も手間もかかる難しい技術ですが、素材のさらなる
強度アップのため、こだわる独自の特別な加工技術です。
MT-DRACOがベストと考える 『裂開鍛造』 ですね^^;
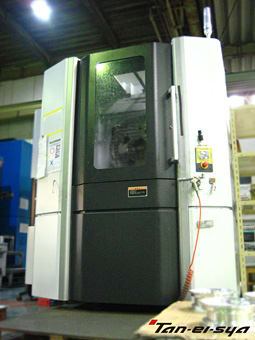
NC旋盤、マシニングセンター。
私の大好き?! な5軸旋盤!
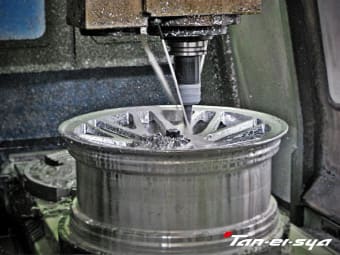
大量生産品の鍛造用金型を用いて鍛造する型鍛造に比較して
より高い寸法精度を追求するとNC・MC加工となります。
同社では、24インチまで対応する大型NC旋盤と5軸マシニングセンタを
導入し、さらなるデザイン再現性を確立しています。
特に、鍛造17インチのRS209A&Bはこの切削工程で通常製品の
4~5倍の手間暇と時間が掛かってしまってます(=お高くなっちゃいます)
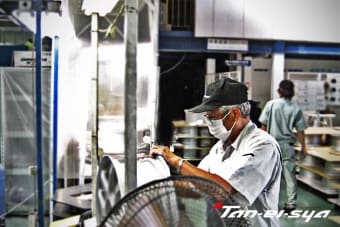
仕上げ加工。
意外に思われるかもしれませんが、切削後の製品には鋭利な部分が
どうしても出来てしまいます。
形状によりマシニングの際にプログラムを組んで一緒に取ってしまいます
が、完全ではありません。
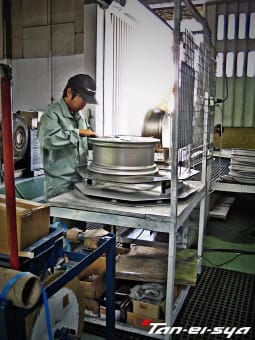
切削後は1本1本、職人が熟練の技で丁寧に仕上げていきます。
この工程がなかなか手間暇が掛かる部分ですがとても重要なプロセス。
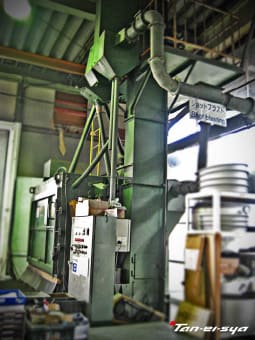
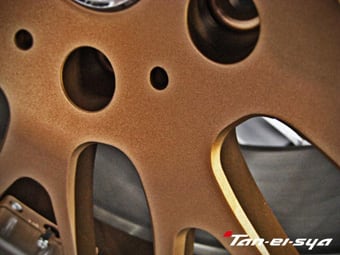
表面処理には色々な手法がありますが・・・
ブラッシュド、ポリッシュ以外の製品には、ショットブラストという技術を
用います。
数ミリのステンレスカットワイヤを毎秒数百メートルの高速で材料の表面に
ぶつけることで、残留圧縮応力を与え、耐疲労性の向上と表面を整えてい
きます。
それに伴いできあがった、ディンプル状の模様を利用した新しい
表面テクスチャの提案もしています。
冷間直巻きのスプリングも同様の表面処理加工してます。
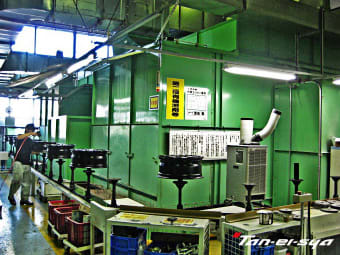
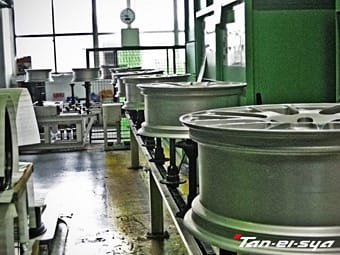
粉体焼付塗装。
ショットブラストが終了した製品は洗浄され、粉体焼き付け塗装で下地を
作っていきます。 塗装前の皮膜処理は、従来のクロム酸化皮膜から
ノンクロ皮膜へと変更し、環境問題に配慮しています。
その後の通常製品には、1コート(塗装)につき1ベーク(焼き付け)を必ず行
います。
通常商品には3コート、3ベークを行ってます。
表面処理。
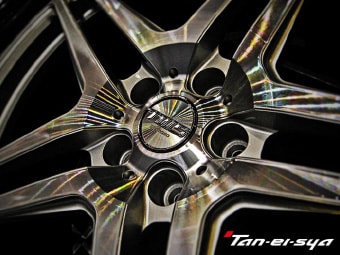
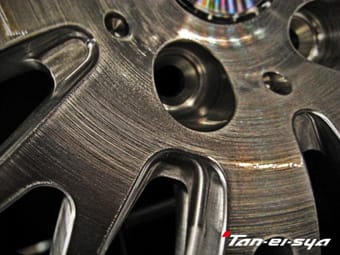
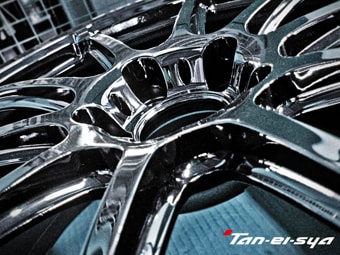
表面処理に関しては様々な方法があり、又私自身が知らない新技術があ
ると思いますが・・・
ダイヤモンドカット、アルマイト、ブラッシュド、乾式&湿式ポリッシュ、
スパッタリング等々。
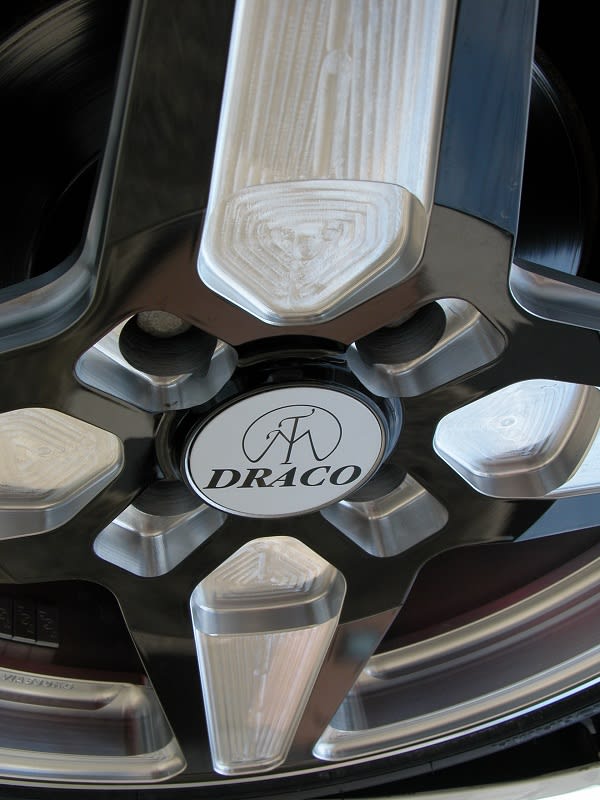
この表面処理工程、RS209Aの場合はポリッシュ~クリア2コート~
硬質アルマイト処理といった工程で通常の10倍の手間暇掛けてます。
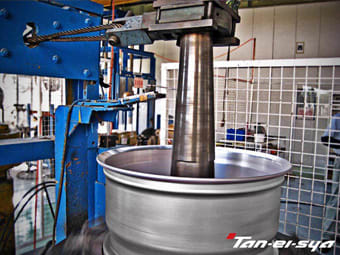

品質管理。
「高剛性」、「軽量化」という相反するものを、高次元で両立させる為、同社
ではJWL規格※1、JWL-T規格※2の定める厳格な数値をクリアし、
なおかつ同社独自基準の+α試験を全製品に実施しています。
※1:運輸省通達「乗用車用軽合金製ディスクホイールの技術基準」の安全基準
※2:貨物自動車および大型自動車向けアルミホイールの安全基準
今さらながらに私自身が思うのですが・・・
こんな重厚長大な製造工程でよくもまあとんでもない少量生産を
無理くり行っているもんだと思う今日この頃でした^^;
未だ、確定ではありませんが RSC252A Falcone 鍛造15インチ
ホイール、次回セカンドロットの計画も検討しなければいけないかも・・